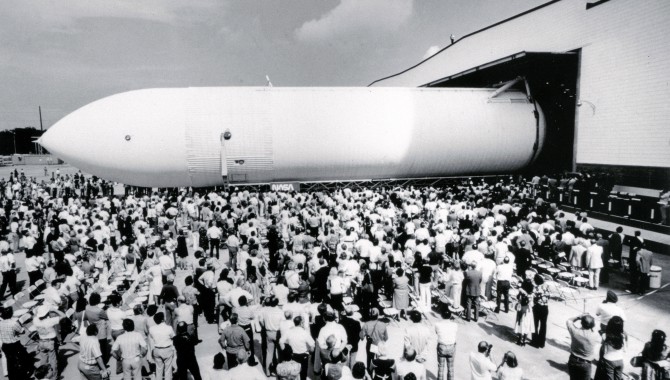
By Russel Rhodes
There is more to a ballistic rocket than hardware and software. Think about all the fluids required to power its systems. There’s a lot more than “rocket fuel” involved, especially as these systems grow increasingly complex to meet the innovative demands of groundbreaking science and exploration. Not accounting for fluids early in development can create complex systems integration and management issues later on and dramatically increase operating costs. Designing for efficient fluid management will be an important element of making future spaceflight reliable and affordable.
Because rockets require such precision equipment, the fluids that power them also have to be precise. This means the fluids have to be pure, carefully controlled, and verified to meet designers’ specifications.
In the early years, flying a rocket required only propulsion fluids, a coolant, air-bearing gas for the guidance system, and sometimes hydraulic fluid for the controls system. The Jupiter rocket, for example, used only eight fluids in the mid-1950s. Compare that with the Space Shuttle, which required twenty-seven fluids (fifty-four if you include the cleaning and testing fluids involved) with 102 locations, and you can begin to see that the complexity of fluid management and the cost of preparing a vehicle for launch drastically increased in just a few decades.
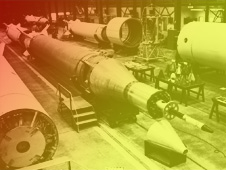
Jupiter-C Missile No. 27 assembly at the Army Ballistic Missile Agency in Huntsville, Alabama. Jupiter-C successfully launched the first American Satellite, Explorer 1, in orbit on January 31, 1958.
Photo Credit: NASA
Because rockets require such precision equipment, the fluids that power them also have to be precise. This means the fluids have to be pure, carefully controlled, and verified to meet designers’ specifications. In the beginning, the Army Ballistic Missile Agency Missile Firing Lab—which was later transferred to NASA—relied on the air force to perform this verification. Once Kennedy Space Center was developed, NASA assumed these responsibilities, but our efforts were not organized efficiently. With little technical management oversight, each systems engineer had to ensure the fluid verification was completed for his or her particular system. This worked well enough when less than a dozen fluids were required, but our leap into human spaceflight quickly expanded the number of required fluids.
With the age of Apollo came the need for fluids for life-support systems. At the same time, launch-vehicle systems became much more complex, relying on multiple stages to push humans into space. And those different stage elements weren’t required to use the same fluids. With the number of fluids growing rapidly and no integration or technical oversight of fluids management at the program level, keeping the fluids pure and the system clean quickly became a greater issue.
In one case, filters were not performing as predicted. These spacecraft filters were recleaned at Kennedy and given a 10-micron rating, but they were discharging much larger-diameter particles, which would cause component failures. During the resulting failure investigation, we discovered the filter manufacturer was performing the assembly in an uncontrolled environment, trapping contaminates in the filter. Recleaning the filters failed to remove these trapped particles, and they would end up shedding during operations to contaminate the system. This problem was resolved by having the filter manufacturer change its processes to first clean the double-Dutch-twill filter cloth with other filter parts and then assemble the filter in a clean-room environment.
The Apollo-era practice of taking fluid samples at the flight-to-ground interface when servicing operations began was another important contamination-control requirement that would have caused issues if implemented on the Space Shuttle program. Launch-vehicle personnel realized that obtaining samples at the ground interface was not a practical or safe way to verify large cryogenics systems because the launchpad area was always cleared of all personnel before servicing the vehicle. To solve this issue, they developed a technique to sample fluids in the ground-servicing container instead and then carefully control the environment when the fluids were later transferred to the flight vehicle. This approach, along with the use of a qualified final filter, proved to be a technically adequate solution and was later written into a single procurement-and-use control document. This allowed for consistency in keeping fluids clean and verified across an entire program.
Additional changes required for fluid management became more evident as NASA transitioned from Apollo to the Space Shuttle. The shuttle program was to be managed from a lead center with responsibilities divided among the NASA spaceflight centers. Because the lead center knew there would be many fluids required to support the shuttle flight system, the management team wanted visibility into and control of the procurement and use of all fluid commodities.
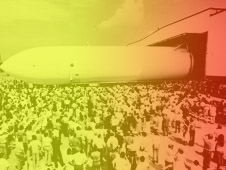
The first Space Shuttle external tank—the main propulsion test article—rolls off the assembly line on September 9, 1977, at Michoud Assembly Facility in New Orleans, Louisiana. The tank contains two tanks, one for liquid hydrogen and one for liquid oxygen, and a plumbing system that supplies propellant to the main engines of the orbiter
Photo Credit: NASA
The result was a single document describing an integrated approach, by subsystem, to controlling all fluids used by the shuttle elements. There was never any disagreement on using a single document to provide a uniform and consistent method for managing all fluids, but there were differences in the approach to this task that needed to be worked out. The three prime centers got together to work through the differences and compromise on a consistent method, relying heavily on experience to inform their decisions. For example, they invited launch-vehicle operations personnel to provide insight into the discussion since they had considerable successful experience in the field.
