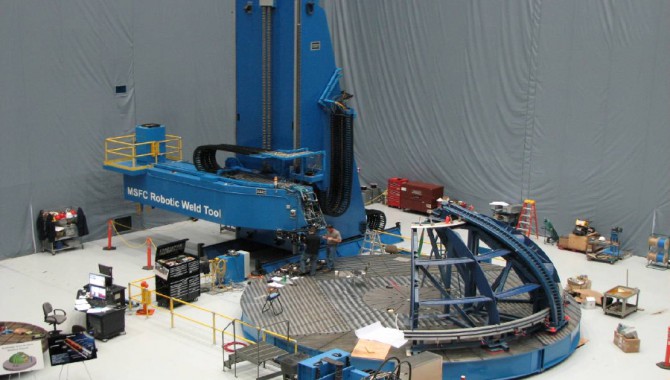
By Stephen A. Cook
Organizations are like people—sometimes it takes a major shock or a disaster to change their behavior. For NASA, the shock occurred on February 1, 2003, when Space Shuttle Columbia broke up on re-entry. Even as we mourned the loss of the crew, many at NASA began some serious soul-searching. The Columbia Accident Investigation Board (CAIB) was formed within two hours of the accident. In addition to the technical reasons for the disaster, the CAIB report cited management and cultural problems inside and outside NASA. They faulted political leaders for not giving NASA a clear mission and faulted NASA for weakening its in-house engineering and safety organizations. In response, policymakers developed the U.S. Space Exploration Policy to provide the Agency with a long-term vision. And NASA changed internal structures and practices to strengthen engineering and safety.
NASA’s New Approach
The CAIB report advised us to establish a strong engineering technical authority and focus on safety as a core engineering discipline, rather than relying on industrial safety policies. Establishing the Safety and Mission Assurance and Engineering Directorates as separately managed and separately funded entities means that NASA engineers in those organizations can be more forthcoming about raising safety issues without fear of retribution.
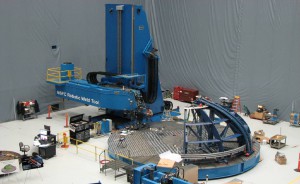
This robotic weld tool at Marshall Space Flight Center is configured to assemble the domes at the ends of each of the Ares I Upper Stage propellant tanks.
Photo Credit: NASA
Engineering and safety are closely linked in a discipline as demanding as space flight. Every engineering decision has flight safety consequences, so our engineering and safety teams must be staffed with competent engineers and space systems managers to ensure we are applying an effective risk-based approach to the design. Routine, open, and honest communication among project management, engineering, and safety is a must. Cost, schedule, and political constraints exist in any project; all the parties have to understand them clearly and find creative ways to work within them. For Ares, we are cultivating a “Yes, if …” rather than “No, because …” culture by giving NASA civil servants a product ownership role.
NASA Administrator Mike Griffin gave us one clear directive for managing the Constellation program: NASA must own the intellectual property rather than use a proprietary design developed and owned by a contractor. The Agency used this development model to build the Apollo crew capsule and the Saturn launch vehicles in the sixties, but it is a new way of working for the current NASA team. For thirty years, NASA deferred to private industry for launch vehicle development and operations. We needed to get our hands dirty by delving into the details of development.
Ares Projects—Owning the Product
The Ares projects at Marshall Space Flight Center are charged with developing the launch vehicles to get the Orion crew exploration vehicle and Altair lunar lander into space. The Ares I crew launch vehicle will lift off from Launch Complex 39B at Kennedy Space Center using a five-segment solid rocket motor based on the ATK Launch Systems four-segment motor used on the Space Shuttle. The upper stage, powered by a liquid hydrogen/liquid oxygen J-2X engine—a modern version of the Apollo/Saturn J-2—will push Orion to low-Earth orbit.
To accomplish this enormous task, we have revived Wernher von Braun’s practice of building and maintaining in-house engineering and safety expertise, but we have incorporated modern management practices, such as Lean Six Sigma and Kaizen, establishment of team norms, and an all-digital model and manufacturing process. Rather than reviving the top-down management of the 1960s, we are empowering engineers at all levels to identify improvements in their daily processes.
NASA Marshall and our partner centers are responsible for overall vehicle or “stack” integration and developing the upper stage in house, with an innovative partnership with Boeing for production. In addition, we are using Boeing’s propulsion expertise to work very closely with first-stage contractor ATK Launch Systems and upper-stage engine contractor Pratt & Whitney Rocketdyne to develop these two key elements.
In-House Development in Action—The Ares I Upper Stage
One of the managers most affected by these changes is Danny Davis, the Ares I upper-stage manager. When asked to sum up his job, he said, “The NASA design team is responsible for all design, development, and testing of the upper-stage system. We are reducing development risk and cost by incorporating state-of-the-art technologies and minimizing the need for new technology development. We also have to reduce the overall cost of ownership of the upper stage by considering early in the design process the input of the Boeing team that will fabricate the stage and the operations team that will handle and operate the stage.”
According to Davis, the upper-stage production system is being designed along with the upper stage itself, with the upperstage production contractor (Boeing) providing “producibility” input to the NASA design team: “The NASA design team has exceptional capacity and passion to implement the upperstage development and operations. For example, during one ‘lean’ event that included both NASA and Boeing personnel, the upper-stage team cut 100 days off the time it takes to manufacture a stage.” One major savings came from Boeing’s suggestion to tack weld the upper-stage barrel segments in a vertical orientation rather than build the stage horizontally, an insight gained from building Delta IV launch vehicles. The NASA/Boeing Kaizen team took that process one step further and decided to completely weld the barrel segments together vertically, resulting in substantial assembly time savings.
