NASA Marshall Space Flight Center Engineering Technicians John Hood, Amy Meekham, and Mark Sloan discuss details of their work on the Imaging X-ray Polarimetry Explorer.
A joint effort between NASA and the Italian Space Agency, the Imaging X-ray Polarimetry Explorer (IXPE) is the first space observatory dedicated to studying the polarization of X-rays coming from objects like exploded stars and black holes. Polarization describes how the X-ray light is oriented as it travels through space.
Launched in December 2021, IXPE carries three identical telescopes. Each telescope includes a set of cylindrical mirrors, or optics, and a sensitive detector. The mirrors collect X-rays from celestial objects and focus them onto the detectors, which make an image of the incoming X-rays and measure the polarization. All three mirror sets are separated from their corresponding detectors by a deployable 12-foot (3.7-meter) boom.
In this episode of Small Steps, Giant Leaps, you’ll learn about:
- Intricate details and incredible precision required to build IXPE
- Technicians’ responses to the pressure of machining, polishing, and replicating IXPE components
- Helpful lessons learned for early career technicians
Related Resources
Imaging X-ray Polarimetry Explorer (IXPE)
IXPE: Expanding the X-ray View of the Universe
Assembly of the IXPE Mirror Modules
Historic Nebula Seen Like Never Before With NASA’s IXPE
NASA’s IXPE Fires Up Astronomers With New Blazar Findings
APPEL Courses:
Creativity and Innovation (APPEL-vC&I)
Communicating Technical Issues (APPEL-vCTI)
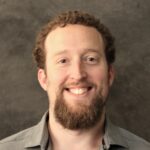
John Hood
Photo Credit: NASA
John Hood is an Engineering Technician with Jacobs and the Jacobs Space Exploration Group at NASA’s Marshall Space Flight Center. Hood currently supports Marshall as a materials technician, working on the formulation of rubber insulation compounds that are used in applications, including solid rocket motors. He has 14 years of experience in aerospace, manufacturing, and chemical industries. As an optics technician supporting the Imaging X-ray Polarimeter Explorer (IXPE) Project, his major contributions included replication of the X-ray optics by performing electroplating, electrochemical cleaning, and passivation. Hood has an associate degree in applied science in mechanical engineering from Snead State Community College.
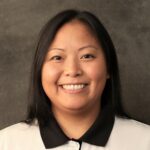
Amy Meekham
Photo Credit: NASA
Amy Meekham is an Engineering Technician with ERC and the Jacobs Space Exploration Group at NASA’s Marshall Space Flight Center. Meekham currently supports various optics projects by both polishing and assisting in the replication of the X-ray optics. As an optics technician supporting the Imaging X-ray Polarimeter Explorer (IXPE) Project, she super-polished the mandrels used to create the X-ray optics with precise prescriptions. Meekham is a Navy veteran who served as an aviation structural mechanic performing maintenance on E-2/C-2 and F-18 E/F aircraft.
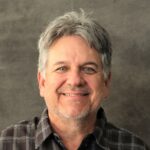
Mark Sloan
Photo Credit: NASA
Mark Sloan is an Engineering Technician with ERC and the Jacobs Space Exploration Group at NASA’s Marshall Space Flight Center, where he provides precision manual machining services. Sloan currently leverages his 45 years of machining experience, including 30 years at Marshall, to support science and technical personnel at the National Space Sciences and Technology Center in the fabrication of parts and components for various experiments, projects, and programs. His experience extends to other unique NASA projects, including a full-scale mockup of the Hubble Space Telescope for use in the Neutral Buoyancy Tank; Crystal Growth Furnace hardware used for International Space Station (ISS) research; and ISS Water Recovery System flight hardware for the Environmental Control and Life Support System. Sloan served as a senior machinist on the Imaging X-ray Polarimeter Explorer (IXPE) Project, responding to a wide range of hardware requests to support optics development and environmental testing.
