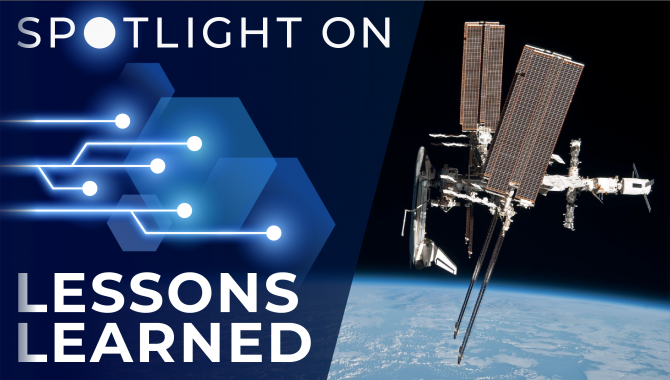
Realizing each team member had to become familiar with each discipline’s processes in order to increase productivity for the entire team is one of the key lessons learned from the disposition of International Space Station hardware when the Space Shuttle Program ended.
Over 30,000 International Space Station (ISS) items were either excessed, retained, returned to support other programs, or transferred to the government when the shuttle era ended. The ISS Hardware Disposition Project lasted almost two years and resulted in the disposition of almost 1,000 Program Model Numbers (PMN)/Systems – 10 percent higher than the planned baseline.
A strong relationship with NASA partners along with early inclusion of stakeholders facilitated timely disposition processing, including reduced screening times. An Integrated Disposition Team, consisting of the Checkout, Assembly and Payload Processing Services (CAPPS) contractor and its subcontractors along with NASA Kennedy Space Center personnel from various disciplines, was formed to manage and implement the post-shuttle disposition activities for identified ISS hardware.
Dispositioned systems included downgraded flight hardware, major ground support equipment, processing equipment, special test equipment, facility subsystems such as cranes and doors, and work platforms and stands.
Lesson Number: 7136
Lesson Date: December 1, 2012
Submitting Organization: Kennedy Space Center
HIGHLIGHTS
LESSONS LEARNED
- It was important to pursue and implement Lean/Accelerated Improvement workshops to develop tools and processes that create a high performance team. Each team member had to become familiar with each discipline’s processes in order to increase productivity for the entire team.
- Continual, early coordination with the appropriate program and configuration management personnel was paramount to ensure timely release of Change Revision documentation.
- The team realized that flexibility was mandated and changes were inevitable throughout the life of the project as additional PMNs/Systems were added for disposition and process sequences changed.
RECOMMENDATIONS
- Pursue the early identification of items that may be environmental hazards and ensure they are properly identified on the schedule.
- The disposition team leader should form a Work in Progress Board to allow for efficient data tracking and successful management and oversight of the project during day-to-day operations.
Consult the lesson learned for complete lists.
Kennedy Space Center CKO Michael Bell on the importance of this lesson learned:
This lesson spotlights what can happen with cooperation and teamwork between contractors and subcontractors along with NASA personnel from various disciplines. It also illustrates the implementation of Lean Improvement workshop tools and processes at NASA.
Spotlight on Lessons Learned is a monthly series of articles that feature a valuable lesson along with perspective from NASA’s knowledge management community on why the lesson is important. The full lessons are publicly available in NASA’s Lessons Learned Information System (LLIS).
If you have a favorite NASA lesson learned that belongs in the spotlight, please contact us and be sure to include the LLIS Lesson Number.