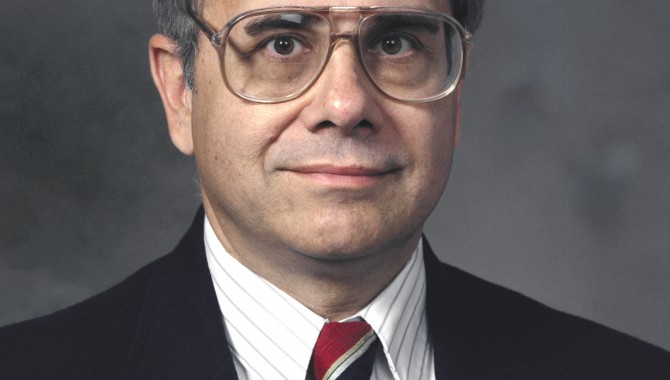
By Don Cohen
Dr. Kenneth Szalai led the Dryden Flight Research Center from 1990 to 1998. Earlier in his career at Dryden, he was principal investigator on the F-8 digital fly-by-wire program and participated in many X-plane aircraft programs.
COHEN: I’ve heard you talk forcefully about the value of flight programs. What makes them so valuable?
SZALAI: I strongly support the flight aspect of the NASA aeronautics program because it is a primary means of discovery in aeronautics, and it is the truth serum and the lie detector of what is possible or not. Flight provides the real answer. You can’t say, “It worked,” when there is a cloud of black smoke coming up from the desert floor. And, in the process of doing it successfully, you provide a level of confidence to other people. Burt Rutan once said something very profound about SpaceShipOne: “Other people will say, ‘If a guy out here on the Mojave Desert can put the equivalent of a three-person spaceship above a hundred kilometers, bring it back safely, and then do it again within a week, I should be able to do that.’”
COHEN: What’s an example of that kind of project at Dryden?
SZALAI: When we did the digital fly-by-wire program, a prominent executive of a major aerospace company said, “That gave us the confidence to bid fly-by-wire in our proposal.” He said that without having read any of the reports. We gave a three-day seminar to regulatory people in the eighties where we said, “Digital fly-by-wire is coming, and this is to assist you in what you will be dealing with.” Many of the people present there said, “This will never happen.” But look at the 787 and A380—they’re fly-by-wire airplanes.
COHEN: Because you showed it could work.
SZALAI: And also because we showed the enormous benefits of digital flyby- wire [DFBW]. In some ways, it was reverse technology transfer from space to aeronautics. The technology transfer for human-rated software went from the Apollo moon-landing program to Dryden, and then from Dryden to the aircraft industry. For the first phase of the F-8 DFBW project we used the Apollo lunar guidance computer and inertial navigation system. Because of that, Dryden became the first NASA research center to tap into the tremendous national treasure of processes, techniques, and procedures for flight software development for human-rated vehicles. This had been developed by the Charles Stark Draper Laboratory. The biggest two findings of the first phase of the F-8 program were, first, that digital fly-by-wire is possible and, second, that the task of human-rated software development is so complex and challenging that it will become the pacing element for all aircraft digital flight control systems. In the second phase, we essentially invented how to make multiple computers that work together for fault tolerance look like one computer to the pilot. One of the eye-openers in the F-8 program was that you can exercise the software to the nth degree in the simulator, test every path, test every function, and test as much as you can until you’ve reached the point where you’re not finding any more errors. But what happened when we started flying in August of 1976? We started finding software issues. I say “issues” because sometimes it was a specification error, sometimes it was an interpretation error, sometimes it was just something everyone overlooked. None of these issues ever showed up in flight, but they could have. By the way, I was lucky enough to be the chief engineer and principal investigator on the project. I was in the right place at the right time.
COHEN: Another example of the power of flight to convince skeptics?
SZALAI: Early in the Space Shuttle development, designers were still considering air-breathing engines on the Space Shuttle to give it go-around capability or add power if you were a little short, just like an airplane. After all, the crew has one attempt at landing if it has no power. But just imagine, now, if you had to carry a turbojet or turbofan engine or two on the shuttle orbiter with all its systems and all the fuel and all the controls and supporting avionics. What do you think the payload would be? That might have been the payload. At that time, Milt Thompson, who was an X-15 pilot and a brilliant engineer as well as Dryden chief engineer, was saying to a lot of the Johnson Space Center people, “You know, you can do this all unpowered. We have proven that with the X-15 and the lifting bodies. We did unpowered approaches and landings safely and consistently.” But this was a big step to take with the nation’s newest human spacecraft. Many of the space people were a generation beyond the aeronautics group that started the space program. The shuttle program management said, “You’ve been landing the X-15 and the lifting bodies on this enormous lake bed, fifteen miles long and eight miles wide. We’ve got to land on a runway.” So Milt Thompson led an effort to do a convincing demonstration. Dryden launched the X-24B from a B-52 and went out about seventy miles supersonic. The rocket engine burns out, and then they come back from seventy miles and try to hit a new line painted on the runway. That’s a very high-precision task. John Manke, the test pilot who became the director of Dryden in ’81, hit the line. Maybe he missed it by five feet. Then Mike Love, who tragically later lost his life in an F-4 accident, repeated the flight with about the same precision. The shuttle people were amazed. That turned the tide. No one was going to change the shuttle to be a glider from orbit because someone in a simulator says, “I think we can do this.” By the way, an Ames pilot, Fred Drinkwater, was a key player in this program as well, developing low lift-to-drag approach and landing techniques using a large transport aircraft.
