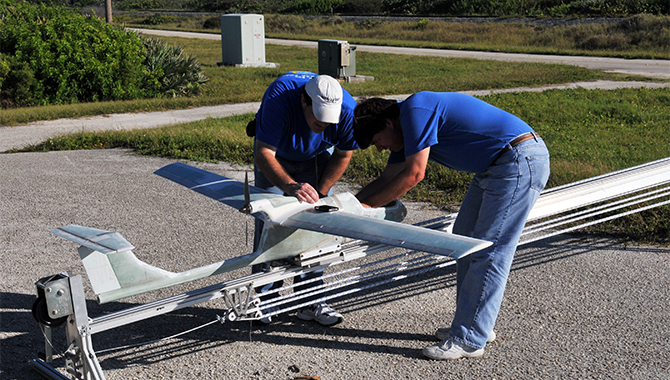
With an aircraft already in production and the groundwork underway for test flights, the Kennedy Space Center Unmanned Aerial System (UAS) team found themselves in a race against time to reach competition day.
Spare time to work on the Rocket U UAS Competition was a rarity for the Kennedy Space Center (KSC) team. Often taking nights and weekends to work on their aircraft, the team came together to get the job done—no matter the task.
The team chose to compete with a fixed-wing aircraft named “Genesis,” already under development in the UAS Laboratory at Kennedy. Having worked on shuttle for numerous years, Mike DuPuis was tapped by the head of Kennedy’s Rocket University to lead the UAS Lab and mentor the competition team.
DuPuis was joined by Stephen McConnell (ground station operator), Dan Keenan (systems engineer), and Martin “Marty” Pontecorvo (the KSC chief UAS pilot) for an interview. Additional team members included Mike Knutson, Les Boatright, Jan Lomness (project manager), Luke Catella, and Rob Mueller.
(Editor’s note: The following are excerpts from a series of interviews conducted with the Kennedy Space Center competition team members and mentor. Some of the content has been edited for clarity and readability.)
APPEL News: What drove the Kennedy team’s decision to use a fixed-wing aircraft for the competition versus other aircraft options?
DuPuis: The UAS Lab was kicked off before the competition was conceived and the Genesis fixed-wing aircraft was already under development in the lab. This was one of the Rocket U platforms for training on project management and systems engineering (PM&SE) and systems engineering and integration (SE&I). The initial meetings of the competition team quickly focused the type of platform and solution that would be implemented or at least investigated. Early on the team felt that because the Genesis aircraft was already under development, it posed less risk for the project. From a risk posture the team thought, we’re already making this effort to certify Genesis for flight here in KSC’s airspace; let’s use that as the competition platform so we’re not trying to get authorization to fly a separate vehicle at the same time.
McConnell: When we sat down to choose an aircraft, we looked through all of the requirements and competition guidelines. Just basing off of the point system for the judging, we thought we could get the most points using a fixed-wing aircraft. We could get the endurance no problem—unless we crashed (which we did)—with a fixed-wing aircraft because we could fly much longer than a helicopter and we could get the observation speed because we could fly faster than a helicopter.
Pontecorvo: And fly higher.
McConnell: Right, and higher so we could do fewer passes. We looked at all the scoring criteria and went with the fixed-wing airframe selection because we thought we could get the most points out of it.
APPEL News: In preparing for the competition, it sounds like your team had a similar experience to the Johnson team in terms of having to lay groundwork to fly unmanned aerial systems at your center.
Pontecorvo: Yes, that’s correct. We did not have a UAS program in place at Kennedy yet. Rocket University gave us the opportunity to learn from other established programs across the agency to build our own program. I tried to mirror the best practices from other NASA centers here at Kennedy. It’s been an outstanding learning experience for me.
NASA’s requirements for a UAS pilot are very similar to a manned pilot. To stay current, I have to do three full-stop landings and touch-and-go landings every 90 days. I also had to design and administer crew resource management classes for all UAS personnel.
The big challenge we had was that the competition was not our primary job. Stephen, myself, and a few others worked numerous nights and Sundays on our plane. The first time we flew it was the day before the competition. Johnson actually had more total flight time on their helicopter than we had on our plane. We had the lowest flight time of the three teams in the competition.
McConnell: We didn’t have flight time problems, we just had time problems.