Tight control of procurement specifications, verification procedures, subsystem cleanliness requirements, vehicle-to-ground interface filter requirements, and the requirements for verifying a filter’s design and construction integrity, to name a few, were necessary due to the shuttle system’s complexity. The final document not only defined requirements to help keep the very complex shuttle system free from fluid contaminants, it also established a common language to help avoid misunderstandings since every NASA center has its own unique terminology. Identifying terms such as bubble point—the minimum gas pressure (in inches of water) required to overcome surface tension at a filter’s interface when it is submerged—and silting—an accumulation of minute particles sufficient to interfere with sample analysis—helped prevent misunderstandings among the team.
The shuttle Space Transportation System required fifty-four fluids in total, and each flight required servicing for twenty-seven of them located within sixteen system groups, which had between them fifty-six subsystems needing fluid service. The magnitude of managing the procurement and use of all these fluids was much greater than the Jupiter vehicle system. Why were so many different fluids required? First of all, the shuttle system was especially complex because it had broad applications. Also, flight systems are traditionally designed with a stove-pipe mentality: each subsystem is optimized on its own for a minimum dry weight without regard to the total vehicle system.
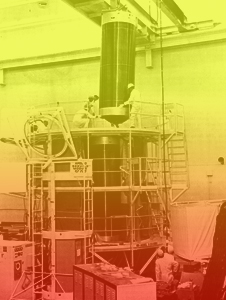
The Apollo 11 service propulsion subsystem (SPS) fuel tank being installed at North American. The SPS included two helium tanks, two helium pressurizing valves, two dual-pressure regulator assemblies, two dual-check valve assemblies, two pressure-relief valves, and two heat exchangers. The helium provided pressurization of both the fuel and oxidizer tanks.
Photo Credit: NASA
The fluid management approach to the shuttle program was very effective, but when a program requires a large number of fluids, recurring operations costs will also be large. Unique subsystems drive the requirements for many labor-intensive operations, reducing the productivity of the flight system by increasing ground-servicing time, which also increases cost. In addition to this direct cost impact, the logistical relationship among fluid management, flight hardware, and ground-servicing hardware grows increasingly complex.
For comparison, the Constellation program’s expendable cargo launch vehicle, designed for fewer capabilities than shuttle, had sixteen systems identified for fluid servicing, including thirty-seven subsystems that needed fluid service every flight. During the program’s preliminary design review, there were fifteen different fluids identified for servicing and twenty-two fluids that required procurement-and-use control. Many of these systems were not fully defined at this phase of the program, so the list of fluids was expected to grow.
The Ares I design team did take fluid control into consideration, planning for the booster thrust-vector control and reaction control systems (RCS), as well as the upper-stage RCS, to use a common hydrazine fluid. The fluid choice ended up being very toxic, unfortunately, but at least it was only one fluid for several propulsion functions.
Often in designing and developing these systems, the focus is on performance, optimizing each subsystem independently without regard to the integrated system. If we continue to focus only on performance, we should not expect anything different in terms of the product’s affordability. If we want an affordable solution, we must change our development process.
As we ready ourselves for the next leap in spaceflight, bold leadership can empower personnel to design for affordability and sustainability—as well as innovatively.
At present, a commercial launch-vehicle supplier has provided an example of integrating common functions on a vehicle, which reduces flight-to-ground interfaces as well as overall flight and ground hardware. The vehicle stores cold helium gas on the vehicle itself, which provides flight pressurization for both the fuel and liquid-oxygen tanks. The only flight-to-ground interface required would be for filling the cold helium bottles on the vehicle. This system provides prepressurization for the fuel and liquid-oxygen tanks as the bottles are refilled during the final phase of preflight. The NASA cargo launch vehicle also used cold helium gas to pressurize the liquid-oxygen tank during flight, but it required an additional interface to provide pre-pressurization to each of the liquid-oxygen and fuel tanks. The commercial vehicle’s approach would provide considerable savings in the recurring cost of spaceflight.
With a national policy directive advising NASA to focus on improving and achieving affordability and sustainability, minimizing the total number of fluids required for launch would be one way to create substantial savings. To help achieve these savings, fluid control and servicing should be integrated into design considerations earlier on—and across an entire system, not just individual elements. Concept development should consider life-cycle cost and not just minimum dry weight. If weight removal is needed to meet performance objectives after the design architecture has been selected, designers could look at manufacturing processes or material selection for reduced dry-weight solutions. Integrating major functions could also help reduce the number of flight-to-ground interfaces that require fluid servicing for every flight, further reducing costs.
As we ready ourselves for the next leap in spaceflight, bold leadership can empower personnel to design for affordability and sustainability—as well as innovatively. Including integration design and fluid management is just one way to help achieve these objectives and make future spaceflight more affordable for government and industry alike.
About the Author
![]() |
Russel Rhodes has been employed for more than fifty years at Kennedy Space Center. During this time, he has been engaged in the design, development, testing, and operation of ballistic missiles and space transportation systems, and has specialized experience in space vehicle propellant loading, cryogenic, hydraulics, high-pressure gases, and other propulsion systems. |
More Articles by Russel Rhodes
- Explosive Lessons in Hydrogen Safety (ASK 41)
- + View More Articles