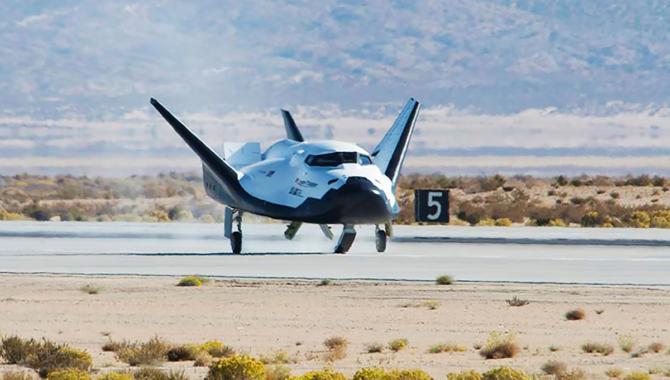
The Dream Chaser spacecraft glides to a landing at NASA’s Armstrong Flight Research Center at Edwards Air Force Base in California, following a successful free flight demonstration in 2017. Photo Credit: NASA
Dream Chaser, with roots in a NASA project from the 1990s, will take lifting body design to new heights.
Inside the Space Systems Processing Facility (SSPF) at NASA’s Kennedy Space Center in Florida, teams are making progress preparing a new spacecraft—the Dream Chaser spaceplane—for final assembly, testing, and pre-launch processing before its first flight to the International Space Station (ISS), likely now in 2025. Developed by Sierra Space with a foundation in NASA history, it will fly as part of NASA’s Commercial Resupply Services program.
The Dream Chaser is a “lifting body” spaceplane, which generates significant lift through its body shape and nose cone design, and employs small, retractable wings. This enables it to return from space with less g-forces and touchdown gently on a landing strip.
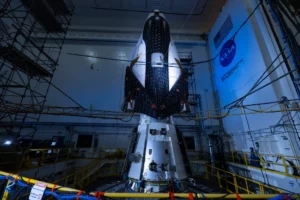
Dream Chaser and its cargo module undergoing testing at NASA’s Neil Armstrong Test Facility to prepare for the extreme environment of space.
Photo Credit: NASA/Jef Janis
Its first flight will launch to the ISS from Cape Canaveral Space Force Station atop a United Launch Alliance Vulcan Centaur rocket. It will be paired with the company’s Shooting Star cargo module. This module attaches to the back of Dream Chaser and features thrusters for operations in space, large, folding solar arrays for power generation, and an internal cargo capacity of 7,000 pounds. Shooting Star will be jettisoned during reentry, burning up in Earth’s atmosphere.
The spacecraft arrived at KSC in May, following months of testing at The Space Environments Complex at NASA’s Neil Armstrong Test Facility, a remote campus of NASA’s Glenn Research Center in Ohio. It was tested in a variety of facilities there, including the Mechanical Vibration Facility. Over five weeks, the spacecraft were stacked on a powerful shaker table to simulate the vibrations of a launch aboard a Vulcan Centaur rocket.
It was also tested in the massive Space Simulation Vacuum Chamber, a 122 ft high, 100 ft diameter test area that effectively simulates the vacuum of space and can expose a spacecraft to the dramatic temperature fluctuations in low-Earth orbit—a 400-degree range from about -150 to 250 degrees Fahrenheit.
“Successful completion of an incredibly rigorous environmental testing campaign in close partnership with NASA is a significant milestone and puts Dream Chaser on track for operations later this year,” said Sierra Space CEO, Tom Vice, in a company press release.
