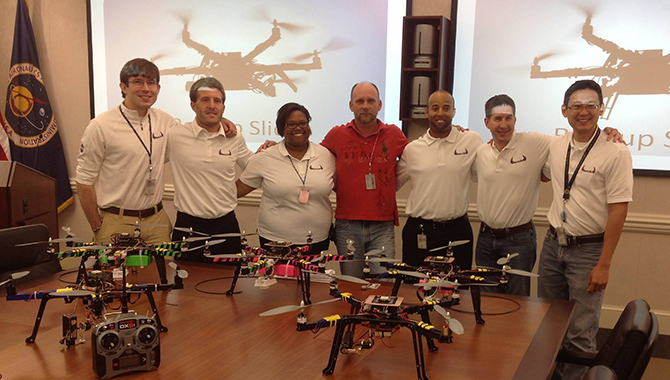
Team Aero-M with their competition hexacopter (pink), two additional hexacopters, and two quadcopters after the UAS Competition. From left to right: Adam Kimberlin, Chris Becker, Tiffany Russell, Jim Snoddy (mentor), Robert Parker, Garrick Merrill, and Peter Ma.
Photo Credit: NASA
A year ago, six early-career engineers from Marshall Space Flight Center experienced success with their unmanned aerial vehicles. They haven’t stopped flying since.
Marshall Space Flight Center’s (MSFC) Team Aero-M participated in the 2012-2013 NASA Unmanned Aerial Systems (UAS) Inaugural Competition, which was hosted by Kennedy Space Center (KSC) and NASA’s Academy of Program/Project & Engineering Leadership (APPEL) as part of KSC’s Rocket University program. Team Aero-M placed first. But when the competition ended, the group didn’t stop flying; instead, they obtained funds to expand their work on unmanned aerial vehicles (UAVs) and were later honored with a MSFC Group Achievement Award. APPEL News recently caught up with five of the original Team Aero-M members—Christopher Becker, Peter Ma, Garrick Merrill, Robert Parker, and Tiffany Russell—to learn more about how their UAV work is benefitting their center.
APPEL News: The UAS Competition ended a year ago. So why are you still flying UAVs?
Garrick Merrill: Before we even went to the competition, we applied for a TIP, which is a Technology Investment Program. It’s a center-level fund. One of the ideas we had for the competition—but we ran out of time and couldn’t do it—was to have multiple UAVs cover a search area instead of just one. [Our TIP proposal] focused on researching formation flying using multiple UAVs. We would then apply our research to a satellite situation where you have multiple satellites in a formation. With the UAVs, we can work out formations and actually test them on vehicles. It gives us the opportunity to do real flights instead of just a flight simulation on a computer.
We applied for the TIP just before we left for the competition. When we got back, we found out it had been awarded to us. We only have funding for two or three of us to spend more time on it but we all still stay plugged into it together, and for test flights we always have different people from the team helping. So that’s what we’ve been working on for the past year.
APPEL News: What will you do now that your TIP funding is coming to an end?
Merrill: We’re applying for a follow-on TIP to continue the formation work with our quad copters. We’re also applying for a CIF, which is a Center Innovation Fund. With the CIF, we’re proposing to use our biggest vehicle, an octocopter, as a sensor platform. We’ve been flying the octocopter and testing it already, and we have a LiDAR (Light Detection and Ranging) sensor to use with it. Our goal is to fly over our lunar training field here at Marshall and get data from that field. The field has very close optical properties to those of the moon, so we can get good representative data.
At this point, we’re still going through the proposal process for the CIF and we haven’t heard back on the TIP yet. So in terms of the future—who knows? We may continue one or both of our projects, depending on the funding we get. Even if we don’t get funding, we probably would continue to fly on an as-needed basis. For instance, if somebody needed a video of something or had a sensor and wanted to do a flight, we would do it as long as we still had workable vehicles. We definitely enjoy flying in addition to doing the research.
APPEL News: You’re using the UAVs for formation flying and sensor applications. Are they being used for anything else?
