By Dr. Arnold Marder
This year my friend Arlan Benscoter received one of the highest honors in the field of metallography. Arlan was awarded a fellowship by ASM International,* and he richly deserved it.
But what makes Arlan’s selection so remarkable — and controversial too — is that he has no formal education or training in metallography. He is entirely self-schooled. A letter of support from a former president of ASM speaks volumes for how much Arlan has accomplished, considering his background:
Arlan Benscoter is a special case for a fellow nomination in that he does not have an advanced degree and has followed a career path quite different from university professor, industrial scientist, or manager. Nevertheless, he has made outstanding contributions to the development of metallagraphic techniques, the teaching of metallography, and service to ASM.
Nowhere has Arlan’s selection as a fellow been more controversial than in the Academy. Being a professor myself, I am not surprised. Having gone through a Ph.D. program, academics often feel like they have to look at things based on formal principles. Arlan’s approach to metallography is one of practical experience, i.e. working with the microscope. A person can try to guess what has happened to a material based on first principles, but someone like Arlan who can look under the microscope and see what’s going on — that is, someone with a very special skill — and a college education doesn’t necessarily provide you with it.
This reaction to his fellowship is no different than what has been following Arlan his entire career. I have been witness to it from the beginning. I have worked with Arlan for 36 years, first at Bethlehem Steel, where I was a research engineer and he was a technician, and now at Lehigh University, where I am a professor in the Materials Science and Engineering Department and he works as a researcher, assisting students with their experiments under the microscope.
Arlan started at Bethlehem Steel a month before I did in 1965. I was fresh out of college, and he was fresh out of the Army. His talents were not developed at that point — but then neither were mine. Mostly, he was carrying specimens for the engineers at Bethlehem, and then he started to do some testing, and as a result of the testing he started to look into the microscope and use it to evaluate what he saw. That led him into metallography, which is the process of looking at metals in a light optical microscope.
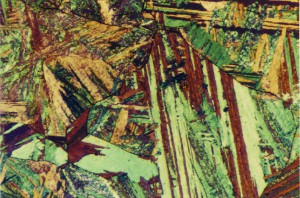
An example of the kind of art found under a microscope. Click image for close-up view. Artist: Arlen Benscoter
At that time I was also a part-time graduate student, studying for a Ph.D., and as part of my dissertation Arlan was helping me evaluate some microstructures. On one particular alloy, he found some tiny cracks on the surface of the material that no one had ever paid much attention to before. These cracks were always passed off as artifacts. Arlan insisted that it was real cracking and had its ramifications on the fracture strength of the steel. I knew if we started examining this it was only going to extend my dissertation, and at that point I wanted to get on with my life. I was reluctant to indulge his curiosity, but he kept insisting that it was important, and eventually he got to me.
Together we looked at the cracks, and it turned out that they were real. As you can probably imagine, there was a good deal of skepticism about our findings. Here were two people coming out of nowhere, one a mere Ph.D student and the other somebody without even a college education. In particular, we were sharply criticized by Bethlehem’s arch competitor at the time, U.S. Steel. This led to what Arlan and I still refer to as “the shootout” between Bethlehem and U.S. Steel. We invited one of U.S. Steel’s leading scientists to Bethlehem to perform an experiment with us. This scientist had claimed that what we were seeing were dust particles on the negative and weren’t really cracks, but when we performed the experiment together, he saw we were right and agreed with us.
As a result of our work, people acknowledged that Arlan had done a good job, but as far as recognition like awards or citations were concerned, there was none. Bethlehem Steel gave him a promotion, and he started working his way up to be the key person in the metallography group at Bethlehem. In many ways, this has been the story of Arlan’s career. People privately recognized his talents, but publicly few were willing to admit that someone could accomplish as much as he has without formal training. The amazing thing is he has never been discouraged by it.
