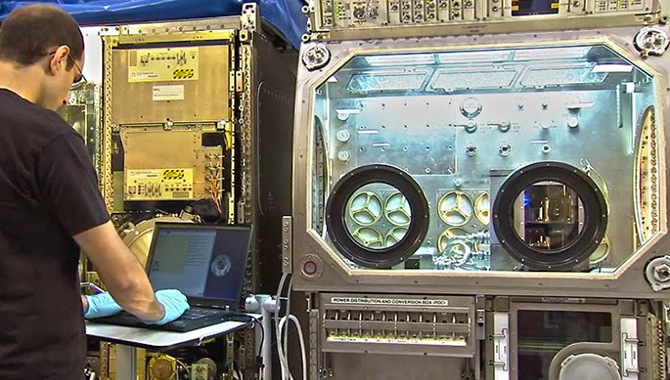
Marshall Space Flight Center tests a 3D printer that will be launched to the ISS in autumn of 2014.
Photo Credit: NASA
A recent report issued by the National Research Council examined the potential applications and challenges for additive manufacturing in space.
The report, jointly commissioned by NASA and the Air Force, found that additive manufacturing could contribute positively to aerospace missions in several important ways. Often referred to as 3D printing or advanced manufacturing, additive manufacturing involves adding layer upon layer of material until an object is formed. The process is already in use for space applications. The spacecraft Juno—currently on its way to Jupiter to explore the planet’s origin and evolution—contains microwave parts produced by additive manufacturing.
The use of additive manufacturing to support space missions is expected to benefit human spaceflight in particular. Developing the ability to manufacture replacement parts or tools to perform emergency repairs in orbit may reduce mission costs. Additive manufacturing technology may also benefit missions to the moon or Mars, where the potential for on-site fabrication will lessen reliance on the transportation of spare parts. The technology has applications for robotic missions as well: it may facilitate the construction of smaller satellites and their components, leading to reduced launch requirements and costs.
However, the true potential for in-space additive manufacturing may lie not in cost reductions but in innovation: the technology could produce a paradigm shift in space architecture. Because in-space additive manufacturing will not be subject to the constraints of gravity-based manufacturing, it could lead to an entirely new way of thinking about structures used in space. Structures produced by space-based additive manufacturing technology will be distinct from those created on Earth in two important ways. First, their design and manufacturing processes will not be subject to the same constraints as structures used in the high-gravity Earth environment. Second, because they will not need to withstand the stress of the launch environment, they can be larger or more delicate than structures currently developed for space use. This may encourage the conception and development of structures with functions and forms that could not be realized without in-space additive manufacturing technology.
Despite its great promise, this technology is still in its infancy. The National Research Council report pointed out a number of issues that must be resolved, including:
- Infrastructure: While some additive manufacturing may be performed on the International Space Station (ISS), eventually a whole new infrastructure—with associated costs—must be developed for manufacturing in space.
- Certification: Standards for parts and tools produced via additive manufacturing must be established, and there must be a way of certifying that the pieces produced in space meet those standards.
- Training: Aerospace organizations will need to invest in training and education in many areas. For example, training is needed for experts in additive manufacturing to apply their knowledge to space-based applications, and for experts in spacecraft design and engineering to utilize their expertise in the additive manufacturing environment.
- Human involvement: Currently, most additive manufacturing processes require human labor. While this is not an obstacle on Earth, human labor is less available in orbit, necessitating an autonomous or semi-autonomous solution.
The report also cautioned that additional development of Earth-based additive manufacturing applications is not likely to benefit the space environment. The markedly different manufacturing issues in a high-gravity versus low- or no-gravity environment, and the kinds of designs that may be developed in one environment versus the other, mark a clear divergence between the two paths.
Instead of looking toward Earth-based applications, the report suggested that research, including workshops with experts in additive manufacturing and spacecraft design and engineering, is necessary to fully assess the technical limitations and performance criteria for additive manufacturing in space. NASA and the Air Force are encouraged to work together to identify a roadmap for developing the technology, jointly sharing costs associated with research while pooling data to advance the initiative. An initial goal is to pinpoint experiments that can be conducted on the ISS over the next 10 years. Over the long term, the report concluded that an approach stressing semi-autonomous in-space manufacturing processes on the moon, Mars, or an asteroid, featuring minimal human involvement, is likely the best path forward.