Christopher Becker: Yes. We got approached by the Mighty Eagle [flight team] in April of 2013. They had heard about the UAS competition and knew we had these unmanned vehicles. They wanted a different perspective on their flight, an aerial shot. So we took an off-the-shelf GoPro, hard-strapped it on our vehicle, and flew out to the location. Mighty Eagle did their test flight, we got the video. They were happy with the results. Later in the year they had a longer test flight series, so we ended up getting a gimbal [stabilizer]. That produces a nice smooth video. With the first video, every time the UAV would hitch or roll, you’d see the camera roll. The stabilizer allows you to get a nice smooth video with much higher quality. We flew for five or six of their flights later in the year. It gave them another piece of data they could use to analyze their flights.
This year we were approached by some of the facilities folks here at Marshall about using that same platform to get shots of new buildings going up, or sinkholes, or anything on the center that they wanted to shoot from above. Previously they’d have to get a crane or hire a helicopter, which is obviously a lot more expensive.
APPEL News: It sounds as though the work you’re doing with the UAVs has really benefitted Marshall. Can you tell us more about that?
Becker: In general, the UAVs are used to view or test things that would be really expensive to do the conventional way. For example, if you want to see something on a satellite system, you usually just simulate it on computers. But that isn’t the same as doing it with actual vehicles. That’s why we use the UAVs. It’s a similar concept [to satellite flying]. It’s obviously not the same—it’s a different environment—but for the formation flying, the UAVs give you a set of vehicles cooperating with one another relatively cheaply. So [our UAV] platform is used if you need something done less expensively or more frequently, like for people to do tests of sensors or some new algorithm they developed for flight control.
APPEL News: How else has your UAV work supported your center?
Tiffany Russell: We were able not only to do the competition but continue our work on the UAVs because people have seen that this technology can be used in so many different areas. Our work on it is a benefit to our home organizations: through this experience, we’re learned more about how Marshall works and how the agency works when it comes to flight programs, and have been able to take that knowledge back to our home branches. We’ve been able to take this project and grow it into a robotic laboratory that we’re sitting in right now. It’s open not only to our team, but to others that have similar types of work but haven’t been able to find a venue on center to get it done. They can come here and do it.
APPEL News: So you ended up creating a robotic laboratory that’s now a resource for everyone at Marshall?
Merrill: When we were doing the competition, we had a lab set up because we had to have a place outside of our offices where we could keep the vehicles and work on them. Then, after the competition, our work didn’t end. We had the TIP, plus we ended the competition with hardware that was still usable. We built more than one UAV because we saw throughout testing that they can fail. And we didn’t want to have a crash the day before the competition and not be able to participate. So we ended up with three or four vehicles that were usable. That meant we still needed a lab somewhere. We’ve now pulled in rovers as well as aerial vehicles. Our goal with the lab is to have it be a resource and not just exist for a specific purpose. The research ideas we come up with are not going to pan out every year. Why not have the vehicles available for the next person who walks in the door once our work is done?
APPEL News: How did you evolve from a hexacopter to a quad copter to an octocopter? Are they used for different purposes?
Robert Parker: Actually, we started off with the quad copter. We changed over to the hexacopter to improve the battery life and lifting capabilities. We ended up with the hexacopters for the UAS competition.
Becker: As you add more propellers, you have a trade off: get more flight time or carry a heavier object. As with anything, the bigger it gets, the more capability you usually get, one way or another. The LiDAR, for example, is two kilograms. That’s stretching the capability of our hexacopters, which is why we went to the octocopter.
Merrill: One thing to add is that these vehicles are kind of flying lawnmowers. So we have multiple vehicle types now partly in the interest of safety. We’ve got quad copters, which we use for the formation flights. We’ve got hexacopters that were left over from the competition and can lift more than the quad copters. And we’ve got the one octocopter. We try to match up the payload to the vehicle. If we have a lighter payload, we’ll put it on a quad copter because it’s a lot less risky: there’s a lot less mass moving around in the air. Also, we have a lot more of them. If we have something heavy [to fly], we might end up with the bigger vehicle. We didn’t have the octocopter until recently because we didn’t have a need to lift that much payload. It was only when we came up with the research idea to work with the LiDAR and other larger sensors that we needed a larger vehicle.