Transcript
Pam Melroy: It’s not just rocket propellant that launches spacecraft. It’s people.
I’m NASA Deputy Administrator Pam Melroy.
NASA has one of the brightest, most dedicated workforces in the world, including the highly skilled technicians who develop and test our components and then assemble them into a space mission. Our work is exciting, using cutting edge manufacturing technologies that in some cases we’re pioneering.
As this podcast series concludes, I’m excited to hear stories from our talented trade and technical professionals who made essential contributions to the successful IXPE mission and learn more about the intricate details of their work.
Deana Nunley (Host): Welcome to Small Steps, Giant Leaps, a NASA APPEL Knowledge Services podcast where we tap into project experiences to share best practices, lessons learned and novel ideas.
I’m Deana Nunley.
The Imaging X-ray Polarimetry Explorer, or IXPE, is NASA’s first mission to study the polarization of X-rays from many different types of celestial objects. Launched in December 2021, IXPE is a space observatory built to discover secrets of some of the most extreme objects in the universe. Each of the observatory’s three identical telescopes includes a set of cylindrical mirrors that collect X-rays from celestial objects and focus them on sensitive detectors.
The highly successful mission is an international collaboration between NASA and the Italian Space Agency. Hundreds of engineers, scientists, and technicians from more than a dozen countries worked together to make IXPE a reality.
Today as we wrap up the NASA Trade and Technical Professionals series, we’re talking with three of those technicians who work at NASA’s Marshall Space Flight Center and supported areas that were essential for the success of the IXPE mission.
Mark Sloan: Hey, I’m Mark Sloan. I’m an Engineering Technician, Manual Machinist. I’ve been a NASA contractor now, for almost 30 years with Jacobs Space Exploration Group. That is the prime contractor, and I’m with ERC-Oasis now. And my role in this IXPE project was to assist with any ground support equipment as far as vibration, testing, calibration, any kind of fixture or anything that may need to be built to hold an instrument, maybe put in a vacuum chamber or help them hold another piece, so where they can lift something up or maybe get something out, or just whatever needed to be done at a moment’s notice. I was an on-call machinist.
This was very important, because of IXPE and NASA, everybody always works on a timeline and a budget. When things get delayed, if they have to wait a week to get a part, or two weeks to get a part, or maybe get a set of drawings out to somebody, they didn’t have to do that with me. They knew that they could count on their in-house technician to take the bull by the horns, to say, and just go get done what needed to be done.
Amy Meekham: Hello, my name is Amy Meekham. I’m with Jacobs Space Exploration Group. I am also currently working with ERC-Oasis. I helped out with the polishing on 24 mandrels. And what made this important is that we were able to get a good high-quality surface that met the requirements needed for the job.
John Hood: I’m John Hood and I work for Jacobs Space Exploration Group as an Engineering Technician. My work on IXPE involved electroplating replicant shells from our polished mandrels. This was important because the inside of the replicant shells that we separated from the mandrels were the X-ray telescope mirrors.
Host: Thank you all for joining us today on the podcast and giving us a summary of your role with IXPE. Let’s dive deeper into the details of how you contributed to this successful mission. Mark, let’s start with you.
Sloan: We try to keep our customer happy, and when they actually come to you and needing something, you can always sense an urgency or a, ‘Mark, we need to handle this. This is going to hold up if we don’t get this’ or ‘This is what we need and we’re going to rely on you to bring us through this little process here where we’re needing you. And we know that you can handle it.’ And they do, they always compliment and are very appreciative of the work that we do, whether it’s coming up with something off the top of my head or maybe even something that’s put down on a piece of paper. And just getting those guys back up and running if they have a problem, that’s kind of been my role throughout the whole process of IXPE.
