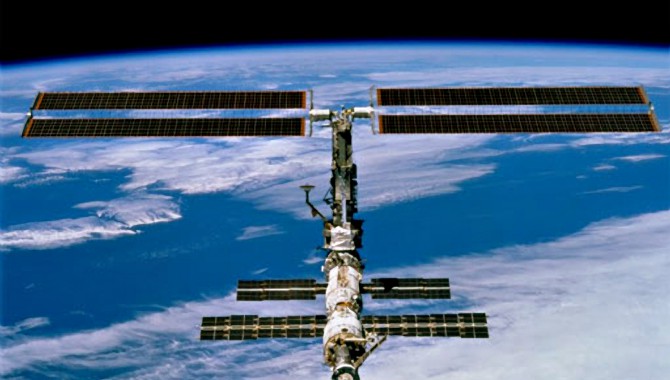
By Tim Howell
As a new International Space Station (ISS) engineering manager in 1986, I quickly learned that having the right mix of people was the key to my team’s success and that sustaining success depended on an environment that encouraged people to pass on experiences. I also learned that maintaining performance over time as team members leave an organization is especially challenging. These revelations would serve as a foundation for Design Knowledge Capture initiatives started in late 1997. What follows is a story about gathering stories from ISS engineers who explained, in their own words, how their designs work.
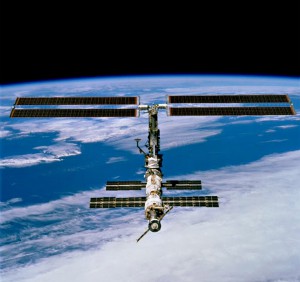
The STS-97 crew delivered and installed the P6 truss, which contains the first U.S. solar arrays, during ISS assembly mission 4A.
Photo Credit: NASA
Design of the power management and distribution system, which I had been part of, was nearly complete in 1997, and engineering design activities were shifting to sustaining engineering, assembly, and test. The Rocketdyne ISS sustaining engineering team began discussions with the Johnson Space Center ISS program office to establish methods for capturing design knowledge. The designs themselves were well documented, but we wanted to meet with as many design experts as possible so they could explain how the space station really worked.
“I don’t want to call a console operator to ask how long a remote-power control module will last before it fails and get an answer quoted from a spec document on that person’s computer,” said the NASA ISS program manager at Johnson. “I want that console operator to tell me what the real design margins are based on what he or she has learned from the person who designed it.” NASA wanted subcontractors to pass on the experiences of the original designers to maintain strong design knowledge over a projected thirty years of on-orbit operation. In other words, NASA was saying, “Show us how it works.”
A Rocketdyne colleague, John Rank, and I developed a proposal to interview ISS subject-matter experts. The plan focused not on collecting documents, but on gathering experts’ thoughts, experiences, and explanations of how and why designs worked. We thought that capturing these “nuggets of knowledge” in their own words would provide contextual explanations that might help a console operator or astronaut in 2010 and 2030 understand the ISS design concepts, strengths, and limits. We knew it would be difficult to capture ten years of collective design knowledge and wisdom, but it was important to the future success of ISS to try.
With limited time and resources, we focused on identifying key experts before they left the program. Our mantra was, “Who is the go-to person?” With the help of team managers and coworkers, we were on a mission to find ISS subject-matter experts who were identified by their peers as the most knowledgeable in their engineering disciplines.
The Design Knowledge Capture initiative had three elements:
- Ask subject experts to help design specific questions they would ask a peer. The questions needed to be specific to the system, hardware component, or software and to the design discipline. We solicited responses from a cross section of engineering and manufacturing program experts in areas including electrical, mechanical, software, and systems. We learned that involving program experts in the design of probing questions yielded richer, more detailed, “how does it work” answers. These same experts were our first interview subjects.
- Establish interview, presentation, or demonstration recording methods. We respected each individual’s willingness to have sometimes very personal one-onone discussions about his or her design development experiences. Asking permission to record video made most people self-conscious and reluctant to discuss factual details for fear of making a mistake, but we assured them that we would not publish their sessions until they had reviewed and approved them. This put most people at ease and made them feel involved in the process.
- Publish Web-based, indexed interview content organized by system (such as power management, thermal controls, or communications).
Planning how to deliver an expert’s information was as important as capturing it. “Capture, Index, Share” was a Design Knowledge Capture slogan. If any of those elements are missing, knowledge cannot be transferred. Indexing was particularly important for quick subject searches and learning retention. No one wants to watch a two-hour interview to get to the information they need.
We established a point person, or “site focal,” at each company we planned to visit. These people knew their organizations well and guided our search for subject experts, especially those who would soon retire or move on to other programs. We asked team managers to identify the most knowledgeable people and then asked these experts to recommend peers. During this process we would ask, for example, what is the most important thing someone should know about an orbital replacement unit, thermal radiator, or blanket-box release mechanism? These leading questions were intended to start a dialogue to help an expert recall design details. We often facilitated roundtable discussions among teammates; one person would remind another of a performance value, margin-of-safety calculation, or the how and why of a test failure. Using video to capture experts’ own words was as close as we could get to placing future students in the room at that moment.
