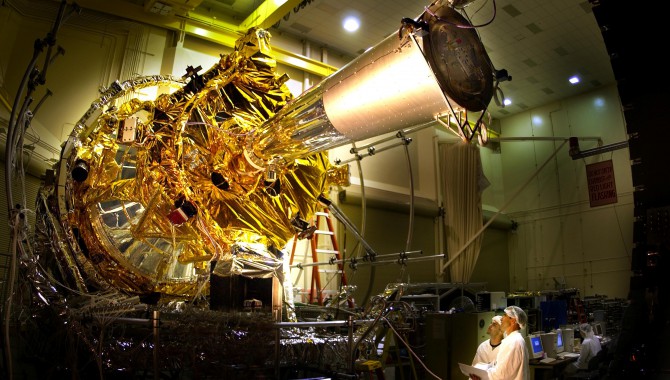
By Edward S. Calder and Bradley T. Jones
Gravity Probe B (GP-B) has been called the most sophisticated object ever placed in space. Whether this is true or not, it is certainly oneof NASA’s most complex missions and occupies a unique place in space science history. GP-B embodies all aspects of an ideal NASA mission: advancing science (testing Einstein’s general theory of relativity), meeting daunting technological challenges (gyroscopes that required an environment with no drag and near absolute zero temperatures), teamwork (Stanford University–NASA–Lockheed Martin), and public value (more than ninety Ph.D.s were earned on GP-B-related projects). While the scientific value and technological achievements have been well documented, relatively little attention has been given to the management of this extraordinarily complex mission. How was its management structured? How was the balance between radical innovation and reliability achieved? What practices can be extracted from the GP-B program that might be applied to other missions?
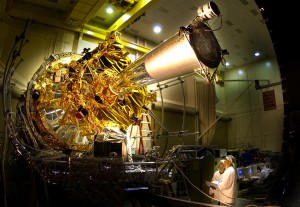
The completed space vehicle undergoing thermal vacuum environment testing.
Photo Credit: Lockheed Martin Corporation/Russ Underwood
Management Story
GP-B began like many other NASA–university collaborations: a group of scientists conceive an important scientific experiment that requires a space environment. In the case of GP-B, the idea emerged from a 1959 discussion at Stanford between Professors Leonard Schiff and William Fairbank of the physics department and Professor Robert Cannon of the aero/astro department. The experiment they envisioned would measure the relativistic precession of an orbiting gyroscope (that is, the motion of its axis), thereby testing two aspects of the general theory of relativity: the warping of space-time caused by the Earth’s mass (geodetic effect) and by the Earth’s rotation (frame-dragging). In 1964, NASA decided to fund a small group of Stanford researchers to develop the basic science requirements and technology. Stanford and Marshall Space Flight Center collaborated on some technologies, including oversight assistance on subcontracts to industry for gyroscope and telescope hardware, development of the insulating container or dewar, and testing of many basic features of the final design.
In 1985 GP-B entered a new phase that became known as the management experiment when then-NASA Administrator James Beggs commented that GP-B was to be an interesting management experiment in addition to an interesting scientific experiment. The management experiment was an agreement between NASA Headquarters, Marshall, and Stanford University that made Stanford the prime contractor, responsible for managing the entire program with minimal NASA oversight. The decision followed a recommendation from the Space Studies Board to NASA HQ in mid-1983 that in a mission such as GP-B, where the science instrument (payload) and spacecraft are much more closely integrated than in typical space programs, separating the two would be gravely detrimental. The agreement was predicated on Stanford’s intent to set up a much stronger management structure than is typical at universities.
In the following years, Stanford made substantial progress on the novel technologies needed to achieve the precision required for GP-B’s demanding objectives. In order to measure geodetic and frame-dragging effects, extremely small angle changes (forty-two milli-arc seconds) needed to be detected and measured. (One milli-arc second is equal to the width of one human hair as seen from ten miles away.) This precision placed extremely tight tolerances on much of the GP-B hardware. The gyroscopes, for instance, are the most perfectly spherical objects known to mankind.
To assist Stanford with development, Lockheed Martin was awarded the subcontract for the spacecraft and some components of the payload. This contract was under Stanford’s control and represented a substantial increase in the university’s managerial responsibilities. During this phase, GP-B also began a process of incremental prototyping — that is, developing an initial system design and then building actual hardware, while recognizing that a process of redesign and rebuilding would be necessary. The advantage to this approach lies in the learning derived from building hardware, both in terms of process and concept evolution. Given the complex and radical innovation necessary for GP-B’s technology, incremental prototyping contributed crucially to the ultimate success of the program.
Around 1998, the management experiment was terminated when the GP-B team encountered two significant technical problems involving the payload system: one necessitated the removal and replacement of one of the four gyroscopes and the other repairing a broken thermal contact between the probe and dewar. While the GP-B team resolved both issues skillfully, the associated delays to schedule and cost contributed to a growing feeling among NASA personnel that the Stanford team had entered a stage of development for which it didn’t have sufficient experience. This view was made explicit by an independent review team that went so far as to recommend that Lockheed Martin be made the prime contractor. NASA concluded that Stanford would remain the prime to preserve the scientific integrity and coherence of the mission, but additional NASA personnel would be needed to help run the program. NASA took a much more proactive approach to GP-B, involving many NASA employees at various levels of decision making and oversight. Gravity Probe B increasingly resembled a typical NASA program.