APPEL News: Despite the time challenges, it sounds like the energy and enthusiasm of the team behind the project was definitely present. Is that a fair assessment?
Keenan: I would say yes, and yes, and yes. In fact we had no charge codes to support this activity. We were permitted to work on the project in the gaps of our daily requirements, as able. I would say that these limitations showed the commitment level of the team members who found the time to make it happen.
APPEL News: Mike, as the team mentor, and in seeing the team fluctuate due to time limitations, what sort of ‘sage advice’ did you have to help keep the project moving forward?
DuPuis: I’m probably no more sage than anyone else on the team. Perhaps having a better understanding of the end goal and how the systems needed to come together, and previous experience of how these systems are developed, verified, validated, maintained, I think I was able to step in and help out where the team might have lost its step.
There were times when the team was focused on learning processes, like different methods of composite manufacturing for the airframe. As time was getting tight, I could sit with the team and say, hey guys, we can spend the next three or four weeks perfecting this other method and we might get a good result, but there are methods that we can implement immediately that can keep us going. From a composite manufacturing perspective, we did a lot of fantastic training and a lot of fantastic hands-on work, but at the end of the day there was a deadline, there was a customer, and there was the need to produce a deliverable. Some of the processes that may have turned out well just weren’t fully mature yet, and so we were able to fall back on some experience we had with faster, simpler methods. There were definitely times when my experience on these types of systems could be brought to bear and just bring a little more focus and clarity to make the technical effort progress a little faster. So that would probably be my biggest contribution.
Keenan: May I add something? We weren’t just building one aircraft, one unmanned aerial system. I believe we were working to lay the foundation for making sure that all of the paperwork and processes were in place so that it is repeatable. There was a lot of relationship building and relationship management. This was not just about building an aircraft and a system. It was about taking areas of competence that we have and learning things that we had never done before.
The great part about the project was when the team came together, got all eyes on it, figured out what we knew, what we needed to learn, and kept moving. Sometimes it’s like making sausage, it’s not pretty, but we stuck together and we made it happen. That’s what good teams do. They make things happen.
APPEL News: What sort of challenges did you encounter leading up to the competition?
McConnell: Two days before the competition I think we had our first test flight and everything was OK, but we didn’t have the video system installed and operating at that point. The next day we installed the video system and that was the first time we had it in the aircraft and flying. The video system wasn’t working and all of a sudden we weren’t getting our GPS telemetry either.
So the day before competition our entire imaging and targeting system was gone. That night we were working on it, looking at it, and we found out that the GPS antenna and the video antenna were too close together. When we moved the GPS antenna back, we might have messed up the link antenna. That’s possibly what caused the crash on competition day.
The morning of the competition we took the airplane out there, got our stations all set up, and powered on the aircraft. We were getting a good GPS link and good video feedback. Everything was going well. Marty launched it, he flew around and we had the targets identified in no time because he only had to make one or two passes.
APPEL News: However, the plane crashed during the competition. Can you tell us more about what happened?
Pontecorvo: That happened on the duration part of the competition. Prior to the competition, our KSC Range Safety wanted our team to have what’s called a flight termination system (FTS). If our aircraft unexpectedly veered off path and we lost the ability to control it, we had to make sure that we could prevent it from going some place it wasn’t supposed to go. We needed to make the case that our Genesis airplane, which can fly straight and level for hours, wouldn’t go to Titusville if we lost the radio control link.
During the competition the aircraft did lose radio link—and our FTS worked. The plane did exactly what we promised to our KSC Range Safety and to the Airworthiness and Flight Safety Review Board, which was created in part for the Rocket U program. When we lost the link, the plane immediately cut the power, banked hard, and spiraled into the ground. Our Range Safety representative came over, put his arm around me and said, Marty, I trust you now. Thank you.
In a way, the crash did a lot of good in demonstrating the reliability of our FTS, but not so much for our chances in the competition.
APPEL News: Despite the challenges, it sounds like the team really came together as the competition approached.
Keenan: I can speak to that. While I was pulled away from the team for a while, I was able to come back and support as the competition was getting closer. What I got to see—and be a part of—was a team in that “magic hour” of a project where everyone comes together to get things done during crunch time. No one locked themselves into a specific role – they just did what needed to be done, be it sweep floors, fabricate, or whatever. There was a small group of people who worked weekends and late nights and just made it happen. The camaraderie, the focus was really sharp, and a lot of fun. We all just did what we could do.
