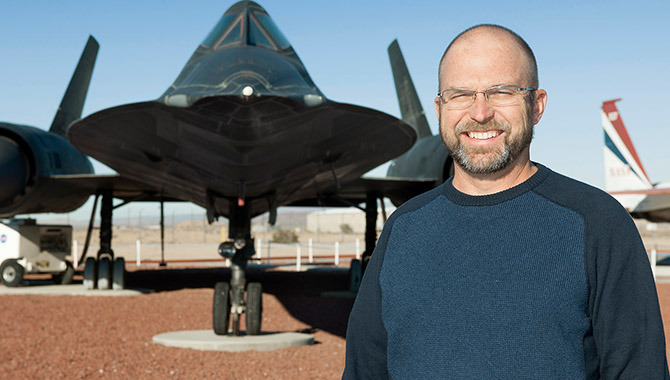
AFRC CKO Bradford Neal standing in front of the SR-71.
Photo Credit: NASA
Bradford Neal discusses knowledge sharing at NASA’s Armstrong Flight Research Center.
Disclaimer: This material is being kept online for historical purposes. Though accurate at the time of publication, it is no longer being updated. The page may contain outdated information or broken links. Current Knowledge Community Corner articles are available here.
Bradford Neal serves as the Chief Knowledge Officer (CKO) at NASA’s Armstrong Flight Research Center (AFRC). Neal is the center’s Chief Engineer and provides independent technical guidance and oversight to Armstrong flight projects to ensure conformance with agency and center standards, policies and processes. In addition, as Chair of the Airworthiness and Flight Safety Review Board, he is responsible for determining and providing the appropriate level of independent technical review for each project prior to flight.
Neal served as an Operations Engineer at NASA Armstrong for more than 20 years, specializing in the integration, test and operations of flight research vehicles and experiments, including the X-31 Enhanced Fighter Maneuverability Demonstrator, Hyper-X / X-43A Hypersonic Research Vehicle, the Stratospheric Observatory for Infrared Astronomy (SOFIA), and the Linear Aerospike SR-71 Experiment (LASRE).
How does your organization share knowledge?
A lot of the knowledge transfer at Armstrong takes place through human interaction. We try to promote the interaction of less experienced folks with more senior folks through work assignments and our internal review processes. We also hold occasional lunchtime seminars and colloquia to cover topics that we feel are of interest to the broader community.
Organizationally, the center’s Research Operations Branch holds the knowledge management activity, internal to Armstrong, for managing, maintaining and distributing our research flight data and associated project records. Also, the center’s Chief Engineer and Office of Safety and Mission Assurance are responsible to collect and disseminate lessons learned — good or bad — that might be helpful to future projects.
We also encourage folks to write technical reports, and support — as much as we can — attending and making presentations at technical conferences and symposia.
Do you have any success stories of how human interaction has improved knowledge sharing at Armstrong?
In years past, we had a Center Director that believed it was important for us to develop a video — X-31: Breaking The Chain — to document the lessons learned from an aircraft accident we had here. It’s been over 20 years since that accident occurred, but some people directly involved with it still work at the center. Being able to play the video and then have a panel discussion or opportunity to talk with those individuals about what they were thinking and seeing at the time has provided great opportunities to learn. It’s been helpful in stimulating conversations and getting people engaged with what has been done in the past that affects how we think and do business today.
Another approach has been to host brown bag lunchtime presentations. These provide an informal forum for senior researchers and engineers to share their knowledge of specific topics with anyone at the center who is interested.
What do you see as the biggest challenge to knowledge sharing that has impacted your organization?
One of the biggest is allowing people the opportunity to slow down long enough to think about what knowledge they have collected, and then how they are going to capture and present that in ways that are easily communicated. We’re so busy that as soon as we’re done with one thing, it’s on to the next. The challenge is to have the discipline to say, ‘Hold it. Stop for a day, a week or whatever it takes to actually collect that knowledge and catalog it in a way that can be passed along.’
A related challenge is having the resource capacity or headroom and flexibility at the center to assign newer employees to work alongside journeymen or senior employees to learn the “tribal knowledge.” That type of knowledge isn’t necessarily all bad and gaining it by working closely with a more senior person, in my experience, is a great way to learn and apply what they know. The important knowledge that used to get passed this way now has to be more formally documented and communicated. It’s become incumbent on the newer employee to actually search for and find that knowledge.
Is there a specific project or set of lessons learned that influences your approach to solving problems?
I’ve had the good fortune to work on several different flight research projects over my career. Thinking back, each has left me with at least one lesson that I still apply today. As a young operations engineer I’d have to say that the most impactful project was the Linear Aerospike SR-71 Experiment. Although in my opinion LASRE was less than fully successful, I learned a lot of lessons about organizational and team dynamics, communication, the importance of commonly agreed upon objectives and requirements, the need to define mission success, and how not to put together LOX and hydrogen high pressure fluid systems. The lessons learned from these challenges certainly influenced my and other team members’ approach to project structure and system design that we applied to later projects such as X-43 and SOFIA.
In my role as the Armstrong Chief Engineer, I believe that learning the why behind the way we do things here at the center has influenced my decision-making and problem-solving. Many of the processes that we use to conduct work at the center were put in place by a generation of folks who lived a much different set of experiences. Again, I have had the good fortune to work alongside folks who experienced personally the X-15 and lifting body programs — programs that took place 10 to 20 years before I began working here. We have processes and procedures at the center — still in place today — that were established because of accidents or incidents that took place on those vehicles. It was very helpful to me as a young engineer to have people who had lived those experiences sit down with me and say, ‘Hey, this is why we do those things. You don’t have to do it exactly this way, but these are the high-level points you need to think about as you write procedures and conduct tests — before you go and accomplish an activity.’ Understanding the rationale — why they have done things a certain way — has been helpful in allowing me to do things well; I hope better than I would have if left to my own devices.
I have certainly learned from personal experience, both others’ and my own. For me personally, the “failures” remain with me more than the “successes.” The things from activities that didn’t go quite the way they should have or the way we thought they ought to, sometimes ending with spectacular results, are things that I apply daily as Chief Engineer when evaluating the work of projects that we’re doing now.
What misunderstandings do people have about knowledge?
One is that people often don’t view it as a commodity to be leveraged and used as a resource like so many others to enable efficient and successful project execution. Another is getting people to understand that knowledge isn’t just a library somewhere, but that people hold and carry knowledge around with them that never gets documented anywhere. The misunderstanding here is that the best or only place you can go to find information is a database, library or some other document repository.
What are some highly technical organizations that have aggressively ensured that workforce knowledge is being captured from across organizations and industries?
From the standpoint of a professional organization looking at aeronautics research, operations and flight test, I believe the Society of Experimental Test Pilots, Society of Flight Test Engineers and American Institute of Aeronautics and Astronautics (AIAA) all see this as important, and work hard to capture and communicate knowledge. The Federal Aviation Administration also has developed web-based information from accident reports and is cataloging them by common causes to help communicate the lessons learned.