When we first started trying to figure out how to hold these mirrors, they were having problem with the glue, with it holding or the glue was turning loose during the vibration test. And they actually came to me and I made some rings for them to actually hold the mirror in place while they glued it. I guess it was probably an engineering development unit that they had to run everything through before they actually did the flight piece. So they did have problems there for several months I know, and there was a lot of different iterations of the mixture. I’m not sure if it was because they were putting too much vibration or if it was in the vacuum chamber. I’m not sure exactly what was causing the glue to fail. Maybe John, I don’t know if you could speak to that.
Hood: I’m the same. I don’t exactly know what caused it to fail, but I know it was a nightmare.
Sloan: Yeah, that was a big ordeal there for a while. And they finally came up with a right glue, maybe it was from a different company. I’m not sure if some of the chemicals were out of date they were getting from a vendor, but we did manage to work through that problem and it came out on the good side.
Host: That’s good. Amy?
Meekham: So, starting off with the polishing, we got it from diamond turning, which is a really rough surface about 600 angstrom, and then we will keep polishing it out, until we got into a really fine, shiny surface of about five angstroms. And then after we got it done with polishing, we would have to actually go into the next step of getting it final cleaned before it went to replication.
Sloan: Amy, can you talk a little bit about the polishing on the machine and maybe the slurry that you had mixed up to go in while the machine was running, and maybe the contact that was made on the mirrors to help polish it? Is that something we want to talk about?
Meekham: So, the first compound that we used to polish was the 1.0 micron Baikalox. And we started off with that, and once we got it down to the smoother roughness, and then we kept moving down from the 1.0 to the 0.3, the 0.05, and then after that we would start with the super polishing, which would be the COMPAL 180 or 120, and then after that would be glaze-ox and that would get us to the nice clean shiny surface of five inch trim and below. And we would have to keep on keeping the surface of the mandrel constantly wet with the compound just to make sure it doesn’t dry out and if it does, it’ll scratch up the surface pretty bad. So we were constantly in the tent and we actually made sure we had humidity in there also to make sure that the surface didn’t dry up.
Sloan: Inside that tent is the machine where you did your polishing, Amy, and I didn’t realize you were having to keep that at a certain humidity in there, but I guess probably the temperature and the humidity had to be controlled in order to come up with that fine of the high polish on that, I imagine. Is that correct?
Meekham: Yeah, we kept it at 80 percent to about 90 percent humidity and the temperature in the tent would be about 70.
Host: What did you wear as you were doing this kind of work?
Meekham: We just wore regular clothes and then maybe just a lab coat and then goggles and gloves.
Host: And were you really hot?
Meekham: Some days it was pretty warm in there, but eventually I got used to it.
Hood: I will tell you, at the beginning of the IXPE stages when I got hired in, I was helping Mark with the polishing and I’m very hot-natured. So yes, it was hot to me and it was very humid, especially after being out in the Alabama heat and humidity anyways.
Sloan: Didn’t we start out when we first started polishing those things, when we had the machine, it was this black rubber stuff and then we had, I don’t know if some grooves or channels or something, I guess for the compound to work in between it and the diameters of those where that radius on those polishing things were similar to the diameter of the actual mirror, wasn’t it?
Hood: Yeah, that was the polishing laps.
Sloan: I remember working on some of those laps in the early stages.
Meekham: Yeah, we used those laps and then further down we actually continued using them for all the different projects, but we actually got them made in-house for the different sizes, but all the laps and the pitch that we use, they actually made the molds for us to pour out the hot pitch before we laid it out onto the actual lap.
Sloan: Oh, OK.
Host: Interesting. John, let’s hear from you as far as details of how you contributed to the mission success.
Hood: So, to start, as a team, we were tasked with making 96 X-ray telescope mirrors for IXPE. IXPE had four mirror modules and each module had 24 replicate shells that would go inside of it, and all 24 shells are different diameters, so they could be nested inside the largest shell. We had 24 mandrels made for each size shell we needed to replicate, and we had to be very careful not to damage these mandrels, especially after they had been polished. Damage to the mandrels could take up to six months to fix, so we knew we had to be careful with them, and I think there were a couple that had to be repaired and we did have to wait that long for.
