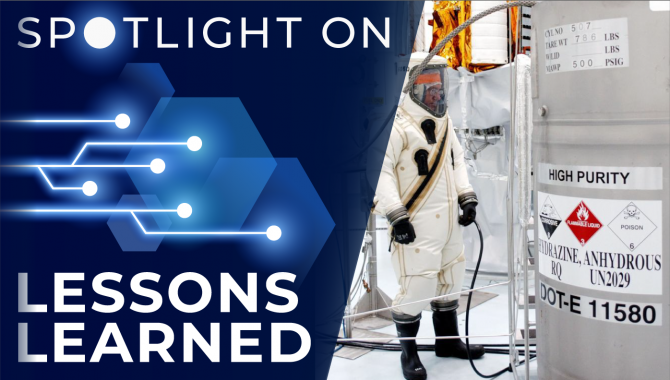
Best practices for conducting high-purity hydrazine elemental analysis processes must be followed to avoid sample contamination that could impact space missions.
Trace contaminants in high-purity hydrazine (HPH) propellant impact a wide variety of NASA, Department of Defense, and commercial missions. Depending on thruster design, contaminants must be kept at extremely low levels, which are verified by routine analysis. Several impactful contaminants are not currently controlled in the MIL-PRF-26356 specification that governs procurement.
A recent assessment of some of these elemental contaminants sheds light on potential contaminants present following changes in the HPH supply chain. A round robin analysis using four separate laboratories resulted in unacceptably high variability in the quantification of the contaminants.
Efforts were made to ascertain the causes of this lab-to-lab variability and highlighted several sample preparation and analytical method considerations that can impact laboratory results. The principal objective of this lesson learned and the accompanying recommendations is to establish an analysis methodology that yields accurate and repeatable quantification by providing best practices for both quantitation methodology and strategies for avoiding sample contamination during analysis.
Lesson Number: 29801
Lesson Date: December 14, 2020
Submitting Organization: NASA Engineering and Safety Center
HIGHLIGHTS
LESSONS LEARNED
- Analysis of single batch-sourced samples of hydrazine hydrate (HH) from four laboratories showed an unexpectedly wide variation in elemental assay results.
- In some cases, large discrepancies were determined to have been caused by differences in analytical procedures and methods at the laboratories.
- Refinement of analytical methodology for HPH, HH or other hydrazine derivative sample handling and processing as well as the instrumental analysis methodology for extended elemental content is essential to gaining accurate and equivalent results from multiple laboratories performing this type of analysis.
RECOMMENDATIONS
- Glassware usage should be minimized in all steps of the analytical process to minimize sample contamination.
- When using platinum evaporation dishes, adequate cleaning between samples should be ensured.
- Method detection and reporting limits should be established for all elements in analysis for proper reporting of trace elemental levels.
Consult the lesson learned for complete lists.
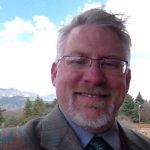
Charles Pierce
Credit: NASA
NASA Deputy Technical Fellow for Propulsion Charles Pierce on the importance of this lesson learned:
In 2018, the process for producing high-purity hydrazine (HPH), the monopropellant used as the engine fuel for the vast majority of U.S. spacecraft, was changed. The legacy process for producing high-purity hydrazine used for U.S. spaceflight application is well documented as using a Raschig method. The old and new processes use different feedstock compounds and produce different biproduct chemical residues and assays. Well prior to the production change, there were discussions including the user community that a possible modification of the process was being investigated. However, communication of the actual implementation of the change in 2018 was not well distributed, catching much of the spacecraft propulsion community off guard. The new process — with additional unknown contaminants — brought into question the validity of the qualification of all existing thrusters which may use the new propellant.
HPH used for spaceflight programs has long been purchased under the specification MIL-PRF-26536 (and its predecessors) with requirements developed for the legacy Raschig process. The specification severely lacks requirements or limitations on any particular production processes. Further, as time has progressed, additional requirements above and beyond the specification have been requested by programs with specific technical requirements. For years, this was largely managed within the supply chain with no level of standardization. In early 2020, there was a meeting of users with DLA Energy in attendance. Concerns were voiced regarding the completeness of the specification to adequately capture regulation of contaminants of interest. It was agreed that a comprehensive chemical analysis of product should be performed to inform future specification modifications.
Several working groups were established, and several analytical studies were initiated to address the change in production method. A main objective of the study was to understand contaminants present in the new hydrazine and the quantity of those contaminants, and to assess risks to current HPH-thruster systems as well as inform possible updates to a future revision of the MIL-PRF specification. One of the early observations of this study was that most chemical analysis laboratories, both within NASA and the private sector, use different methods for assessing assay contaminants and, not surprisingly, the quantities of contaminants ranged widely between laboratories when analyzing a sample from the same batch for propellant.
By understanding that there is a level of standardization of chemical analysis methods for assessing the purity of HPH, propulsion engineers can have confidence in the accuracy of lab results and will be better able to assure that spacecraft thrusters can provide the expected thrust, life and efficiency performance that are required by the host spacecraft. This lesson learned is especially valuable in that it recognizes that there are often multiple processes and methods to assess the purity of a propellant sample; establishes important guidelines and best practices to minimize the introduction of new contaminants into a propellant sample; and reduces the amount of variability between a variety of chemical analysis methods. Lessons learned like this one will allow chemical analysts in different laboratories to have a level of standardization in the methods and procedures for analyzing rocket propellant, thus allowing multiple laboratories to be used for a chemical analysis with minimal concern of widely varying results and providing propulsion engineers a higher level of confidence in the reported chemical analysis results.
Spotlight on Lessons Learned is a monthly series of articles featuring a valuable lesson along with perspective from a NASA technical expert on why the lesson is important. The full lessons are publicly available in NASA’s Lessons Learned Information System (LLIS).
If you have a favorite NASA lesson learned that belongs in the spotlight, please contact us and be sure to include the LLIS Lesson Number.