How inflatable habitats moved from concept papers to the International Space Station, and what NASA is doing to eventually put one on the Moon.
In this episode, we explore how NASA’s research has advanced inflatable habitats for space exploration, the key steps engineers and researchers took to bring the technology to where it is today, and the lingering technical challenges left to solve before the Artemis astronauts can seek shelter in one.
You’ll learn about:
- The layers of high-performance materials that make up an inflatable habitat and the purpose each has.
- Why NASA was considering an inflatable habitat for astronauts during the later Apollo missions.
- How the first inflatable module on the International Space Station was inflated and how long it took.
- The dangers inflatable structures face in space.
- The challenge of integrating rigid structures, such as hatches and windows, into inflatable habitats.
Related Resources:
The Bigelow Expandable Activity Module (BEAM)
Review of Habitable Softgoods Inflatable Design, Analysis, Testing, and Potential Space Applications
NASA Begins Testing Habitation Prototypes
Inflatable technology: using flexible materials to make large structures
APPEL Courses:
Foundations of Aerospace at NASA (APPEL-vFOU)
Human Spaceflight and Mission Design (APPEL-vHSMD)
Space Launch and Transportation System (APPEL-vSLTS)
Science Mission & Systems: Design & Operations (APPEL-vSMSDO)
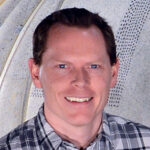
Tom Jones
Photo Credit: NASA
Thomas C. Jones is an expert on inflatable habitats. He worked at NASA Langley Research Center for more than 16 years before moving over to Marshall Space Flight Center in 2023. Tom has performed structural analysis, design, and testing of large, lightweight deployable and erectable space structures and manned inflatable modules. He co-authored NASA’s certification guidelines for crewed inflatable softgoods structures.
Transcript
Matt Kohut (Host): Welcome to Small Steps Giant Leaps, a NASA APPEL Knowledge Services podcast. I’m your host for today’s episode, Matt Kohut. In each episode, we focus on the role NASA’s workforce plays in advancing the agency’s mission through the development and sharing of knowledge. Today’s guest, Thomas C. Jones, is an expert on inflatable habitats. Tom worked at NASA Langley Research Center for more than 16 years before moving over to Marshall Space Flight Center in 2023. He has performed structural analysis, design and testing of large, lightweight deployable and erectable space structures and manned inflatable modules, and he co-authored NASA’s certification guidelines for crude, inflatable soft goods structures. Here’s our conversation.
Tom Jones, thank you so much for joining Small Steps Giant Leaps.
Tom Jones: Happy to be here.
Host: So, let’s start by defining what an inflatable habitat is. Are the terms “expandable habitat” and “inflatable habitat” interchangeable?
Jones: Yeah, so it’s an interesting question. Typically, they are interchangeable and inflatable habitat to start is essentially a large, inflatable volume. It’s an alternative to a typical rigid shell structure for habitat. We’ve been looking at these structures going back essentially all the way to the beginning of NASA, but the expandable habitats can include other vessels which may actually have rigid elements as well. So, we’ve looked at concepts in the past that have rigid telescoping structures for instance, and also mechanically deployed structures. There’s a structure out there called the Hoberman Sphere, which you can actually buy as a toy, but it’s basically a small, mechanized device that deploys out into a sphere from a very small volume.
There’s different structures that can be built that can be considered as expandable but the reason the inflatable structures are typically what we consider as an expandable for a habitat application is the fact that if you use a rigid structure, it’s going to have a lot of hinge lines in it and those hinges can add additional mass. They add some additional risk due to the deployment. You have a lot of hinge points then in that design. Then for a large telescoping structure, one of the big concerns there is the seal lines that you have. Each of those sections that’s being deployed, if you have something that’s 10 – 20 feet in diameter, and it has a seal line around multiple seal lines of that diameter, that’s a concern particularly when we go to the moon where seal lines are one of the areas that dust can infiltrate. So, it’s a yes or no question. Yes, inflatable structures have been used interchangeably with expandable habitats, but there’s good reason why we’re looking at inflatables specifically.
Host: You mentioned that inflatables have been something that NASA has been investigating since the early ‘60s. What were some of the early concepts and milestones that helped to bring this technology to the point that it’s at today?
