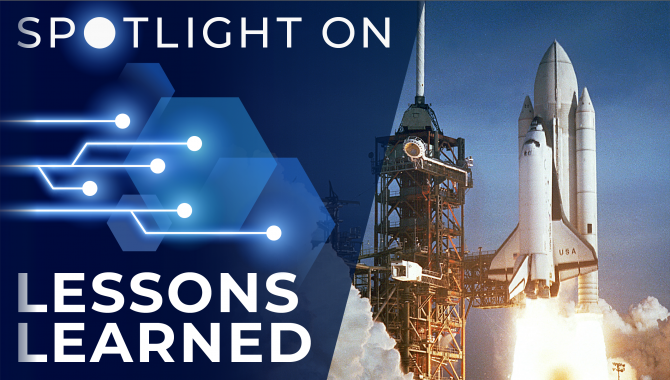
After math solutions left question marks in the aftermath of the Space Shuttle Columbia accident, the Space Shuttle Program faced challenges due to the complexity of analyzing foam and system behavior.
Multiple factors made assessing the root cause of any particular debris event very difficult, and sometimes impossible. In the absence of predictive math models, a process had to be developed for justifying certification to fly.
Prior to the 2003 Columbia accident caused by a two-pound chunk of foam from the External Tank striking the orbiter’s left wing, ice had been considered the most likely and potentially destructive source of debris. Foam was generally thought of as familiar and uncomplicated.
Following the Columbia tragedy, the space shuttle fleet was grounded for two and a half years to determine the root cause of the incident and implement the necessary design changes. On the Return to Flight (RTF) mission in July 2005, the External Tank shed foam from numerous locations and the largest piece was 25 times greater than the certified limit. The shuttle fleet was grounded again and two separate investigation teams were established to determine the root cause of each piece of debris and make recommendations for the second post-Columbia RTF mission.
This lesson learned and accompanying case study illustrate the development of inspection, repair and process changes to minimize the foam debris risk during shuttle launches. The case study challenges the reader to consider programmatic and technical issues in decision-making on complex systems.
Lesson Number: 17903
Lesson Date: September 10, 2015
Submitting Organization: Marshall Space Flight Center
HIGHLIGHTS
LESSONS LEARNED
- Foam is not simple. It is not easily modeled, and predictions regarding the size, location and trajectory of foam liberation from such a cryogenic tank are not computationally calculable.
- Hardware that appears to be simple – a tank of propellant – can entail complications not anticipated before observance in flight.
- Flying on risk is common and requires other controls to mitigate hazards other than mathematical predictions and analytical models.
RECOMMENDATIONS
- Get hardware back from flight when and if possible.
- Take and evaluate imagery from each launch when possible.
- Consult engineers who work with the material and processing closely prior to deciding to launch, especially in return-to-flight circumstances.
CASE STUDY QUESTIONS
- You make the call: Use-As-Built or Remove-and-Replace?
- If you can’t predict the behavior of the material using math models to justify why you think it is safe to fly, what do you base your decision on?
Consult the lesson learned and case study for complete lists.
Marshall Space Flight Center Chief Knowledge Integrator Jennifer Stevens on the importance of this lesson learned:
This case study chronicles the development of flight rationale for the two return-to-flight decisions after the loss of the Space Shuttle Columbia. The case study illustrates the difficulty of creating predictive models of seemingly common materials and ensuring flight safety when process control is the predominant form of risk mitigation. At 20 pages long, the case study provides sufficient background to illustrate the issue at several decision levels and explains the challenges that others might face when generating valid flight rationale. This case study has been used multiple times in organizational and leadership training. An addendum is attached that documents the actual risk assessment used for the decision making.
Spotlight on Lessons Learned is a monthly series of articles that feature a valuable lesson along with perspective from NASA’s knowledge management community on why the lesson is important. The full lessons are publicly available in NASA’s Lessons Learned Information System (LLIS).
If you have a favorite NASA lesson learned that belongs in the spotlight, please contact us and be sure to include the LLIS Lesson Number.