Of course, the Dryden lifting body program had its own objectives: exploring aerodynamics and handling qualities for hypersonic reentry vehicles. It produced its own technology and a tremendous amount of data. But arguably one of the most significant contributions to date is what it did for shuttle, which was never envisioned in the lifting body program plan. It’s true that you can’t start a program saying, “Fund this program because maybe in the future something important will come out of it,” but any leading-edge program is almost guaranteed to produce new understanding, new concepts, new ideas, as well as “to separate the real from the imagined and to make known the overlooked and the unexpected problems,” as Dr. Hugh Dryden stated when asked about the reason for flight research.
COHEN: You learn things that you can’t learn through simulation?
SZALAI: You can’t do everything in a simulator; you can’t do it in a lab. We have a tremendous amount of computational capability today, and it plays a dominant role in design and analysis. But given this level of capability in analysis, some thinking goes like this: “With computational tools, simulators, and labs, we can pretty much do everything on the ground. Then, if we have enough money and if there’s interest, and if we have to, we can fly something to validate our concepts at the end.” In all the years I was involved in flight research, we never had a program like that. Flight research is really flights of discovery. You use the flight vehicle as a pioneer and a probe to find out where we are in terms of understanding and to uncover the gaps in understanding. A major purpose of flight research is to develop, tune, and validate the computational tools and ground facilities for future use in design and analysis. Many of the flight programs of the past produced critical data for both wind tunnel and computational people to develop their capabilities.
COHEN: How, for instance, has flight developed wind tunnel capabilities?
SZALAI: Let me give you a basic example. It’s a big deal in aerodynamics when flow transitions from laminar [smooth] to turbulent. In an aircraft it affects drag; it affects performance. In a spacecraft it dramatically affects heating. One of the things noted in flight is that the natural latent turbulence levels are very low, lower than in most wind tunnels. Why is that? In flight, in smooth air, there is no fan blowing the air across the airplane. In a wind tunnel, you have to make the wind move. Large fans create a flow that goes around corners and bounces off the walls. It’s complicated. NASA and others have spent years learning how to make quiet tunnels—that is, low-turbulence tunnels—so we could design and analyze laminar flow. A stainless steel cone, heavily instrumented to determine when you go from laminar flow to turbulent flow, was traded among wind tunnels to calibrate them. In some tunnels, the flow transitioned at relatively low speed. That meant the tunnel was quite “noisy,” it had a lot of turbulence in its flow. Some were better. Years ago at Dryden we took this cone and put it on the front of an F-15, to fly it in “real life.” The transition Reynolds number, which indicates when transition occurs, was higher than it had been in virtually all the wind tunnels. In other words, smooth air conditions could not be completely duplicated on the ground. As a result of that flight experiment, wind tunnels were calibrated, tuned, and analyzed to make them better. Knowing how the wind tunnels differed from actual flight meant you could apply a correction factor. There’s an example of discovery, not validation. That’s what flight programs are for. Most are much more complex than carrying a cone on the nose boom.
For the Space Shuttle, and for next-generation aircraft and spacecraft, we use the same wind tunnels that had been validated over the years with aircraft, so that gives you a high degree of confidence. If you had no aeronautical legacy, you’d have to validate the tunnel for new conditions or environments while you were trying to design a new vehicle. The interference effects and the unsteady aerodynamics of the Space Shuttle stack— such large vehicles so close together flying subsonically, transonically, and supersonically—are so complex that they defy prediction to some degree. There was more than 100,000 hours of wind tunnel testing. We had to rely on these tunnels, validated over years of experience and validation in flight, because one could not do simple flight tests to predict the actual shuttle configuration. When you fly transonically—0.9 mach number to maybe 1.1 mach number—early wind tunnels had tremendous problems because the shock wave bounces off the walls and hits the vehicle, whereas in free air it never comes back. So you get erroneous data. Through a lot of flight research in the early days and flight tests and calibration of wind tunnels, some clever people came up with both perforated and slotted walls so that the shock is swallowed. But for complex configurations in new flight regions, flight research also often finds the terms in the equation that you have left out on the ground.
COHEN: For example?
