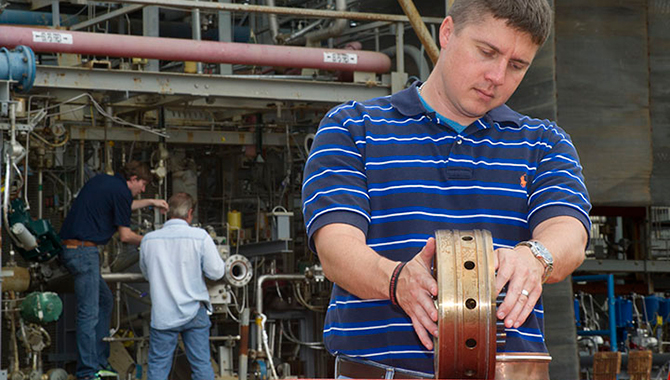
Hurdles remain for next-generation manufacturing techniques such as three-dimensional (3D) printing before they go mainstream.
The National Research Council recently released the results of a workshop held in December 2012 on the advancement of three burgeoning manufacturing processes: additive manufacturing, electromagnetic field manipulation of materials, and design of materials.
Additive manufacturing—or 3D printing, as it is more commonly known—is a discipline of particular interest to NASA and the aerospace industry. Recent tests of a 3D printed rocket engine parts at NASA facilities in July and August of this year support the notion that additive manufacturing technology provides tremendous opportunities to develop and test prototypes quickly and at low cost. This technique also has applications to fields outside aerospace, including medicine, architecture, and automotive manufacturing.
The report identified the need for improvements in the qualification and certification processes for additive manufacturing, the development of new “printable” materials such as metals and ceramics, and better defined standards among the community, especially in the creation of a common terminology. Other topics such as the legal ramifications of 3D printing were also discussed.
The committee also explored the use of electromagnetic fields to manipulate materials (i.e., alter the mechanical or functional properties of a material) and the application of computational and analytic methods to design desired materials such as high-performance steel.
The workshop was convened at the request of the Department of Defense (DOD) to increase the awareness of science and technology efforts currently taking place in these areas, and also to promote coordination among DOD services, components, and agencies.
Propulsion systems engineer Greg Barnett prepares a rocket injector for a hot fire test at NASA’s Marshall Space Flight Center.
Featured Photo Credit: NASA/MSFC/Emmett Given