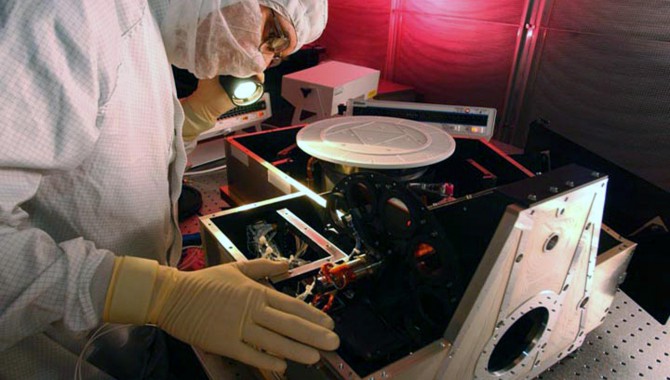
By Rick Grammier
How do you hit an object zipping through space at 23,000 mph, 268 million miles from Earth, and capture what happens after the impact with a camera 300 miles away? In 1999, a team of more than 250 scientists, engineers, managers, and educators set out to meet that challenge and discover what exists inside a comet.
The idea originated in 1978, when Alan Delamere, an engineer at Ball Aerospace & Technologies, and Mike Belton, then at the National Optical Observatory in Tucson, analyzed data from Comet Halley and found the comet was far blacker than they had anticipated. “So we asked ourselves: how could this happen?” Delamere said. The search for an answer evolved into a proposal by Dr. Michael A’Hearn (University of Maryland) to NASA’s Discovery Program to hit an active comet and gather data on its inner material and crust. When the idea was approved in 1998, it became eighth in the Discovery Program’s series of low–cost, highly focused space science investigations. It would be the first space mission to look beneath the surface of a comet.
A first–of–its–kind mission and tight budget weren’t the only challenges awaiting me when I joined the team as project manager in January 2004. The launch had already been delayed one year. If Tempel 1, the target for Deep Impact, sped beyond a reachable orbit from Earth, we would have to wait another five and a half years before the comet would circle around again. With the project already at risk of being canceled by NASA Headquarters due to significant financial overruns, a five–year delay was not an option. With one year remaining until Deep Impact’s last chance for launch, I faced a project with a fractured team and split responsibilities, incomplete development of flight avionics hardware and software, and a system–level verification and validation program that had not yet begun.
Contributing Factors
Though the largest visible contributor to the launch delay was the development and delivery of the flight avionics, many other causes contributed to Deep Impact’s problems. Cultural differences between the Jet Propulsion Laboratory (JPL) and the system contractor, knowledge and experience gaps within the combined team, and an eviscerated independent check–and–balance process led to miscommunication and misunderstanding. The cultural differences were primarily rooted in the distinction between Earth orbiter missions—using spacecraft architectures similar to those flown previously, which the system contractor was very experienced in—and a one–of–a–kind, complex planetary mission like Deep Impact. A good example of the difference between these types of missions is in the complexity of fault protection software required for each. An Earth orbiter may simply enter safe mode due to a fault occurrence; a planetary spacecraft will try to autonomously diagnose the fault and recover from it, entering safe mode only as a last resort. The cultural differences resulted in a great deal of misinterpretation and mismatched expectations that had to be continually recognized and managed.
The contractor’s lack of deep space mission experience also had a significant impact on defining and planning for the flight system validation and verification (V&V) program. The contractor understood the need to validate that requirements were met for each component but not the importance of verifying that the flight system could operate as intended when all the components were assembled. This “test as you fly, fly as you test” approach had not yet been implemented on Deep Impact; combined with late system maturation, this presented a significant challenge to completing the V&V program in time for launch.
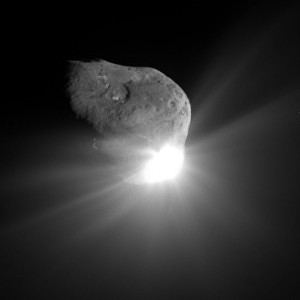
This spectacular image of comet Tempel 1 was taken 67 seconds after it obliterated Deep Impact’s impactor spacecraft. Scattered light from the collision saturated the camera’s detector, creating the bright splash seen here.
Photo Credit: NASA/JPL–Caltech/UMD
Yet another source of problems was ineffective teaming arrangements between JPL and the system contractor. It was not always clear which organization had product delivery responsibility at each level and life–cycle phase. In some instances, the organization with delivery responsibility didn’t have the necessary skills or experience to deliver the product. This was further complicated by a lack of effective management and leadership at multiple levels within the project.
Finally, the project had an inadequate flight operations concept and plan. The original mission was designed to have an eighteen-month cruise period prior to encountering Tempel 1. The one–year launch delay reduced the cruise period to six months, yet the amount of work that had to be done stayed the same; the management team never truly appreciated or analyzed the implications of this schedule compression. The operations schedule and staffing plan were also inadequate to accommodate such a workload, and the system contractor originally given the responsibility for conducting mission operations had no prior experience in conducting operations of this magnitude and no familiarity with the various ground systems and processes that were required. Last but not least, earlier budgetary problems meant that insufficient staffing and funding were available to appropriately plan for the operations and conduct the necessary operations team training.
