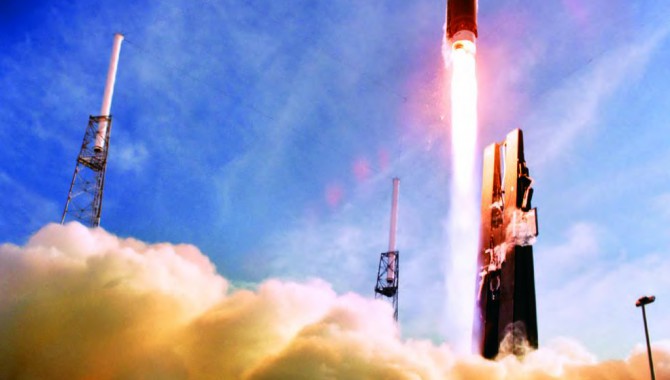
Darren Bedell
As the final “go for launch” was given for the Mars Reconnaissance Orbiter (MRO) mission on the Atlas V 401 launch vehicle, the hair on my arms stood up. The pride of what we were about to accomplish, and the nervous tension of really knowing the risks of space flight, had come to a head.
The MRO mission was the first NASA mission to use the new Atlas V launch vehicle. In fact, it was the first U.S. government launch on the Atlas V. While each NASA mission is important, going to Mars is a very big part of the Agency’s goals, and public interest has always been high for missions to the red planet. A few years back, the Headquarters Program Administrator was trying to get the Kennedy Space Center Launch Services Program’s (LSP) attention for a seemingly less important mission on a small rocket. “Treat it like a Mars mission,” she said, “the most important thing that we have; we have to make it work.” For a Mars mission, everyone’s sensitivity to mission success is higher than it is for a typical mission.
There have been great successes in going to Mars, but there have also been failures. My career has afforded me the opportunity to work on every Mars mission NASA has launched since the Viking missions, and I’ve seen both. While none of the failures were due to the launch vehicle, it really hurts when something goes wrong because everybody involved puts so much effort into these missions. Everyone works hard for mission success, which amplifies the anticipation and emotion at every launch.
I’ll never forget the day the Mars Climate Orbiter arrived at Mars in 1999. I was in a small room in a contractor’s plant in California, listening to the real-time operations going on at the Jet Propulsion Laboratory. I had just learned the mission had failed. I walked into a conference room filled with people who had worked on the launch phase for three years — my face was surely pale — and announced to everyone that “they just lost the Mars Orbiter.” Facing these people was very difficult, a scar that I carry with me to motivate myself and our technical team when faced with tough choices on resource deployment, prioritization of issues, and final readiness for launch.
Making a New Checklist
At the beginning of a mission’s life cycle, the planetary launch period is in your mind with each decision you make. As you get closer to launch, it really starts to stare you in the face. Taking more time to get it right isn’t an option because a Mars planetary mission can only be launched once about every twenty-six months. However, completing the work on time only to experience a launch failure due to our error is what we all feared the most. Facing another launch, this time on a vehicle with very limited flight history, we were determined to get everything right.
The Atlas V was developed commercially by Lockheed Martin, with some of the funds provided by the United States Air Force (USAF) under the Evolved Expendable Launch Vehicle contract. Because new rockets have a history of failure during their first few flights, the Agency established a policy in the 1990s to govern NASA’s requirements for using new launch vehicles. The policy was meant to ensure the quality of commercially developed launch vehicles because NASA buys launch services from the industry, which means NASA does not own or control the development of a new launch vehicle.
The Launch Services Program Technical Staff was responsible for refining and implementing the Agency policy in preparation for the MRO launch. In addition to certifying the Atlas V according to policy requirements, the LSP also performed technical oversight of the hardware and unique analyses required to successfully place MRO on its way to Mars. NASA certification only happens for new launch vehicles, and it is meant to ensure the highest practicable probability of mission success for all future missions to be flown on the vehicle.
We had to figure out how to assess the Atlas V for NASA certification because no checklist or definitions existed for new rockets with less than fourteen consecutive, successful flights. To solve the problem, I called my Chief Engineer, James Wood, and my Branch Chiefs, Pat Hanan, Mike Carney, and Jim Robinson, into my office. We knew that most of us would be there giving a “go” for the first launch on the Atlas V, so we needed to come up with something that we could live with that day, something we could accomplish in time, and something we could stand behind when we were asked for our “go.”