Before IXPE, I had never heard of an angstrom, but we were told they had to be polished to one to five angstroms and I don’t know if everyone else is like me, but that was just a crazy number to me. It’s equal to 100 millionth of a centimeter and used to express interatomic distances. That level of polishing makes for much better than mirror finish.
My day-to-day operations started with our nickel cobalt electro plating bath. We had to constantly monitor and adjust the chemicals and the nickel cobalt anodes in both plating baths. We also had to run tests to make sure there was not too much or too little stress in the metal that would be electroplated.
Once we received a polished mandrel, we would clean it, passivate it, and start assembling it with electroplating hardware. We used a potassium dichromate bath to passivate our mandrels, and with the potassium dichromate, if one drop of that were to get in our plating baths, it would increase the stress in the plating bath by about 1000 PSI. So that contaminant, along with other contaminants, we had to be very careful not to get in the bath, so we had to be very careful with our cleaning processes. Because if we shut down a bath from contaminants, it could take weeks or months to rectify that issue.
Prior to plating, we would calculate our electro plating parameters needed to achieve the desired replicant shell thickness and the electro plating time. Then we would lower the assembled mandrel into the electroplating bath. When that operation was complete, we would lift the mandrel out of the plating bath, clean it and disassemble the plating hardware. Then we’d lower the mandrel with the replicant still attached into a chilled bath, and the difference in thermal expansion of the mandrel and the replicant shell allowed the mandrel to contract quicker than the shell, so the shell would separate and fall into a catch plate we had in that chilled bath. So they were very thin shells and to handle them with your hands could deform them. Then we could remove everything from the chilled bath, clean and dry the shell, and inspect the inside of the shell to make sure it could be used as an X-ray telescope mirror. Each mirror module had 24 nested shells and we had to make enough for four modules, and we were successful in doing so.
Sloan: John, when you were making these shells and you got done, where did you place the shells when you moved on from that one finished and put them into another one? Did we have a bunch of five-gallon buckets or was it something that — I can’t remember where you stored those, the actual shelves?
Hood: So we had the catch plates made to where they could fit a five-gallon bucket on either side to keep dust and contaminants out, and then we would close those up and we had a clean tent set up in our electroplating shop that would control humidity and dust particles, so that we could wait for inspection from Quality to make sure that the shells passed all the requirements needed to be able to put a flight tag on them.
Sloan: I think I remember working on some of those five-gallon buckets. There was something that went on the top of one and all these things kind of hooked together. Now that you bring it up, I remember out of some PVC something or another that we made for those mirrors to slide down in and it set in that bucket.
Hood: I can’t remember what the catch plates were made out of, but they had to have the same thermal expansion rate as the shells so that they wouldn’t cramp the shell in the cold bath.
Sloan: There was a lot of stuff that went on down in that plating area that I’d build some stuff and make things and send to them, and I didn’t know exactly what I was working on and there were some — I made a bunch of molds for the gaskets that I think the gaskets actually kept the mirrors separated. Is that what those gaskets were for?
Hood: That’s a good point. So there were three sections to each mandrel and the middle section was the optic section, and then each end had a section that we could plate a piece of shell on either side, so when we separated everything, we could check the stress on those end rings and not have to mess with the optic section. So those gaskets went in between each section and we actually made all those gaskets in-house ourselves.
Sloan: Those molds, they were pretty close tolerances on those molds and there was like, I don’t know how many different ones. It must’ve been 20 or 30 different molds. Or you could take a piece and put it together and maybe take that one out, maybe put another piece, maybe use the same base or something. But I think Amy, did you work on injecting that material in those molds to help make those gaskets? Was that part of the process you were doing at one time?
Meekham: I didn’t do it on IXPE, but I did it on future projects.
Sloan: Oh, OK.