Change in Course
Acknowledging the challenges I had in getting the project on track and meeting the launch date, the first thing I did was hire an outstanding deputy project manager, Keyur Patel, to help share the tremendous workload and grueling travel schedule.
Together, we focused on opening all communication channels and ensuring our expectations were known and understood by all involved. We then established an alternating, weekly travel schedule that had one of us on site at the system contractor facility every week in order to enhance communication, quickly identify and resolve problems, reestablish an integrated team, and provide for efficient knowledge transfer. Next, we held several working meetings to go over JPL’s flight project practices and design principles to communicate expectations regarding project implementation and design practices and to bridge cultural differences. These had been previously reviewed in a piecemeal fashion and were not well understood across the entire team in the context of Deep Impact. The real value we gained from these meetings was in discussing together what each requirement meant and understanding whether each one was met or not. Not meeting a particular requirement wasn’t necessarily a bad thing, as long as we all understood the risk of each exception and whether or not that risk was acceptable. Engineers from each subsystem, as well as senior and mid–level management, participated in these meetings.
One lesson I learned early in this process was to check that actions the team had agreed to were actually done as intended. I would converse with the contractor’s management or engineers and think we had an agreement; then I would come back to check on it, and find that the way they had worked on it was different than I expected. This was another manifestation of our cultural differences. I learned that at the end of these conversations the best thing to do was to say, “I think we decided this, and you’re going to do x, y, and z. What do you think?”
We also reestablished the mission assurance (MA) rigor that had been eviscerated somewhere along the way. A few months before I came on board, an MA audit team had been formed to determine the state of affairs and provide recommendations. Nothing had been done with the recommendations, so we formed a Tiger Team of experts to implement them and correct the deficiencies. This was a painful and costly process, but you have to do the right thing right. It paid big dividends in the end.
We also changed how often the management review process occurred. Less than a year from launch we had a huge list of issues and risks and a lack of communication; I couldn’t wait for a monthly meeting to hear about the issues, so we moved to a weekly process. Because there were so many issues to review, we didn’t try to solve every issue in each meeting. We frequently defined action items and moved on, then revisited the actions the following week. I also invited the NASA Headquarters program executive and program office to call in to the meetings so they were aware of the issues and able to witness the progress being made. This helped keep the team focused on priorities from week to week while ensuring the management team was aware of the “big picture.”
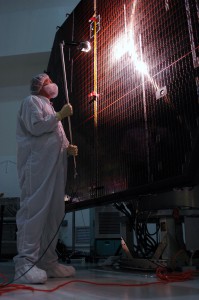
A technician at Astrotech in Titusville, Fla., conducts an illumination test on the Deep Impact spacecraft as a final check of performance.
Photo Credit: NASA
Once the team found a better way to communicate, Keyur and I focused on helping them work better together as well. I organized the product teams—by component, subsystem, or some other deliverable—to take advantage of flight project experience and specific product knowledge, combining JPL and contractor members within teams. We also provided continuous management and engineering presence at the contractor site, which helped improve communication through continuous interaction. This enabled the teams to more quickly share knowledge and identify and resolve problems together. Over time, this directly contributed to re–integrating a fractured team, building esprit de corps, and establishing an appreciation for team members’ expertise and dedication to getting the job done. Make no mistake about this: the teams on both sides of the Rockies were very smart, very dedicated individuals. The challenge here was to provide the team with the resources, tools, experience, and leadership to get the job done.
Mitigating the Impact
These changes allowed Deep Impact to launch on schedule on January 12, 2005, but the problems were far from over once the mission was headed for comet Tempel 1. At launch, Deep Impact still had not passed a test encounter with the comet. Contingency plans for the encounter had also not yet been identified, developed, or tested. The operations team had been certified and trained but were still green in terms of hands-on experience. In short, too much work remained for the current size of the operations team.
To address this shortage, we retained a majority of the development team and continued to use the processes that had so successfully gotten us to launch. The daily operations were jam packed from day one, and we increased the staff tremendously in order to get the work done. We also formed an Encounter Working Group (EWG) to complete development and verification of the encounter plans, sequences, and contingency operations. This team was effectively “fire walled” from the day–to–day operations team so it could concentrate on the encounter development and V&V activities. This did cause some issues with bench depth and knowledge transfer to the daily operations team, but it was absolutely necessary in order to complete the tremendous amount of work in such a short time.
Together we generated an elaborate decision tree, identifying every contingency that might prevent success. For example, if the small impactor had a failure prior to release, we had a contingency plan to either delay the release with a different maneuver sequence or target the entire flyby spacecraft (with impactor attached) for collision with the comet. We planned how to address each possible failure in detail so we would be prepared to salvage the science and mission under as many conditions as possible. We also conducted three risk reviews with the EWG and senior management to alert us to other issues or solutions we may have overlooked.
Big Bang
After an intense year of preparation and another six months of around–the–clock operations, the larger flyby spacecraft released its small impactor and maneuvered away from the impending collision to capture pictures of the impact. On July 4, 2005, Deep Impact successfully collided with comet Tempel 1—with no failures or surprises. The images of the approach, the impact, and its aftermath were relayed to Earth and will be analyzed and combined with data from other comet missions, leading to a better understanding of both the solar system’s formation and implications of comets colliding with Earth. Creating a culture of open and honest communication and rearranging teams to ensure everyone’s strengths were used wisely helped make this groundbreaking mission a comet–shattering success.