DuPuis: Dan is absolutely right. At crunch time there was a core group of people—and I’m not taking anything away from anyone who wasn’t able to make increased time commitments—but there was a group of people that was able come back together after the project became protracted and after support had fluctuated due to people getting pulled into other commitments (i.e., their day jobs at NASA). There were times when things would slow down, there were times when it didn’t seem like a lot of progress was being made because the team had to wait on various things such as the machining of the mold sets.
So there were times when morale was an issue; where the schedule started to slip, regardless of the reason. As we closed in on competition time, the team did have to come together and do a gut check. We’re not going to show up at the competition without a flight vehicle. At that moment, you definitely saw some people step up and grab the reigns and say I’m not sure where the best place is for me to plug in, but I’m here to help, so plug me in somewhere. It was a great experience.
APPEL News: What observations did you make about the other teams in the competition?
DuPuis: The day before the competition flights, at the testing area north of Launch Pad B, we got to see each team’s solution, have unfettered access to the other team’s flights, and talk to other team members. That was very interesting. There was a lot of technical camaraderie. I don’t think anyone was concerned about having their ideas stolen. (And if you need to take someone’s ideas and implement them the day before the competition, then you are in serious trouble anyway.) I don’t think anyone was worried about information sharing
It was great to see that each team had a different solution and it appeared as though everyone approached their solution from the same standpoint: project risk. Johnson’s solution was a rotorcraft. I know their mentor has an incredible amount of experience with rotorcraft and the younger team members had done some experimentation with rotorcraft. Their core team had a technical understanding of that hardware and they could focus on other areas of the competition. I think Marshall was the same way. I think they had people with multi-rotor experience just as we had people who had fixed-wing experience coming out of the initial standup of the UAS Laboratory and the development of Genesis.
It was great to see everyone’s implementation of technology and it was very easy to see the teams that had a lot of support and were able to commit. For example, Marshall had really good management support and organizational backing. They were able to commit a reasonable portion of their time to implementing their solution and it showed. Whereas for Kennedy and Johnson, it was less so, resulting in a bigger push at the end to get their systems where they needed to be for the competition.
APPEL News: What are some of the lessons learned from this competition experience?
DuPuis: I think a huge lesson learned (or lesson reinforced because we probably knew this already) for me and for the administration of Rocket University at KSC going forward is we need to do a better job of showing our management how participation in Rocket University, these competition teams, and APPEL courses directly benefits NASA employees by increasing their skills and effectiveness.
Keenan: Exactly—as well as our ability to know who can solve what problem. An untapped resource might as well be a resource we don’t have.
Pontecorvo: This experience has really broadened my view of UAS technology applications. Because of the competition, I’ve become involved with a number of organizations, including the Association of Unmanned Vehicle Systems International (AUVSI) working with Space Florida. I am part of their working group and it’s been a tremendous opportunity for me. There’s real interest in applying UAS capability to a number of areas. AUVSI is interested in using UASs with mutli-spectrum sensors for agricultural work; to look at crops to know when to rotate areas, inspect for disease, check on ripening, etc. Beyond that, there are also the obvious search and rescue applications and all kinds of weather applications, security-related work, and building inspections after significant weather events. It’s just amazing to see the connections I’ve made and to get involved in the larger UAS community.
McConnell: I learned a lot. I had never worked with composites before and then we went and built a composite aircraft. I also learned a lot about KSC and NASA processes for how to do procurements, government practices, and how to work with foreign companies. (We bought a payload system from Canada. Procurement from Canada is totally different from procuring something from a company in California.) I learned a lot of those processes, which directly helped my job. Currently, I’m working on a payload design and when I need to procure something for this project, I already have the knowledge and understanding of the processes. I have also acquired a lot more of technical knowledge that may come in handy in the future.
Read an interview with Marshall Space Flight Center’s competition team.
Read an interview with Johnson Space Flight Center’s competition team.
Learn more about Rocket University.
Click to view full photo gallery on Flickr.
Les Boatright (left) and Mike Knutson (right) prepare Kennedy Space Center’s Genesis aircraft for launch.
Featured Photo Credit: NASA / Kennedy Space Center