APPEL News: Two of you are funded for the continuing work on the UVAs. How do you balance that work with your “day jobs” at the center?
Merrill: Over the past year, the TIP has afforded both Chris and me the opportunity to work part time on the UAVs in addition to our NASA “day jobs.” It’s nice to have variety and to work on multiple things.
Becker: My branch chief is very supportive of people doing these smaller projects in general—not just the UAV activities. It always helps if you have an actual project to charge to. When we do, like the current TIP project, she’s very open to letting us work more than we’re actually charging to that project as long as we get our other responsibilities done. It depends on your management, but I’ve seen a lot of management that is supportive of these smaller projects because they know that our day job, working the Space Launch System (SLS), is a little bit more abstract.
APPEL News: Although there’s only funding for two of you, has the entire “Team Aero-M” from the competition remained involved?
Peter Ma: Since the competition I’ve been involved, but not as much as Garrick and Chris. I’m usually just working on the 80/20 principle, where you work 80% of your time on your day job and 20% on relevant activities on the center that may or may not be part of your specific job responsibilities. I’ve used the “20%” as a rationale to keep working on the UAS stuff since the competition.
Russell: In my office, the original competition work was highly encouraged: “If you get to go outside, and touch hardware, and fly—go!” But I used up all my dimes [on the UAS competition last year] and was pulled off onto another project. Still, whenever I have a chance to come over and help or do anything UAV-related, I never get any resistance as long as my primary work is done first.
APPEL News: Are you doing the same kind of work in your “day jobs” at Marshall as you do with the UAVs? Or do you get to do something entirely different?
Russell: My day job is more about conceptual design. We do a lot of big picture work, seeing where NASA’s going to be in a few years. So [the UAV project] is one of the rare opportunities I get to be next to hardware, touch it, work with it. When the competition project started, it was around the time that shuttle and the Constellation Program were ending, so being able to work with hardware outside of the International Space Station (ISS) was pretty much non-existent around the center.
Parker: I work with the SLS software. But we won’t see our work on the actual vehicle until the first test flight in 2017. The UAV project is different: within a few weeks we’d actually see what we were working on flying. And in the competition, at the end of the year, we were able to see that we put something together and it worked successfully. As far as our day-to-day jobs, it takes a lot longer to see the results of our hard work.
APPEL News: Have you stuck with the defined team roles you had for the competition?
Becker: To a certain extent, Garrick and I have followed the same roles we had before. But not entirely. Garrick’s background is more the hardware parts of it: he’s an electrical engineer. So if we have some wiring to do, we just naturally go to Garrick to do it. I’m one of the primary ground control operators, so when we have our flight tests I take over that capability. But there are a lot of us who can do that. Peter, Robert, pretty much everybody. A lot of it is just who’s there on a particular day. We concentrate on the skills we were doing for the competition, but these things are pretty simple to work on so we can be flexible about who’s doing what.
Merrill: It’s easier to fall back into the things we were doing. At the same time, none of us feels hesitant about jumping in and taking care of something if we’re the only ones there because even as far back as the competition we were cross training. We wanted to make sure that if a person was sick and stuck in the bathroom on the day of the competition, somebody else could take over. So we’ve always tried to keep everybody in the loop on stuff as much as possible.
APPEL News: Has anything surprised you about the work you’ve done with the UAVs?
Merrill: The biggest surprise, even during the competition, was [the degree to which] UAVs are in their infancy from a regulations standpoint both at the NASA level and the FAA level. If you had to point back to one thing that probably gave us a big advantage [in the competition], it was that we really pushed hard on getting approvals and navigating the fairly complex process of being able to fly a lawnmower. We had to convince people that it wasn’t an airliner with people on it: you could take more risks with a UAV. We had to convince boards that weren’t even at our center—because Marshall isn’t a flight center—to allow us to submit paperwork to fly multiple times instead of having to [submit paperwork] every time we flew. There were a lot of requirements we had to address in order to accomplish our mission for the competition.