Jones: So, during the ‘60s, NASA Langley did a lot of work with Goodyear Aerospace, and there’s some great pictures online of some of the concepts that they came up with, but they were looking at these large toroidal looking inflatable structures, which could be used for a space station.
Then a little bit later on in that program, in the later ‘60s, as the Apollo missions were going on, we were looking at possibly extending the Apollo missions beyond just a few days, and for those longer duration missions, they were looking at habitats that could be inflatable for that. There was really a big gap then after the ‘60s all the way through the late ‘90s where the focus wasn’t on inflatables. We were doing a lot of the programs between those like Skylab, and Space Shuttle, and building up the ISS. But in the late ‘90s, there was a program called TransHab, which is short for Transit Habitat which was led out of Johnson Space Center and that was a three-year program where they really helped drive forward a lot of these technologies they used and are being used as the baseline for today’s developments of inflatables.
A lot of the work that was done back in the ‘60s, it was more prototype concept work, and they did look at a lot of different approaches. So as we talked about expandable structures versus inflatable. They did look at some of those concepts for telescoping rigid structures and mechanized deployments, but in the late ‘90s under the TransHab program, they really started getting down into the details of how you build one of these structures, what the architecture looks like, what the layers look like, how to integrate things like windows and hatches into these inflatable shells, how to design and test the micrometeorite shield, which would be made of soft structure. They did a lot of technology development which was then patented. That actually then got licensed by Bigelow Aerospace, and Bigelow Aerospace over about a 20-year period from 2000 to 2020 were developing those habitat technologies which led in 2016 to the BEAM module. Then from the BEAM, we went into the current NextSTEP program, and we’re working with several different commercial companies on developing inflatables. That was really the timeline of those events.
Host: Let’s back up a little bit before the BEAM, and you mentioned that these inflatable habitats have these multi-layer shells, and these are made of so-called soft goods or materials that are specifically designed for this purpose. Tell us a little bit about how these multi-layer structures are designed and what goes into them.
Jones: Yeah, so each layer is designed for a specific purpose. There’s a number of different layers in there. You’re talking 20 or 30 layers total of various different types of fabric and membrane material. So going from the inside of the spacecraft, we have a scuff layer on the inside, which is something like Nomex material. That helps protect all of the outer layers from any kind of damage from inside. So, you have astronauts moving around in there. You have logistics that are being moved around. Then beyond that, you have typically two to three bladder layers. So those are the layers that actually retain the atmosphere inside the spacecraft. They’re nonpermeable. Those are spaced apart by felt layers typically. So, we’ve used Kevlar felt in the past. It gives it a little bit more strength and durability. It allows if you have a little pinhole leak in one of the bladders, it’s not going to allow a leak of the entire spacecraft. So, there’s generally redundant bladders.
Beyond that layer is a layer that a lot of the testing is focused on, which is the restraint layer, and that’s the actual structural layer that’s holding in the pressure load. You can imagine for a large space structure, and particularly for inflatables where they may be very large in diameter, those stresses become quite high. So, there’s a lot of work done on designing that and laying out the restraint layer. Each different company in NASA itself have different configurations of elements to form that layer, and you have to do testing on each of those. Essentially, the idea of that layer is to provide the strength and durability to the overall structure. Beyond that, you have layers which essentially protect those inner layers of the bladder and restraint layer and obviously the astronauts inside the habitat.
So, you have MMOD layers, which is micrometeorite and orbital debris, and the configuration of that is what we call a Whipple Shield. It’s essentially a series of layers that are spaced apart, and those layers are often things like Nextel or Kevlar. The way that we do an analogy to that is you can imagine a series of bulletproof vests that are split apart, and the idea is you have these very fast micrometeorite particles coming in or orbital debris that’s traveling at very high velocity. It hits the outer layer of that shield and it breaks up, and then the next layer down is dealing with smaller particles, and you gradually reduce the energy out of those particles. The idea of designing that is to design it so that it never gets down to the level of the restraint layer. There’s been a lot of testing on that. A lot of the pioneering work in that area was done during the TransHab program, and they developed the analysis to design those layers.