Here is one little story to illustrate Arlan’s special talent. ASM International gives awards every year for photographs displaying the art and science of metallography. There are ten categories. Out of those categories they take the Best in Show. The first person to win the award in 1970 came out of our group at Bethlehem Steel. Arlan helped him put together those photographs. When Arlan came to Lehigh, he started working with graduate students. One of our graduate students won Best in Show. Several years later another student of ours won the grand prize. Then the next year another of our students won Best in Show. This is an international competition. For any institution to win one grand prize is unusual, to win two is very unusual, but to win three — that is unprecedented. This competition is open to people who have been working in the field for 20 to 30 years. Competing against students? In his typical way, Arlan refused to put his name on any of the entries. Only the students’ names were recognized as the winners.
In 1996, he was given an award by the university for teaching excellence. This was for the best teacher in the engineering college at Lehigh. The students that year felt that he was the best teacher they had ever had. What made this so unusual was that he does not have a position as a professor in the department. He’s the first person ever to get the award who isn’t a professor.
Some professors were upset that someone without a degree could be picked as the best teacher in the engineering college. Students don’t seem to suffer the same skepticism that certain faculty members are plagued by when it comes to recognizing Arlan’s talents. Every year in their exit interviews, invariably, the students point to him as one of the best experiences they have had in their four years at Lehigh.
As much as anybody in our department, Arlan has been instrumental in improving our reputation in the Engineering College. Years ago, for instance, the department was down to only five students per year. One of the things we decided to do to improve things was to invite pro s p e c t i ve students to open houses. It was Arlan’s idea to take undergraduates and put them on all the instrumentation. The prospective students would go around to each of the demonstration rooms and see our students working on all the instrumentation that Arlan had taught them how to use. As a result, our enrollment increased significantly. Students saw this as evidence that Materials Science and Engineering is a hands-on department. Why do I give Arlan most of the credit? One year the Associate Dean said no more open houses. The next year’s enrollment went down substantially.
When I left Bethlehem in 1986 and joined the faculty at Lehigh, I was bent on getting someone like Arlan to run the metallography lab. Who better to have than Arlan himself? I went around asking people to support him, and I lost a couple of pairs of trousers wearing my knees out trying to get everyone to contribute, but we got the money to support him and so then it was just a matter of getting him interested in the position.
Before Arlan came to Lehigh, it had an under-equipped microscopy lab. Having known Arlan for 21 years, I knew how he would react. Bethlehem had a pretty good setup that he had put together. Lehigh still had mostly one-eyepiece microscopes.
“You want me to work here, with this junk,” he said after I showed him around.
Arlan and I had worked together at Bethlehem for a long time and I thought I knew him well. I was prepared for this, so I said, “What’s the matter, aren’t you up for a challenge?”
That was all I needed to say, apparently. He took the job. I doubt he’s ever looked back on leaving Bethlehem with regret.
A month after he started working here, Sandy, his wife, said to me, “What did you do to my husband?”
I said, “What you mean? I’m just letting him do what he wants.”
“I don’t understand what’s happened to him,” she said. “He comes home smiling. He comes home whistling. I’ve never seen him so happy.”
This is the real reason his students love him, I believe. Plenty of people have high standards, but Arlan just exudes love of his work. I see it; the students see it; everyone who is exposed to him sees it. He just doesn’t think about the time he puts in because it’s not like a job to him. This is his mission in life. It has nothing to do with collecting paychecks at the end of the month.
My friend Arlan Benscoter has taught me a great deal about humility. Certainly he has taught me that an academic degree is not a prerequisite to being successful at metallography — or anything, for that matter. While Arlan may not have the academic pedigree, there is no way you could ever say to him, “What do you know? You don’t even have a degree!” People like Arlan are special not just because they love to learn, but because they learn in their own manner. And what that entails generally is learning by experience.
Lessons
- Those who are successful at helping others learn need not necessarily be formally trained as teachers.
- Those who love their discipline work hard at it because it fuels their passion.
Question
In your opinion, is project management closer to art/craft or science/technology?
*ASM originally stood for American Society of Metals, but since polymers and ceramics are now also recognized, it was decided to keep the acronym and dispense with the full name.
Search by lesson to find more on:
- Challenging the Status Quo
- Professional Growth
- Testing