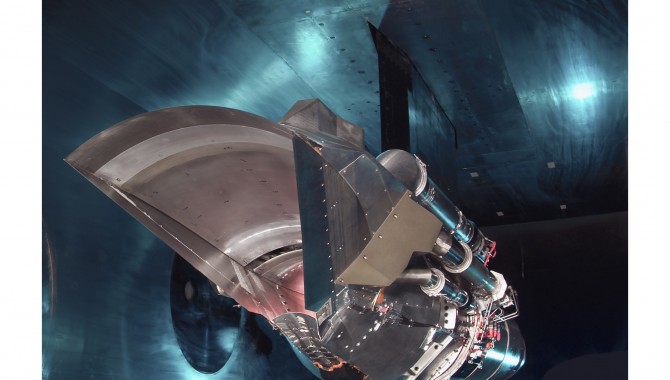
Jerry Mulenburg
The Parametric Inlet model is shown in a wind tunnel at NASA Glenn Research Center on October 24, 2003.
Usually when an organization announces an efficiency drive that could mean budget cuts and workforce reductions, people scramble to circle the wagons and protect their jobs — to convince the higher-ups that their work is essential and no one else can do it. But NASA’s Fabrication Alliance met the efficiency requirements of the Agency’s 1994 Zero Based Review (ZBR) by building a cooperative relationship among NASA research centers. In the process of eliminating duplicated efforts and reducing costs, the Alliance created a mechanism for sharing skills and work.
When the Agency instituted the ZBR with a goal of consolidating efforts and creating more efficiency among its centers, no organization faced a greater threat to survival than the Office of Aeronautics & Space Transportation Technology (OASTT, Code R), which included Ames Research Center, Dryden Flight Research Center, Langley Research Center, and Lewis Research Center (now Glenn Research Center). “We all knew that we were kind of in trouble, especially in the area of manufacturing,” said Peter Murray, former Chairman of the Fabrication Alliance and retired Deputy Chief, Manufacturing Engineering Division, from Glenn. Manufacturing at NASA centers often means producing complex, one-off prototypes and components — not a process that lends itself to efficiency.
In an attempt to meet ZBR goals and identify possible inefficiencies, Code R created an intercenter team called Project Reliance. Nearly 80 key people — two to three individuals from each function within the aeronautics centers — gathered for one intense week at Ames. The participants created subteams according to their functional specialty, including acquisition, engineering, Automated Data Processing, experimental facility operations, manufacturing, plant management, technical information production, and technical library. Guided by a Steering Committee of senior managers from each center, Project Reliance aimed to identify future opportunities for making the most of our resources. The manufacturing subteam saw itself as an investment to ensure that Code R fabrication / manufacturing capabilities would be managed effectively and efficiently across the Agency.
Foundation of Trust
Dubbed the Fabrication/Manufacturing Co-Op, the manufacturing subteam’s initial mission was simply to continue the collaboration that Project Reliance had started among Ames, Dryden, Langley, and Lewis in order to improve manufacturing capabilities through cost-effective methods. “Folks … went in with a lot of apprehension about what the outcome was going to be … even to the extent that all the civil servants could possibly go away following this exercise and we would need to find another means by which to get fabrication manufacturing work done in the Agency,” said Stewart Harris, Associate Director for Fabrication at Langley and current Chairman for the Fabrication Alliance.
To overcome the initial apprehension, the co-op focused first on getting the right people involved, which included at least two individuals from each center. The co-op wanted one of those people to be at the division level, “someone that could … make decisions for the organization, make decisions for the center, and work issues [in] real time,” Harris said. Once the right people were in place, the group focused on building trust among the centers. One of the first steps to building trust among this new team, however, was to throw titles out the window during meetings. “When we got together, we sort of dropped those titles that we all covet so much . … Everyone felt like they had an equal say and what they had to say was important,” Harris added.
Communication and participation were strongly encouraged and occurred through weekly teleconferences and face-to-face meetings held two to three times each year — practices that continue today. The co-op meeting location rotated among the four centers and allowed members not only to meet their colleagues in person but also to tour each center’s manufacturing facilities and better understand their capabilities. “We started out trying to really benefit from areas that one center had that we didn’t. In other words, we weren’t trying to take anything away from a center, we were trying to use their expertise,” Murray said.