Tim Vaughn, chief of the Metals Engineering Branch of Marshall’s Engineering Directorate, works with Davis on the upper stage. He has been on the leading edge of Ares development, and his team is working on the stage from the production angle: “We do weld development, materials and failure analysis, metallurgical engineering, and sub- and full-scale manufacturing and assembly. We are key players in the manufacturing and assembly area. We are developing all the components, manufacturing processes, the tools, and fixtures, and we’re demonstrating all that with full-scale hardware.”
Vaughn’s team has started nearly from scratch. It has been forty years since NASA built rocket stages on this scale, and the technology has progressed quite a bit since the days of Apollo. As Vaughn explains, “There was nothing ‘heritage’ that we could draw upon except industry infrastructure and the initial development experience from the External Tank Program. Today we are using the strongest and lightest aluminum alloy currently available, Aluminum-Lithium 2195. It’s difficult to weld and form. We are also using the friction stir weld process for all major structural welds. Our goal is to take advantage of all state-of-the-art technology development that we have available.”
Developing the Team
Of course it’s not just a matter of building the hardware. On top of the fundamental tasks of developing qualified components, manufacturing processes, and tooling fixtures, Vaughn notes, “We also need to develop people. All the components are new, and all the people are new. Everything we do on a day-to-day basis is new. Most civil servants and contractor partners have limited full-scale production experience, but they’re all bright people and we’re all learning. Everybody is enjoying learning how to go about doing this.” He adds, “Engineers love to build things. I’ve got engineers who had been pushing paper for years now responsible for developing hardware components, and they’re having the time of their lives. I’ve got welding engineers who are absolutely having a blast trying to figure out the best and most efficient way of assembling tank structures. There is no problem whatsoever motivating people. Everybody understands that what they are doing will be used as a basis for the next twenty to thirty years. Future generations, not just NASA engineers, will be using what we developed. This is engineering Shangri-La!”
Changing the Culture
Why is Ares’s shift from an oversight to a development culture so important? As Vaughn puts it, “When you do development, you’re starting from ground zero, and you get to design and develop the type of vehicle that you think needs to be developed. The design is being done in house, and we actually get to have input on how the design is being built, how we’re going to manufacture the vehicle, and to me that’s the beauty of engineering.”
Asked if there were disadvantages to this culture change, Vaughn replied, “There are people who do not like the responsibility and the accountability that this new direction gives you. It’s easy to sit back and criticize something that someone else has done, but to stick your neck out and say, ‘This is the way it’s supposed to be done,’ is the key difference. The things that we’re doing now, ten to fifteen years from now, someone’s going to be critiquing or, if we are successful, using our program as a model to follow. We have to make decisions that influence the direction of the space agency, at least in terms of manufacturing, and that is an uncomfortable position for some people.”
When it comes to the cultural changes within the upper stage, Davis says, “We learn every day what it means to ‘own’ the development. Our team is making binding decisions and working through problems, being innovative, and listening to the ‘wise owls’ who provide advice. We also listen carefully to our production contractor to make sure our design is carefully thought out for all aspects of our mission.
“The NASA design team is fortunate to have several of the men and woman who participated in the development of the Saturn and Space Shuttle launch system available for consultation and advice. Many of our advisors were in top management roles and understand the complexity and details of the job ahead of our team. They know the exhilaration of successfully accomplishing the mission. Each of them has relayed that our job is not easy—you must be tough and persistent and never give up—but in the end the space program and our nation will benefit from the sacrifice made by our team. Encouragement from someone that has been there is priceless.”
When asked how his team approaches the Ares project, Davis added, “Our team is committed to forging a minimumcost development and operational design by a close partnership with our production contractor and the operators who will inherit our hardware. Each team member owns the cost and operational efficiency of their respective components and subsystems. We ensure this by insisting on strict accountability for development and recurring costs, and modeling of the stage operations. Each team member owns the life cycle of their respective design.”
Vaughn adds, “One of the culture changes we’ve had to make is moving to a ‘badgeless’ organization. What you want to do is set up an organization working a series of major tasks to have the latitude to assign lead roles to the best people. The best people aren’t always civil servants. I’ve assigned lead roles for component development, weld tools, and various other technical tasks to Boeing, our Ares I production contractor, and Jacobs Engineering, our engineering support contractor. I’ve got contractor personnel and government personnel working together as teams; contractor reporting to contractor, contractor to government, and government to contractor. There has been resistance, but when you have the best people leading major tasks, it pretty well takes care of itself.”
Preparing for the Future
Rebuilding an “oversight” culture into a “doing” culture may be more difficult than building a new rocket. Vaughn notes, “There’s management theory that says it takes from three to seven years to change the culture of an organization,” and emphasizes the patience and persistence needed to take a group in a new direction. Bringing critical work in house ensures a knowledgeable civil service workforce that understands the work to be done, owns the products and processes, and uses resources wisely. Owning the product and process is giving NASA’s workforce the knowledge and skills needed to ensure the future development of the Ares V cargo launch vehicle and Altair lunar lander and, ultimately, to fulfill the challenges of the new U.S. Space Exploration Policy.
About the Author
![]() |
Stephen A. Cook is the Ares project manager at Marshall Space Flight Center. |