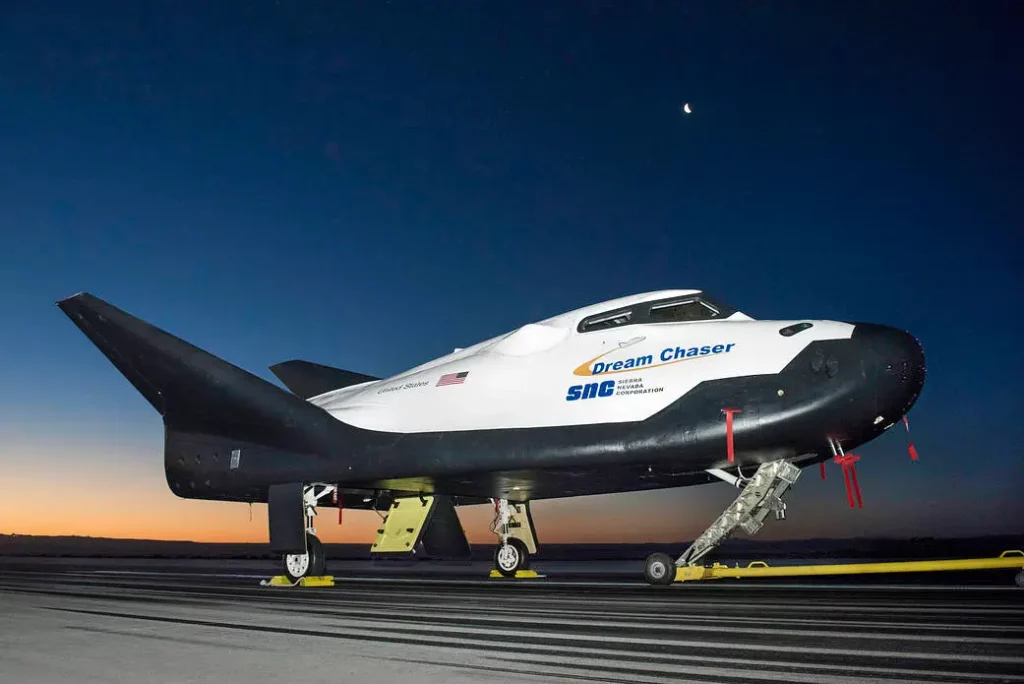
Sierra Nevada Corporation’s (SNC) Dream Chaser® spacecraft shown on the runway at NASA’s Armstrong Flight Research Center on May 20, 2017, preparing for a tow-test. Photo Credit: NASA/Ken Ulbrich
Dream Chaser is a striking spacecraft, just 30 feet long and 15 feet wide. Covered in 2,000 white and black thermal protection system tiles, it bears a passing resemblance—though considerably smaller—to NASA’s space shuttle, the workhorse of low-Earth orbit that was instrumental in assembling the ISS then regularly delivering crew and supplies.
But Dream Chaser’s roots most clearly trace back to work at NASA’s Langley Research Center in Hampton, Virginia in the early 1990s, where a team of researchers developed designs for an experimental spacecraft known as the HL-20. It was envisioned as a low-cost alternative to the shuttle for transporting crew to the ISS, with one permanently docked there as a ready return vehicle in the event of a mechanical or medical emergency.
The HL-20 was never built, but NASA worked with contractors on in-depth studies and assessments of the design, and the feasibility of developing a prototype and operational system. A full-scale model of the spaceplane was built in 1990 for human factors research.

The wingless, lifting body aircraft sitting on Rogers Dry Lake at what is now NASA’s Armstrong Flight Research Center. From left to right are the X-24A, M2-F3 and the HL-10. The lifting body aircraft studied the feasibility of maneuvering and landing an aerodynamic craft designed for reentry from space. Photo Credit: NASA
The HL-20 built upon earlier research NASA conducted on “lifting body” aircraft. Between 1963 and 1975, NASA developed and built a series of thick, angled aircraft with small fins instead of wings. Engineers discovered in the 1950s that these design characteristics, coupled with a thick nose cone, would produce enough lift to enable a spacecraft to make a controlled entry through Earth’s atmosphere and land like a plane. The aircraft informed the design of the space shuttle.
NASA signed a licensing agreement in 2006, to allow a company known as SpaceDev to further develop the HL-20 concept into a commercial spacecraft. Sierra Space, then the Sierra Nevada Corporation, acquired SpaceDev in 2008 and continued developing Dream Chaser.
Inside the SSPF at KSC, work is underway and will continue this fall. The final assembly and system checks include closeout work on the propulsion system, leak testing, and installing the final thermal protection system tiles, which will protect the spaceplane from temperatures approaching 3,000 degrees Fahrenheit during reentry. Owing to technological advances, the tiles are larger, stronger and lighter than the 24,000 6-by-6-inch tiles used during the shuttle era.
Testing still ahead includes checks for electromagnetic interference and electromagnetic compatibility, simulations of the harsh acoustic atmosphere of launch, and runway tests of the braking system Dream Chaser will use when it returns to KSC from the ISS.
“The SSPF High Bay, a site rich with historical significance, hosted the foundations of the International Space Station and multiple payloads which travelled to space and subsequently helped unearth key discoveries and scientific breakthroughs which changed life on Earth,” Vice said, in a company press release. “Our work at this facility is a testament to the collaborative spirit of the space community, with systems bound for the space station—and even lunar-bound Artemis hardware—sharing the same space.”