Hood: I think I made all the gaskets for IXPE, and there were a bunch of molds. Each end of the mandrels were different sizes, so you had 48 different sizes and I think we were able to use a few of the bottom sizes for the next big size, but there probably were 30 or 40 of those molds that we had to make gaskets for them.
Sloan: Yeah, that was a lot of work just in making the mold part and then I couldn’t imagine you guys making those gaskets and then keeping up with the right size, where it goes, and actually even storing them and keeping them clean, and it was just amazing how you guys kept all that together.
Host: And I’m curious, when you’re working on sophisticated hardware that requires such incredible precision, how do each of you know when your work is good enough?
Sloan: Well, early on, we changed the way that we actually did the spiders that were actually holding into the mirrors. And actually, the mirror was, and if I’m wrong, John, correct me, but I think they were kind of floating in midair and you put that glue around it. But I was making these little grooves around on the lathe for the mirror to sit down in and they were like, I don’t know how many different grooves, 10 or 12 or ever how many, but I had a groove tool that was the right width and you could just feed it in. We had digital readouts and worked with calipers, and check and make sure. We had some tight tolerances on that, but it was nothing like done in the angstroms what Amy and John was talking about, but my precision level was probably within a couple thousands of an inch, and what they were talking about was taking that couple thousandths and dividing that into about 10,000 times. That’s getting down there to a gnat’s hair, I think, or maybe even finer than a gnat’s hair.
But a lot of it was experimental and we get to where that’s going to be right, that’s going to work for us. They usually went with those numbers. Sometimes we had to increase the diameter of that and you’d say, ‘Well, what does it measure?’ We don’t know what it measures because none of them were across from each other. On those spiders, you really couldn’t get a good measurement. They said, ‘Well just touch off and take another two thousandths out of it.’ So, you’d have to touch off and go in like 40, 50 thousandths deep, but you’re just taking a couple thousandths off maybe the inner diameter or the outer diameter for the mirror. But they were looking for that to float in midair so they could get their glue around it, and actually the glue probably was what was holding it. They didn’t want it touching the metal. They just wanted for the glue to be surrounded by the spider and the mirror.
Hood: There was a lot of tedious work that went into that. It was incredible.
Sloan: Yeah.
Host: Amy, I’d love to hear your perspective on this.
Meekham: Well, when we would be doing the super polish on the mandrel, we would run it for about six to 24 hours.
Sloan: Didn’t you go by a machine that would tell you how polished it was? Because you couldn’t really tell, just by feel, how polished it was.
Meekham: Yeah, that’s the interferometer. We would have the knee view interferometer in here. Usually Tom Kessler would be the one measuring it or Charlie Griffin, they would be the one doing the testing on the mandrels for us.
Sloan: And they would tell you when it was good enough then, right?
Meekham: Yeah. But if it wasn’t good enough, then we’d put it back onto the polishing lathe and polish it for another six hours on each end and take it back off the machine and put it back on them on the new view for them to measure. And whenever they say it was good, it was good.
Host: And what was their role with the project?
Meekham: They did the metrology.
Host: And John, how did you know when your work was good enough?
Hood: Before electroplating flight hardware, we would analyze and adjust the chemical composition of the plating baths. We would check that we had plenty of anodes in each plating bath, and we would analyze and adjust the stress levels in each bath before we electroplated flight hardware. But ultimately, we had to trust that each member of the team had the skills required to do their job. By the end, all our flight hardware met the requirements needed to satisfy the project.
Host: What was most rewarding with the IXPE project?
Hood: The most rewarding thing about IXPE to me is that our team helped create a space observatory that is currently in orbit, and that’s something I get to share with my kids that we’ve got something flying in space that I worked on.
Host: That’s really cool.
Sloan: I think the most rewarding for me would be after everything was said and done, we got everything ready and was ready to launch, just seeing it take off and have the successful launch. That was probably the most rewarding for me.
Meekham: Yeah, that’s basically the same for me. Having IXPE launch successfully and was able to take some great images.
Host: What was most challenging?