Management Lessons Learned
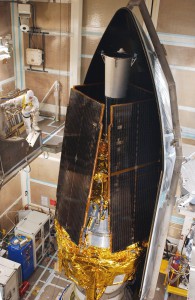
The space vehicle during the encapsulation process atop the Delta II launch vehicle.
Photo Credit: Lockheed Martin Corporation/Russ Underwood
Was the management experiment a success, or does the fact that NASA intervened at the end indicate that a university is not capable of being the prime contractor? The remarkable progress made while the program was under Stanford’s direction shows the value of making a university the prime contractor. At the same time, the fact that NASA needed to step in and mitigate a perceived growing risk indicates that some improvements are necessary for this type of collaboration to work.
Universities and government/industry operate in vastly different environments and have distinct capabilities and cultures to address their different challenges. Universities are flat organizations with little in the way of standardized processes (at the project level); they excel at radical innovation. The government and private industry mainly comprise hierarchical organizations with strong institutionalized processes that excel at incremental innovation. University projects generally involve small teams and therefore have little need for collaboration management. Government/industry projects are usually large collaborations that require rigorous boundary and collaboration management. These differences have significant implications for collaborative projects such as GP-B. In order for collaborative research to become valuable and successful, the program leadership must strategically leveragethese differences in capability while managingthe differences in culture.
Managing organizational differences is one of NASA’s most important responsibilities in collaborating with universities. It can be done by recognizing and managing contextual transitions and establishing an appropriate risk management system. A contextual transition is a change in the requirements, processes, and even the nature of the program. These transformations are not clear and sudden. They can last months or years, making them difficult for NASA or the university to recognize. While the standard NASA five-phase classification scheme is a comprehensive and convenient way to look at program evolution, a more fundamental change for NASA–university collaborations is the beginning of flight hardware development. Moving from research and prototyping to building flight hardware is a shift that requires traditional aerospace processes like quality assurance, operations procedures, and configuration management. These processes, which ensure reliability and reduce programmatic risk, generally impair creative research and development, which thrives in an environment with fewer constraints and more freedom to quickly try new ideas. NASA can help universities recognize the point at which they should begin incorporating
aerospace processes and aerospace-experienced managers in their teams. It must be done early enough to give university researchers competence in such practices when appropriate, but not so early that NASA hinders the innovation gained by working with universities. Gradual implementation achieves the best results.
In addition to recognizing when this transition should take place, NASA should help implement these aerospace processes. The GP-B program showed that universities are indeed capable of adopting aerospace processes; by the end of the program, GP-B produced a number of researchers who were highly skilled at building flight hardware, in addition to being technically creative. NASA has a clear role in ensuring that universities provide the training and experience their young researchers need to mature into able aerospace researchers. Clear guidelines and one-off training sessions can help, but important tacit knowledge is more effectively transferred by embedding experienced NASA or industry personnel in university teams. For instance, one individual who originally came to Stanford as an undergraduate and remained to pursue a graduate degree had no aerospace program experience prior to GP-B. The project gave him an opportunity to apply his deep classroom knowledge to flight hardware design and development processes. Working with his Lockheed Martin colleagues, he developed an expert knowledge of the requirements and skills necessary to design and build flight hardware. Eventually he completed his Ph.D. at Stanford and became the team lead for one of the most critical components of the space vehicle. He has proved an extremely able program manager.
Another component of managing the gradual transition from research to flight hardware development is ensuring the university’s management team has the relevant skills and experience for each stage. For a long time, Stanford had a program manager who possessed a strong technical background and aerospace management experience. After his departure, Stanford promoted a number of its senior scientists to program manager; they were technically excellent but didn’t have the experience necessary to manage a full-scale aerospace program or the practical knowledge of how to develop a flightworthy spacecraft. Eventually a program management team was put in place that possessed the appropriate experience — depth in aerospace management and a sufficient understanding of the science — which allowed the program to run smoothly up through launch and mission operations. In this kind of case, NASA can help the university recognize the need for a shift in its management team’s competencies and identify appropriate external candidates or ensure the university is cultivating appropriate personnel internally.
NASA should also take an active role in instituting a risk management system and helping mitigate risks that stem from university inexperience in flight programs. Initially, GP-B suffered from an inadequate system for assessing and alleviating risk. NASA oversight was often misplaced, focusing too much effort on non-issues and not enough on the more serious problems. For example, while moving the payload from Stanford to Lockheed Martin, the wrong type of gas was connected to the dewar. The reason for the mishap became obvious after the fact: different gasses were stored in the same color bottle. NASA brought in a large team to analyze the failure and provide corrective action, but this added little value; the Stanford team understood the mistake and easily provided corrective measures. It would have been much more valuable to seek out similar process problems instead of dwelling on ones for which the solution was evident. NASA’s motivation was correct, but an ineffective risk system makes it difficult to properly judge perceived risks and increases the danger of overreacting to minor risks and underreacting to major risks. Before a more structured risk system was put in place, Stanford’s fear of NASA overreaction to such problems limited communication. Much of the university team’s time was spent providing status briefings to NASA rather than solving the issue at hand. After helping establish a new risk management system that scaled the reaction to the risk, Marshall was able to provide appropriate and more effective oversight and improved the character of the collaboration dramatically. With the tension of uncertainty and inappropriate responses removed, a sense of partnership and respect increased and contributed to improved program performance.
The goal of any true experiment is to learn something. GP-B proved to be not only a great science experiment but a great management experiment. The successful launch and on-orbit operation of Gravity Probe B is a testament to the value of working with universities. The management lessons that emerged put NASA in a better position to take advantage of this potent resource for challenging future missions.
About the Author