SZALAI: Sometimes it’s something in the interaction between the pilot and the vehicle. Take the Space Shuttle again. The first landing to the runway, flight number five of Enterprise, resulted in a serious pilot-induced oscillation [PIO] in both roll and pitch. There was a complicated interaction between the pilot, the vehicle, the flight control system, the visibility out the front, and the configuration of the shuttle that led to a pilot-induced oscillation. The roll PIO was not too much of a technical challenge and was solved by reallocating control functions to the elevons. But the pitch PIO was a bad problem. Even after it was found on the Space Shuttle, even knowing it was there, it couldn’t be duplicated on ground simulators. The only duplication of a sort that was done was on the F-8, where we replicated the flight control system and the time delay and had a real pilot try to land a real airplane on a real runway. That’s where the PIO exhibited itself. There’s no substitute for the real environment.
COHEN: Dryden took a major role in the SOFIA [Stratospheric Observatory for Infrared Astronomy] program fairly recently.
SZALAI: SOFIA has a flight development phase required to complete the development, integration, and qualification of the overall systems on the aircraft, including a fail-safe system to open an enormous cavity in an airplane above 45,000 ft. at high subsonic speeds. This effort will draw on all the things for which Dryden has a high degree of expertise and experience, namely acoustics, fault-tolerant flight systems, flight controls, dynamics, turbulence, and, above all, safety. There’s no book written on how to do this program. Dryden can draw on its deep flight research experience in dozens and dozens of projects to do this work. They know how to do this kind of project. It’s a national asset to have that kind of experience within an organization. An aircraft company can’t afford to do its own national flight research program. NASA Dryden, as a national facility, has probably worked on more than a hundred airplanes. After fifteen or twenty years most Dryden people end up working on ten or twenty flight programs. But this does not mean that Dryden works independently of the aerospace industry—it works closely with them and each brings its experience to the program. The best way for the industry to attain the technology developed in our programs is to work in close cooperation with NASA as major contractors. Bell Aerospace was the prime contractor on the X-1, North American Aviation on the X-15, and Grumman on the X-29. They designed the aircraft and fully participated in the flight research programs.
NASA is supposed to do hard things that the industry is not yet ready to undertake as a product or commercial venture. I remember President Kennedy saying, “We do things not because they’re easy but because they’re hard.” Dr. Ken Iliff, who was the chief scientist at Dryden, used to tell me there were three piles you should put your programs into: the easy ones, the things you’re sure you can do; the too-hard ones that you shouldn’t even try; and then there’s the question-mark pile. That’s where Dryden fits in. You shouldn’t try to do something too easy or too hard. If it’s too easy, probably somebody else should be doing it commercially. The impossible may look different some day, but warp drives and anti-gravity machines are not programs for the president to announce or for Dryden to work on yet.
COHEN: What is a Dryden accomplishment few people are likely to know about?
SZALAI: Dryden developed an integrated flight propulsion control system for the SR-71, which showed that you could improve the range of the airplane by 7 percent just by properly integrating the control of the engine and inlets, and the control of the airframe. Dryden and engine companies collaborated on digital engine controls and adaptive engine controls for high-performance aircraft. In another program, Dryden developed control system concepts that made it possible to fly and land an aircraft with severe damage or massive failures.
COHEN: Where do you see flight testing being important in the future?
SZALAI: One area in the near term will be work on more environmentally friendly airplanes. This includes issues of synthetic fuels, noise, and emissions that contribute to undesirable constituents in the atmosphere. There’s a lot to be learned about alternate fuels. Nobody knows what happens to an engine after years on synthetic fuel. What are the effects on maintenance? What happens to fuel that’s stored in a tank farm for a long time? What is a long time? Does a synthetic fuel degrade differently from JP [jet propellant]? What happens if it slightly degrades? Can you still use it? If you optimize the aerodynamics for something that doesn’t have a “green” engine and then you put a green engine on it, do you still get the same benefits? There’s an enormous role for flight to explore these things. Not to validate them years downstream, but to be part of the exploration and discovery process.
COHEN: Other important work happening at Dryden?
SZALAI: I emphasize flight because it’s often overlooked, but the Orion (the new space launch system) work is a very important thing Dryden is doing now, even at the expense of aeronautics activities. It is crucial that we have a national capability for access to space and a replacement for shuttle for getting to low-Earth orbit and beyond. Dryden is managing the Launch Abort System [LAS] for the Ares–Orion system. The LAS will operate in the atmosphere. It involves the integrated effects of rockets, aerodynamics, control systems, and life-support systems. These are things that Dryden has spent a lot of time on over the past decades. If problems occur during the project, Dryden will know a lot about how to make it a success, drawing on its aerospace flight research legacy. There’s nothing more important than getting that done, just as in the sixties there was nothing more important that NASA Dryden did than the Lunar Landing Research Vehicle which trained the astronauts—principally Neil Armstrong—to make safe manual landings on the moon. It played a pivotal role. There was nothing in aeronautics that would have been more important to do.