Through a combination of fostering personal relationships across the centers and building a catalog of expertise that listed points of contact within each center, a firm foundation of trust grew among the co-op members. Soon, each co-op participant felt comfortable calling any other member for help at any time.
A New Objective
When Pete Haro, the first Chairman of the Fabrication/ Manufacturing Co-Op and Chief of the Manufacturing Division at Ames, retired in 1996, I became involved with the co-op as the Ames hardware development representative. It was immediately clear to me that these folks were on to something big. Not only was the co-op model important to Code R’s effectiveness, but it also had high potential value for the entire Agency.
A cross-center user group had already successfully solved the problem of incompatible Computer Aided Manufacturing (CAM) software by agreeing to use common software. Part of this effort included a joint-center training class instead of multiple training sessions at each center — an efficiency that also forged new bonds among those who attended.
The co-op also gained access to the Surplus Utilization Expert, a computer tracking system created by Glenn for obtaining excess government equipment and materials, which saved hundreds of thousands of dollars. Co-op members acquired excess metals and new, or near new, equipment for only the cost of transportation from its current location to the requesting center.
Another major early accomplishment was the acquisition of a single, joint-center contract to obtain outside fabrication services — the first of its kind. The Reliance Consolidated Models Contract allowed all co-op centers to obtain estimates from any one contractor, or all three, and then choose the best offer. Instead of contractors competing and administering separate contracts at each center, outside fabrication work now only required a simple task order. An unexpected benefit from this contract was lower cost estimates from the three contractors — as much as 20 percent less than our earlier experiences with them.
Having achieved these successes, the co-op met in Houston in January 1997 to reinvent and rejuvenate itself with a new set of goals, objectives, and operating policies. Among these were actions each center would undertake that were tied to expected returns from increased efficiency and effectiveness.
We agreed to limit specialized fabrication capabilities to centers that currently had them or to one center that would obtain a capability and share it. Langley, for example, procured a new rapid-prototyping stereolithography system, and the other three centers sent their stereolithography work to Langley instead of purchasing their own machines. By using the common software now in place at all centers, Langley could manufacture and ship products back to another center within a day or two, eliminating both duplication of expensive equipment and significant time and cost to contract the work out. This decision alone represented a savings of more than $1.2 million and cut required labor for this work by two-thirds.
Careful documentation of our efforts revealed returns in excess of $16.5 million in savings and cost avoidance over the next five years. These new goals, actions, and expected savings led to NASA Administrator Dan Goldin awarding the Reliance Fabrication/Manufacturing Co-Op Team the 1997 Administrator’s Award for Continuous Improvement. With new confidence from several successful collaborations under our belt, we were certain the co-op would become a long-lasting success at NASA.
Within a year or two after the Houston meeting, we’d accomplished many of our goals. It was time to take another look at our future. To help our centers and the Agency, we began consolidating our centers’ capabilities into fewer buildings, eliminating satellite shops, sharing resources such as excess equipment or knowledge of specialized fabrication techniques, and sharing work when any center had available capacity instead of contracting it out. We also created subteams to address current issues, including common business practices, advanced manufacturing and technology exchanges, and a common manufacturing approach for implementing ISO 9000 across the Agency.
A unique problem the co-op faced, and still struggles with today, was paying centers for work they did for one another. The NASA financial system took months to process a funds transfer, but work for critical projects often had to be done in days or hours. Once again, our members’ ingenuity went to work. Although Ames could not quickly transfer funds to Langley for critical stereolithography work, Ames could order replacement materials and have them delivered to Langley — which we did, in quantities that covered Langley’s cost of materials and labor. We also used a barter system to exchange excess materials and equipment, and we created a system to allocate hours at the beginning of each year for potential work from other centers.