Beyond the MMOD, we have MLI, so multilayer installation. It’s a lot of heritage on the MLI. It’s essentially aluminized Kapton in multiple layers. On the outer layer of everything, we essentially have a corollary to the inner scuff layer. We have an outer layer that protects everything from atomic oxygen. So, if you’re in lower orbit, there’s atomic oxygen which can eat away at these synthetic materials, so you have a layer outside that helps protect against that. Then if we’re going to the moon or Mars where you’re trying to set up a surface habitat, you have to have an outer layer that’s going to protect from the dust environment. That’s something that’s an ongoing area of research and is particularly of interest to the astronauts and the astronaut suits. They’re going to be walking around in the dust so we’re going to be leveraging a lot of the research that we do on their outer layers as well.
Host: So, it sounds like there’s a combination of some materials that have significant heritage, as you said, and others that are probably really cutting edge to the moment. I’m curious if there was a breakthrough moment as far as some of the materials that have come about in the past, say, two decades or so. Were there specific materials that had to evolve to the point where they could do the things that were needed for the BEAM, for instance?
Jones: Yeah, so during the TransHab program, the baseline for the structural materials, so the restraint layer material was Kevlar. There was obviously a lot of heritage there from military application of Kevlar. During that program, they also started to look at a material called Vectran. Vectran is similarly a synthetic material with very high strength to weight ratio, but it had some nice properties to it. Essentially, it made it the baseline material for all structures that were built after that time with TransHab.
So, the BEAM has Vectran webbings in it and all the current developed inflatable structures, all the ones that are in development are using Vectran materials for that structural layer. The reason for that was that it has some good properties for lifetime. So, you can imagine a habitat is going to be under pressure possibly for several years, possibly for ten years or more. Vectran is very good in creep, which is that long, duration stretching that you get under load. So Vectran was a big one. Like I mentioned before, the materials that are used in some of the outer layers have quite a bit of heritage. The most external layer for the atomic oxygen or the dust layer is typically Beta cloth. That’s something that’s been used for years and years. It’s actually an area now of possible research because there’s more and more emphasis on reducing forever chemicals. Beta cloth has some of that in it – PFAS. So, they’re looking at alternatives for that, so that may be a new area of need in terms of development.
Host: Speaking of low-Earth orbit, let’s talk about lessons from the BEAM. I’m curious what NASA has learned from that deployment and how that learning is informing both today’s technology and today’s mission planning.
Jones: Yeah, BEAM was a great demonstration module. So it’s been up there eight years now. It’s been recertified for use through essentially end of life for ISS. Originally it was only designed for a two-year mission, so it’s really proven the long-term viability of having inflatable structure in orbit and something that a crew can go inside and use. Interestingly, after the two-year initial test program, it was converted essentially into a logistics storage module which sounds somewhat mundane, but it actually is a good demonstration of how an inflatable structure can allow you to have a very large volume for logistics. That’s actually a very important consideration particularly for long duration missions. Obviously, ISS is a long duration mission, but we’re looking at long duration surface missions on the moon. We’re looking at transit missions to Mars and long-term surface missions on Mars. So where you store those logistics for those missions is critical. Having inflatable structures, something that’s highly packageable and then deployable allows you to store all those logistics without taking up the entire livable volume of a rigid structure. You can see that in a lot of the images that you see on the inside of ISS. There’s just so much stuff in there. So that was a great demonstration of BEAM.
Then one of the lessons learned from BEAM after 2016 was we had never really certified a structure like this before. So, there wasn’t guidelines in place on how to go about that, so there was a lot of using requirements and standards that had really been written for rigid structures and metallics. So, one of the things that we did immediately after BEAM was start working on the guidelines for certifying inflatable structures for crude applications. That was something that was published a couple of years back now, but its what’s been used for essentially directing the kind of testing we want to see from our industry partners as they go through the development and certification of their inflatable habitats. The last thing with the BEAM is that they did put instrumentation systems on there. So, we had a distributed impact detection system, or DIDS, which was a series of accelerometers put on the inside of BEAM. That was to detect impacts from meteorites. Didn’t get a huge number of positive hits there, but part of it was where they located BEAM was in the off side of ISS in terms of the direction of travel. So, it was a relatively well protected area anyway.
