Collaborative Problem-Solving: The STS-119 Flow Control Valve Issue
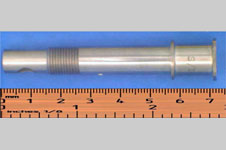
GH2 flow control valve and poppet. Each valve has a poppet that resembles a tiny sprinkler head, which pops up and down regulating the flow of gas through the valve. The valves have two rates: high and low. During a launch they switch between the two rates approximately fifteen times. Image Credit: NASA
On November 14, 2008, as Space Shuttle Endeavor rocketed skyward on STS-129, flight controllers monitoring data during the ascent noted an unexpected hydrogen flow increase from one of the shuttle’s main engines. Despite this in-flight anomaly, the launch proceeded smoothlysince three flow control valves (one per main engine) work in concert to maintain proper pressure in the hydrogen tank, one of the other valves reduced flow to compensate for the greater flow from the valve that malfunctioned. This issue would require immediate attention as soon as STS-126 landed safely on November 30.
The next launch, STS-119, was scheduled for February 12, 2009. Shuttle and ISS program managers preferred for the mission to launch prior to mid March so that it would not interfere with the March 26 mission of the Russian Soyuz. If the launch were delayed until after the Soyuz flight, interdependencies in the schedule would require a re-evaluation of other future launches.
The challenge this problem would pose was a familiar one. To ensure the safety of future shuttle missions, management, along with the technical community, would need the best possible analysis to understand what happened on STS-126 and its implications for future missions. Leaders would have to promote and ensure open communication among the multiple organizations involved in the shuttle program so that all relevant information would be available to decision makers with the responsibility to approve or delay future shuttle flights.