Spreading Our Wings
With some acknowledged uneasiness at the possible effects on the close working relationships we had developed over nearly five years, we recognized that it was time to expand beyond the aeronautics centers and invite other centers to the table. In April 1999, Goddard Space Flight Center joined our team. The advantage the co-op gained was easy access to Goddard’s unique metal-plating capability, which we had never had within aeronautics. In September 2000, Marshall Space Flight Center followed Goddard, and soon the Jet Propulsion Laboratory, Johnson Space Center, Kennedy Space Center, and Stennis Space Center fabrication organizations all joined. Now that we were a true Agency-wide team, the Fabrication / Manufacturing Co-Op was renamed the NASA Fabrication Alliance.
During this expansion, we realized that many of the aeronautics centers’ fabrication issues and needs were identical to those of other NASA centers. These new collaborations and exchanges bolstered our membership, resulted in sharing more sophisticated work, and nurtured the dynamic that made much larger projects possible.
One of those projects was a high-precision parametric engine inlet that needed to be fabricated for a wind tunnel test. Glenn developed a design for it then used the Alliance to divide the work among four centers. The initial drawing review began in early 2000; the work itself took 22,000 hours and was completed in April 2003. We could not have met the project milestones if we hadn’t tried something new and risky. Our creative scheduling included dividing up the complex inlet so its parts could be machined independently at five separate NASA centers. Building the many components simultaneously, instead of serially, was possible because of digital modeling, which our now standardized software allowed us to share across centers.
Weekly telephone conferences kept the project team in close contact, and we exchanged digital photos to show progress and to share problems, which also made final assembly easier. When completed, the precision-machined, mating flow surfaces matched flawlessly, and the project schedule was reduced by at least twenty-four months.
Another critical test of the Alliance collaboration capability came after the shuttle Columbia accident. Johnson was tasked to provide an exact shuttle wing section mock-up, and quickly, to test a theory that the wing’s leading edge failed due to foam striking it during launch. Building this precise mock-up of the critical wing section was more work than Johnson could do in the short time available. “Just by bringing that issue up at the [Fabrication Alliance] telecon, they were able to get the job done,” said Carl Voglewede, Branch Head for Fabrication Business & Contract Management Branch at Langley.
The mock-up wing consisted of more than 500 manufactured parts and 2,000 fasteners. To meet the extremely tight schedule, Johnson relied on the NASA Fabrication Alliance to fabricate many parts. The Alliance successfully coordinated the distribution of needed parts to the various centers in less than three days. We procured all materials, manufactured every part, and assembled the entire wing in just five weeks. We also provided all the direct personnel contacts needed at each center for immediate support and manufacturing implementation. Ames, Dryden, Jet Propulsion Laboratory, Marshall, and Stennis all provided essential support in the manufacturing of parts. The success of this project was exhibited in a video showing a test foam sample penetrating the mock-up wing’s leading edge. The “possible” cause of the accident suddenly became the “probable” cause.
These projects increased our technical knowledge and, more importantly, deepened trust among Alliance members. The strength of the Alliance partnership encouraged us to share hard-earned aerospace trade secrets obtained through past experience to an unprecedented degree.
Future of the Alliance
Nurtured and sustained for more than a decade by a handful of NASA fabrication experts’ grassroots activities, the Fabrication Alliance retains the spirit and energy of its original members. The Alliance formula — cooperation, not competition — resulted from having a joint goal, building relationships and trust among colleagues, identifying common goals and objectives with a real commitment to implementing them, and maintaining both face-to-face and frequent other communications.
Our members continually strive for innovation and still set new challenges for growth and knowledge sharing. “One of the things I’ve been working on is regional workforce development. How can we partner with academia, with industry, with government to develop the workforce for the future?” Harris said. After ten years of sharing and building knowledge across the centers, the Alliance faces the challenge of retaining it.
“As we lose personnel either through retirement or people moving to other jobs, the resource situation is getting more critical,” said Voglewede. “That’s something we’ve talked about in the Alliance, and we need to put some energies into that,” Harris added.
We continue to talk openly about the challenges we face, whether they are technical, resource driven, or Agency issues and initiatives, and we know that accurate, reliable information is only a keystroke or phone call away. Membership turnover has not hampered the respect or enthusiasm generated among the members, and lifelong friendships have resulted from the Alliance interactions. We truly know the meaning of One NASA.