Good learning occurs when one can see, hear, and read at the same time. This is known as the “3–D” effect of learning. What you see may be body language or expression. You hear voice inflections. Reading gives you the details that substantiate the verbal or visual information. Each sensory experience reinforces the others. This rich learning experience improves retention as well as understanding.
Some Stories from the Field
Here are a few examples of Design Knowledge Capture in action.
The First Solar Array–Deployment Assembly Mission
Several months before deployment, design engineers demonstrated solar-array design elements for Design Knowledge Capture video sessions. Sessions included solar-cell design and fabrication, blanket-box release mechanism tests, and arraytensioning pulley design.
Recorded sessions were published to the ISS knowledge management Web site ahead of the launch and assembly sequence. The site was available to NASA and ISS subcontractors to augment existing procedures and specifications. Between 1999 and 2001, the site received on average 2,000 hits per day.
Design engineers knew the array panel material had a surface tension that could cause panels to stick together when deployed after a long period of storage in their protective blanket boxes. The longer the arrays were stored, the greater the possibility two panels would not unfold smoothly. Successful deployment tests suggested this was a minor concern, but random panel surfacetension release caused a yo-yo motion of the partially deployed array during the P6 truss solar-array deployment that resulted in tensioning cables jumping off their spring-loaded pulleys.
Armed with a good understanding of solar-array design, members of the astronaut office and solar-array design engineers designed an extravehicular activity (EVA) cable-retraction tool, video recorded how to reinstall the cables, and transmitted the video to ISS astronauts. Astronauts reinstalled the tensioning cables and successfully deployed the P6 arrays during the next EVA. NASA now deploys the arrays more slowly, with periodic pauses to allow time for panels to unfold and minimize sudden tension-cable retraction. ISS astronauts also have the benefit of a “how-to” training video if the problem reoccurs.
EVA Airlock Design
When we first approached the one EVA airlock systems engineer still working on final design revisions and overseeing the assembly and test of the main ISS EVA airlock, he replied that he didn’t have much to share. This was a common reaction. We all tend to forget what we know or think what we know is not especially important. After explaining that the Design Knowledge Capture initiatives were attempting to capture undocumented design knowledge, he replied, “OK, if it is OK with my manager.” With his manager’s blessing, we spent eight hours recording his explanation of airlock systems design principles. We then suited up with cameras in hand for a clean-room guided tour of the airlock in its current state of final assembly. The mix of documentation and visual and verbal explanation of airlock systems provided rich contextual knowledge. We learned three months later the engineer had left the company to build a house in Alaska.
Battery Orbital Replacement Units
One of the companies we worked with worried that sharing detailed ISS battery design concepts might expose information that would damage its competitive edge or even violate U.S. export laws. Many ISS component designs are based on trade secrets and proprietary information. The solution? Design engineers teamed up to record their design rationale through presentations and one-on-one discussions and edited their recordings before delivering the final tapes to ensure that proprietary information would be protected and correct information would be conveyed. The process of revisiting design decisions and trade-offs was as valuable to them as the final video. The engineers were afforded time to reflect and reaffirm that the designs were the best they could be. These recorded sessions were also used to train others within the company.
A Rich Resource
There are nearly three hundred video stories like these archived in the ISS knowledge management Web site at Johnson Space Center. The site’s one-on-one or group knowledge-sharing sessions are supplemented by written replies to questionnaires and Orbital Replacement Unit Handbooks. Similar methods have been used on the shuttle program. Senior shuttle design engineers provided video-recorded information that was used to train mission-support personnel. The information contributed to a 100 percent graduation success rate for the first class.
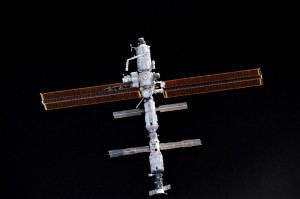
The STS-104 crew used the Space Shuttle Atlantis’s robotic arm to install the new Joint Airlock from which both Russian and American spacewalks may take place. The high-pressure gas assembly supports spacewalk operations and augments the Zvezda Service Module gas resupply system.
Photo Credit: NASA
When we started in 1997, SharePoint, AskMe, LinkedIn, and other social-networking tools did not exist. These tools expand our ability to connect and share. I have wondered what it would be like to have a one-on-one conversation with Albert Einstein through Facebook. But these new technologies do not replace other, older methods of teaching and learning. We learn from each other and we learn by doing. Face-to-face mentoring and roundtable discussions still provide the richest form of knowledge exchange; there is no substitute for engaging in direct conversation where one idea triggers another or point–counterpoint debate leads to a solution. But videos that preserve the subtle body language, speech inflections, and contextual references of a face-to-face conversation may be the next best way to preserve and experience an expert’s explanation of design concepts long after that expert is gone.
We continue to work to bring people together face to face and virtually to share ideas. We encourage knowledge “stewards” to help others discover the wealth of “live” knowledge available within their organization. Through both practice and technology, we have expanded the casual watercooler conversation to collaborative communities with few boundaries. The sharing of knowledge by experts “in their own words” will continue to be an important contributor to successful missions.