Hood: It was very challenging to solve some contamination issues, but we all worked together and solved those issues.
Meekham: Yeah, I would agree on that. That was the most challenging part for me too. We had excess silica, and we weren’t able to really figure out where it came from and it was hard getting it cleaned. But we came together and got it cleaned and got everything done.
Sloan: I think holding the diameters on those spiders were the most challenging for me. It was pretty nerve wracking when you had a piece of carbide that was maybe 20 thousandths wide or 40 thousandths wide and you’re trying to go 90 thousandths deep, and you’re hitting each one of these little spiders, one little thin stainless steel and that thing goes dink, dink, dink, dink, dink, dink, dink. Then all of a sudden it was just, you knew what had happened. It wasn’t given that little clink in there and a piece of carbide may break off and there you are, you got to start all over again trying to find another insert to put in there. But that was probably my most challenging part, just putting those face grooves for the spiders.
Host: And how do you handle the pressure of the job when your role is so important?
Hood: I have to trust in my skills and the training I’ve received, but then also I have to make sure when it’s time for me to go home, that I’m home and I’m spending time with my family and friends and enjoying life to take a break from it.
Meekham: The people in my group give me confidence to handle this kind of pressure. If I needed help with something that I didn’t understand, I would go to them and ask them what was the best thing to do and somehow they would always have an answer. So, I think that really helped me out.
Sloan: For me, I really didn’t feel that much under pressure. I don’t know if that comes with years of experience or being a senior machinist. It was just you just got to do what you got to do, and you just take away what you don’t need and leave the rest because what you do need is right next to what you don’t need and you just remove that metal and eventually you’ll get there, but you have to be careful. It’s not really pressure, it’s just doing your job.
Host: What got you to this point career-wise?
Hood: A lot of hard work. I was originally working toward a mechanical and aerospace engineering degree, and that got me into a co-op program that opened several doors for me. While I was going to school, I got to work with some very smart engineers on many research and development projects and that experience and the skill sets I learned led me to this job.
Meekham: I would say being patient, willing to be able to learn all the knowledge from anyone really trying to give it. And also, my mentor is Mark Young. He’s our master optician here. He is the main polisher here and he does a really good job, and I’ve been learning from him for over five years now, and I would say just keep on learning really.
Sloan: The point of my career right now, just 45 years of working in the space industry, from probably 1980 is when I first started working on flight hardware in the early days of some of the launches. I think mine is just being able to just stay focused and paying attention to all the fine details gets you to where you can be the type of technician that you need to be.
Host: Have you learned lessons along the way that might be helpful to early career technicians?
Hood: Even if you do not have the skills that a project requires, try to get involved. Your team will help you and you will gain valuable skills and it’ll mean the world to you.
Meekham: So, joining IXPE, it was my first time ever learning how to polish, so everything was new to me. I was in the Navy before this and I was an aviation mechanic working on environmental and safety equipment, so everything with polishing and being so technical and clean, that was all very different for me. But you definitely have to learn from the older guys that’s been here longer. Learn from them, be humble and definitely take in what they’re teaching you. Be patient and don’t be afraid to take chances to try something new, especially if you never did it before, because all this, five years ago was new to me and I took a chance and I’m still here and I love it.
Sloan: Never be afraid to ask questions.
Host: If you came together at an event to celebrate IXPE mission success, what are some of the stories you’d swap?
Hood: I think we would all like to reflect on Art LaPietra. During the middle of the project, he died in a car crash involving a train. He had been in the group a long time before I came in to work on IXPE, and he was a diamond turning technician. His skills were crucial for preparing the mandrels for polishing operations, and he really helped me understand a lot about what we were trying to accomplish in the earlier stages of IXPE. From what I could tell, he was a really good man and had a loving family. And when we all lost him, it was hard to recover emotionally and technically. But I now work in a different group, so I’d want to know how everyone is doing, and I would also like to hear what projects they’re working on now and share some of the projects I’m working on.