But also one of the things that we learned was that you picked up other things in the station going on in terms of vibrations and astronauts moving around and spacecraft coming in and out so that those signals also show up in an impact detection system. So that was an interesting thing that was picked up there. They also looked at radiation levels inside BEAM over a period of time. Essentially the radiation levels were nominally the same as they were in the rest of the station, but one interesting feature of inflatables on soft goods is because they’re synthetic polymer materials for the most part, they actually don’t produce secondary radiation which can be a concern for astronauts. So, if you have materials that are made of heavy molecules like metals, when you have radiation come in, it can produce secondary radiation that can be damaging. Soft good structures don’t have that, so that’s a feature of inflatables. A couple other things they looked at in there were microbial readings. They did sporadic readings of that, and I think have continued that throughout its life. Again, those have remained nominal.
One of the concerns with having an inflatable is the fact you have these rubberized and fabric surfaces in there. They may be a little more prone to having microbial issues possibly versus just a metallic surface. It’s just a little bit easier to keep that clean, but they saw the – they were not seeing any readings that were significantly higher than anything else they were seeing on station. So that was good information to have. Then the last one was they did measure temperature and they’ve continued to monitor that, but the passive thermal performance of these structures have also been shown to be very good. So, they actually insulate quite well. There’s a lot of interesting things and lessons learned out of that program that have helped inform these programs that have come since then.
Host: Now it took over seven hours to inflate the BEAM. Can you walk us through at a high level how that type of a process works?
Jones: There’s several steps to the launch and then the deployment of any inflatable, and BEAM obviously had to go through those steps. One of the things that did affect BEAM and the whole deployment was the fact that there was a launch failure of the Falcon 9, prior to the one that they were launching BEAM on, which ended up causing a delay of about 10 months on the launch. So, it stayed in its very packaged highly compressed state for 10 months more than was anticipated. So, you can imagine if you have something that’s made of these various soft materials and you’re squishing it down, and now you’re holding in that configuration for a long period of time, and then launching it into the cold and vacuum of space, the thing kind of wants to stay together. So, they ran into that issue when they started to deploy it. Prior to that, once they had launched it and got it up to the station and connected it to the station with a robotic arm, the first series of steps they have to go through is they release the restraint straps. They had three restraint straps on the outside of the vessel. They also had some launch lock bolts that were connecting the two bulkheads together on each end.
So, they released those so that it could now deploy axially. Then the last part of it was essentially closing a valve. One of the key things for an inflatable is when you’re launching it and you’ve packaged it down, it’s possible to get some trapped air in there. It’s almost impossible to get all of the air out of it, so you have to have a clear path for that air to be able to escape from the inside to the outside as you go from sea level up into the vacuum of space. So, they have essentially a vent valve that’s open. Right before they do the pressurization, they have to close that up and then they essentially are just putting bursts of air into it. This was a demonstration module so it may not be the final way that they do it for a habitat, but essentially it was done manually with an astronaut opening and closing the valve, and they did that over a series of about 25 separate manual valve openings and closings. As they were doing that, when they first started doing that, they were noticing that the pressure was rising, but the structure was not deploying the way that they expected it to.
So, they backed off of that. They let it sit and rest for a little bit, relax the material. They depressed it a little bit. Then they came back and started putting a little more gas into it in bursts and it gradually moved it out over that seven-hour period, but a lot of that was probably due to the fact that it had been compressed for so long that you had to just allow it a little bit of time to relax and expand on its own as you fed the gas into it.
Host: Moving into the present here, what do we understand well about these kinds of structures at this point, and what do we still need to learn before we’re ready to place one, say, on the moon for the Artemis astronauts?
Jones: Yeah, so there’s been a lot of great work done I think over the last 20 years. Certainly, there was a lot of concept work before that, but starting with TransHab and going through from 2000 onwards, we’ve really learned a lot about the design and the testing and the performance of these structures. So, there are still areas where we need some additional research and testing. One of the big ones is the instrumentation and analysis and the validation of the performance models for these types of structures. Soft goods, habitats are made of materials that are typically nonlinear. So, you can imagine a composite or metallic structure there, essentially fixed in place. But in a soft goods, there’s a lot of motion that’s possible. So, before you inflate the thing, every cycle that you do on it is going to slightly change that stiffness behavior. So, one of the things that we look at is cycling the load a little bit before we actually finally deploy it, or cycling the materials before they go into the final fabricated article to reduce some of that nonlinearity. But it’s still a challenge to model that accurately, particularly with these built-up architectures with multiple layers and the structural layer itself has a lot of components to it. So that’s an area of current research.