APPEL News: What kinds of challenges did you face in preparing to fly?
Ma: One of my primary roles in the competition was to help the team get through all the processes and paperwork. When we went into the competition, we had no inkling about the requirements and the certification that we had to do for the competition. The technical work was challenging enough. No one realized the full force of the flight regulations that were placed on UAVs as well. As Garrick mentioned, we don’t have a flight ops directorate within our center to approve test flights. So, through a proxy, we had to use Langley’s flight ops directorate and their board approval to certify us to fly. It took months of legwork before the competition to get certification. We had to do things like get FAA medical clearance that says we’re physically capable of piloting these vehicles remotely. And we had to have our eyesight checked, make sure it’s 20/20 or 20/40, depending on our role. Things like that. We also had to make sure we were compliant with two NASA procedural requirements (NPRs): NPR 7900.3C, Aircraft Operations Management Manual and NPR 8715.5A, Range Flight Safety Program. That was the big bulk of the work we had to do: [make sure we were compliant with] those two flight-related NPRs before we even powered up our vehicles. We had no inkling that we had to do all of that prior to starting the competition.
APPEL News: Tell us what you’ve enjoyed about your work with the UAVs.
Ma: What I found most gratifying about the project was that, from the get-go, we were able to find a few fellow team members who were dedicated to “the cause.” That was very necessary to be successful in the competition. We started off with 20-25 interested members, but like all of us they had day jobs, and there was a requirement that if you spent time on the project you didn’t get a charge code: it was all volunteer, part of the 80/20 rationale. As long as you’re able to maintain your day job, you can spend your remaining time on this project. Well, not many people could do that. But the few remaining people we had were able to see it through from beginning to end. It was that kind of dedication that made us a success. That was not the case for the other two teams, the other two centers that participated in the competition. They didn’t have the minimum skeleton crew to maintain the project to completion. But we did.
Russell: One surprising thing was how our work is [being looked at by the center]. At the end of the UAV project last year, I started working on a solar sail project that ended up turning into a small satellite project. Now there are two of them, they’re twin satellite projects that are going to fly in the next few years. At the beginning, when we were starting to put things together, one of the systems engineers on the team said to me, “Hey, you did the UAV project, you know how to navigate all of these NASA [processes].” That’s the perception. Right now, the agency is in a birthing phase of figuring out how to manage what they call “class D” missions, which are small satellites, like CubeSats, of various configurations and sizes. And they’re actually looking at the model of what we did [to fly the UAVs] and applying it to smaller Transformation Satellite Communications System (TSAT) missions that they’re hoping to fly in the next couple of years. So the fact that something that we worked on just a year ago is able to help other projects in the early stages of their formation is pretty amazing.
Parker: One thing I really enjoyed about the project was that the main focus was to learn the NASA systems engineering handbook. And that particular handbook relates directly to my job. I work on the SLS flight software systems verification team. The experience on this project gave me a lot of insight into things I’m not directly involved in day to day.
APPEL News: Is there anything you’d like to add?
Ma: The premise of the whole competition was to give us a real-life experience of bringing something from cradle to grave from a project management (PM) perspective and as part of the Systems Engineering & Integration (SE&I) process. I think what greatly attributed to our eventual success in the competition was that we were fairly rigid in applying both PM and SE&I processes, scaling and scoping them to our particular project. We gained a lot of insight into how those processes work, and how it works to see a project to fruition.
Merrill: We all loved the opportunity to do the competition. It was a once-in-a-career experience. I hope that anybody coming into NASA can have that same opportunity.
Read more about Team Aero-M in the UAS Competition.
Learn more about the 2012-2013 NASA UAS Inaugural Competition.
Click to see the full Flickr set.