Sloan: Yeah, Art was a great guy. He knew a lot about that diamond turning and some other processes that took place, and he was a key individual in working with the mandrels and machining that diamond turning. There’s not many people around the country that did the type of work that he did, so his skills were very valuable to us. And there were also other people that we worked with in our group also that had passed away in the last, say 10 years. You miss those guys when they’re gone. Some just didn’t come back from a holiday. They found them at home, and then maybe another guy died of cancer and got sick during the early parts of IXPE. So, those guys were missed.
Host: And that’s really tough on a team, when you go through those kinds of sad experiences together. How did you come together and overcome?
Hood: I felt like it kind of drew everybody close together in mourning for him and maybe the others that had passed away before I had come there, but I think it made us focus on what we needed to get done, and I think we just had to take what we had learned from him and then what we could learn from each other to overcome those obstacles.
Host: And you’ve got the sad times and then of course you’ve got the good times. If you try to think of a happy story, maybe even something from all these years on IXPE that makes you laugh, does anything come to mind?
Hood: Turkey Trot. (Laughter) It’s every Thanksgiving. It’s like our department or I guess everybody in that building. All the halls would be decorated, different football teams and everybody’d bring different food items and whole lot of potluck-type meals, and we’d just spend a whole day walking around, chatting with each other, goofing off and eating and just enjoying each other’s company.
Sloan: Yeah, ERC would have a get together sometime down at the river and they’d play different games. Art was known for his bocce ball and we’d play some of that. I think he had a little Italian blood in him there, so I think that’s an Italian game that they played. But just getting together as a team, try to celebrate some milestones and it was always good to get together.
Host: What do you like most about your job as a technician?
Hood: I get to be very hands-on with every project I work on, and they’re all different and always teach me something new, so I’m getting to constantly learn.
Sloan: Just working with all the different skillsets that are out there. From working from the top guy all the way down to the people that may be the custodian. We’re all human beings and we all put our pants on the same way. But just being around folks, sharing life’s experience, talking about your grandkids or talking about maybe a fishing trip, being able to share different stories with people at work. I think it means a lot if you can just not necessarily always be focused on your work, but you got to have some social skills in there too. Just being around other people I think, and you learn from other folks some of their skillset, learn what they do and what they’re working on.
Host: Amy, what do you like most about your job as a technician?
Meekham: I like that I can learn new skills when offered. And like what Mark said, being around other people that like to teach you and lift you up and just being around people who are amazing.
Host: So, this has been really fun. Thank you all so much for joining us on the podcast.
Meekham: Thank you for having us.
Hood: Yeah, thank you.
Sloan: Thanks a bunch.
Host: Any closing thoughts?
Hood: I would like to mention the culture out here. We have a culture of safety, and although it may slow things down sometimes more than it would have in the past, we know that our companies care about us and we get to usually go home without any injuries to our families and well, to enjoy them and come back to work every day knowing that we’re going to be taken care of and that we’ll get to enjoy our work and enjoy the family lifestyle that we have out here where everybody can enjoy each other and get their work done and always be safe.
Host: You’ll find John, Amy, and Mark’s bios and links to topics discussed during our conversation at appel.NASA.gov/podcast along with a show transcript.
Many thanks to NASA Deputy Administrator Pam Melroy for introducing each episode in this podcast series and sharing her personal reflections and appreciation for NASA Trade and Technical Professionals.
As we mentioned, this is the final episode in this three-part series but you can be sure this isn’t the last you’ve heard from technicians on the Small Steps, Giant Leaps podcast. We plan to feature interviews with technicians supporting NASA missions in future episodes in addition to our interviews with engineers, scientists, and project managers.
If you’d like to suggest a guest or topic, please let us know on X at NASA APPEL – that’s app-el — using the hashtag Small Steps, Giant Leaps, or contact us via the APPEL Knowledge Services website.
As always, thanks for listening.