Creating a Cornerstone for Success
We based our decisions on the risk we would eventually face on launch day, and we referred to a list of previous NASA assessments. The previous assessments gave us a starting place, but the certification items on the list did not apply to this new category of launch vehicle. We really had to think about what would work for certifying the Atlas V. We emphasized the importance of hardware qualification because of our experience with previous launch vehicles failing due to hardware malfunctions, and we added an assessment that used a cause- and-effect “fishbone” technique that identifies potential failure modes and their mitigations. The combination of flight data review for three flights, hardware testing, analysis of the new Atlas V, and failure mode mitigation became the cornerstone of our NASA certification effort.
As we created and refined our certification process for Atlas V, we realized getting to “go” before we could launch MRO would take about four times the effort of a typical NASA mission because we were using a new rocket and we had to certify it. My first thought was to ask for additional personnel. However, the same Program Administrator who once told me to treat another mission like a Mars mission, the most important thing we have, also told me I was not getting any more people.
To help solve the problem, I had to look outside Kennedy. We partnered with the USAF, National Reconnaissance Organization (NRO), and other NASA centers to perform some of the technical work required for certification. For all information obtained from a partner, the LSP retained technical cognizance of the work performed by the other organization and held all technical and risk decision authority for that effort.
Through a series of government launch vehicle collaboration meetings, the similarities and differences in the LSP, NRO, and USAF approaches to technical evaluation were discussed. Each organization knew that resources were limited, so finding a way to work together would be important. But we reached no definitive agreements during the first two years of the collaboration. We were all on unfamiliar territory and therefore lacked the trust necessary to reach an agreement. We also didn’t understand the language of the other organizations, so this new collaboration started very slowly and carefully. To address these issues, we agreed to gather everyone together for one big meeting each year and supplement it with smaller meetings when necessary. As a result of these meetings, the most notable element of the partnership emerged. It involved using Lockheed Martin’s Design Equivalency Review, which the NRO funded. NASA engineers worked with Lockheed Martin, USAF, and NRO engineers, and we partnered with Marshall Space Flight Center and Glenn Research Center to increase our technical staff.
We used the equivalency review to document most of the information we needed for the LSP hardware qualification assessment. James Wood and I knew the Lockheed Engineering Review Board process in detail, and we knew the NRO/USAF participation in the review board would be significant, which allowed us to relax our requirement for conducting a separate NASA Engineering Review Board. We required our engineers to participate in the Lockheed engineering review and to conduct a unique NASA evaluation of each component. We also shared our systems engineering evaluation of the components with the NRO and alerted them to any NASA findings they might want to consider in their own evaluation.
Changing Course
At the beginning of the Design Equivalency Review, we were understaffed and the information was coming in too quickly for us to handle. Our approach to managing the LSP effort had to be changed in the middle because we had too many elements and not enough dedicated leadership. Pat Hanan, who had become the Engineering Division Chief at the time, brought in Dave Sollberger to organize the effort and provide detailed tracking plans to account for all the work being performed by the multiple organizations. For undefined problems or new approaches, establishing the management system is as important as defining the technical work. We learned the hard way that it was better to find a way to avoid falling behind schedule early in the process instead of having to play catch-up just before a deadline that can’t be moved. Dedicating someone to manage the relationship with the partner is imperative.
By the end of the equivalency review, the partnerships with other NASA centers were in place, and the information wasn’t coming in as fast as we needed to support the planetary launch window. We knew this because of the project management system Dave Sollberger had developed. Problems included delays in USAF launch dates, changes in personnel, and priorities of the Columbia failure investigation at our partner centers. The talented engineers throughout the government have a lot to offer; however, partnering is no panacea. We had to consider the efficiency of the support we received based on the particular agreement and situation, and we were not always in control of our destiny. That is what makes the completion of this effort even more remarkable.
When I think back on hearing the final “go for launch” during the MRO countdown last August, I hope you understand why the hair on my arms stands up in excitement. I know how much thought and hard work it took to reach that moment, and how important a moment it was for the American Space Program.