The other side of that is integrating instrumentation into that structural layer so that you can actually monitor the performance of it over time. There’s two reasons for that. One is a risk mitigation as we use these for the first time that we can monitor the performance of that structural layer, because it’s not directly viewable. You can’t see it from the inside because of the scuff layer on the bladders. You can’t see it from the outside because of the micrometeorite layers and the MLI, so we really want to integrate some sensors on the body of the structural material so that we can track its strain over time. We can see what its creep performance is like and then hopefully validate some of that with models and tests that we do on the ground.
The other area is dust mitigation and what those outer layers may look like. I mentioned that before with – that’s also a concern for the space suits, what material we may use, and then with Beta cloth and the fact that it uses these forever chemicals. There may be a requirement eventually in terms of using something different. So that’s going to be an area as well that we still really need to research and get a handle on. Then the last part, particularly for inflatable structures is the integration of hard structure. So, if you have a metallic habitat, it’s a lot easier to integrate essentially a penetration so a window or a hatch. It’s a little more simple to do that versus in a soft goods structure, you have to have the interfaces between the soft goods and that hard structure, and seal lines between the bladder and that penetration.
So that’s where a lot of the work has also been done. For module-level testing, they have to test it with those – with that hard structure integrated. That’s something that – you can see some of the videos that Sierra Space has put out recently on the tests they were doing at Marshall with an integrated plate to demonstrate some of that. That’s still an area for each architecture to prove that out that you can put in those types of structures.
Host: One last question for you, and it really follows what we were just talking about. What do you see as some of the most promising developments on the horizon over, say, the next decade for these technologies?
Jones: Yeah, I mean the most promising development to me is really after these 20 years since TransHab, we’ve been doing a lot of the kicking the tires and doing a lot of that testing to get us to the point now where I think there’s confidence in inflatable structures being a viable solution. The concepts have always been there in the architectures, and the desire to have these as usable elements I think has always been there, but the thing that’s really exciting now in terms of development is that we have multiple commercial companies that are in the process of developing inflatables and doing that testing currently. So, I think there’s multiple viable approaches and pathways to getting habitable elements actually in orbit both for NASA’s application obviously in space, and on the moon, and eventually onto Mars, but also for a lot of commercial applications.
So, there have been – these companies want to build a viable commercial enterprise out of building these structures. Things like in-space manufacturing, medical/pharmaceutical developments, developing new materials in microgravity, and even things like tourism and entertainment are things that commercial companies are interested in using these inflatables, and having private spacecraft essentially that would allow people to use them for these kinds of applications. The other thing that’s very interesting to me at least is the extension of this technology to other areas beyond just the habitats. So, there are other elements in the architectures that could use inflatables. So, things like airlocks in space or on the surface – those could be inflatables. Tunnel elements – so elements that connect multiple habitats as you build up an outpost, or an element for instance between a Rover and a habitat. Those kinds of things lend themselves well to a deployable structure. Even things like fuel and in situ resource use. So, the resources that you’re extracting could be stored in an inflatable. We’ve had folks who had looked at cryogenic storage in an inflatables. So, you can launch a series of tanks that can be very large, or you can package them in a pretty small rocket and land them fairly easily.
There’s a lot of interesting applications directly from that, and then we actually have a current open challenge. So, it’s an open source challenge, and we do these every so often, called the Big Idea Challenge where we’re currently looking at inflatable applications beyond habitats. We’ve gotten some very interesting proposals back on that in terms of novel uses of inflatables for various different applications and mission specific things. So yeah, there’s a lot of promising developments I would say both for habitats and habitat-derived inflatables and the use of inflatable technology beyond that.
Host: It certainly sounds like it. Tom Jones, thanks so much for speaking with me.
Jones: My pleasure. Thank you.
Host: That’s it for this episode of Small Steps Giant Leaps. For a transcript of this show, or more about Tom Jones or the topics we discussed today, visit our resources page at APPEL.NASA.gov/podcast. Don’t forget to check out our other podcasts like Houston, We Have a Podcast, or Curious Universe. Thanks for listening.