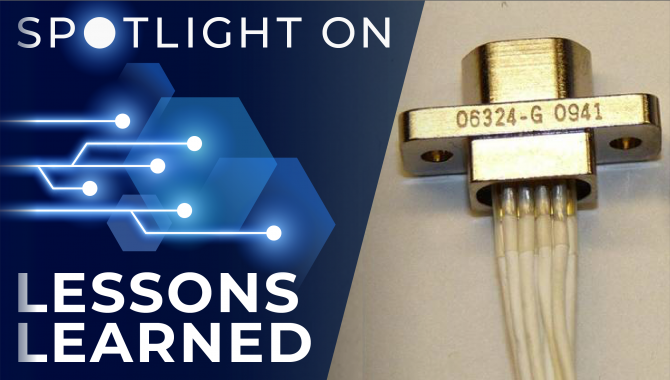
Problems experienced with SpaceWire cable used in flight hardware intended for deployment on the International Space Station resulted in lessons learned and recommendations to help avoid similar issues.
Handling, fabrication, integration and test issues were identified during the use of Gore SpaceWire cable (part number GSC-05-82730-00, size AWG26). One cable stopped functioning after the flight enclosure was shipped to the lab in preparation for system-level vibration testing. Another cable had passed all tests performed during fabrication, but stopped functioning after it was installed in the flight hardware.
After extensive troubleshooting at NASA’s Glenn Research Center indicated a probable short or open on Cable EFA517-001, SpaceWire Cable #3, the cable was taken to the Naval Research Laboratory for further evaluation. Time domain reflectometry tests identified the conductor and location in the cable where an intermittent short existed, and destructive physical analysis confirmed the location of the short.
Cable EFA518 -002, SpaceWire Cable #4, passed all functional tests during assembly, but stopped functioning after it was installed in the flight hardware. Extensive troubleshooting helped determine alcohol used during the post-solder cleaning process was absorbed by the expanded Teflon insulation, wicked its way up the cable, and caused an insulation breakdown and ultimate failure of the cable.
Lesson Number: 6416
Lesson Date: February 3, 2012
Submitting Organization: Glenn Research Center
HIGHLIGHTS
LESSONS LEARNED
- Lack of detailed instructions in the process plan resulted in the omission of protective shrink tubing around the wires when the back shell was installed. The assembly technician was absent and his replacement was not aware the shrink tubing had to be installed as part of the assembly process.
- Expanded Teflon insulation on the individual wires was very soft and susceptible to damage under very light point compression.
- Lack of detail on the cable assembly drawing showing the Micro-D connector face in relation to a right-angle back shell resulted in the connector being incorrectly oriented during assembly.
RECOMMENDATIONS
- Ensure assembly drawings and process plans contain complete, clear and detailed instructions. More than one technician should be capable of performing the required assembly processes.
- Use ethyl alcohol for post-solder cleaning, and do not wipe cable with alcohol after bake-out.
- When installing cables in flight hardware, position and secure SpaceWire cables in place one time and never unbend them.
- When working with a new cable/connector system and lacking previous experience, contact other NASA users for information on problems they may have experienced.
Consult the lesson learned for complete lists.
Spotlight on Lessons Learned is a monthly series of articles that feature a valuable lesson along with perspective from NASA’s knowledge management community on why the lesson is important. The full lessons are publicly available in NASA’s Lessons Learned Information System (LLIS).
If you have a favorite NASA lesson learned that belongs in the spotlight, please contact us and be sure to include the LLIS Lesson Number.