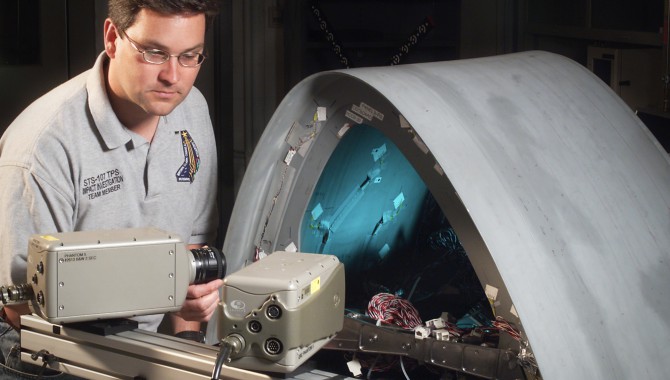
By Matt Melis
On February 1, 2003, Space Shuttle Columbia and her crew were lost during reentry. In the months following, a nationwide team of experts from NASA, industry, and academia, spanning dozens of technical disciplines, was assembled to investigate the causes of the tragedy.
Launch imagery and forensic reconstruction of the orbiter provided the evidence that enabled the Columbia Accident Investigation Board to determine the root cause of the accident. A piece of insulating foam had separated from the orbiter’s external fuel tank bipod attachment eighty-one seconds into the STS-107 launch, causing a breach in the thermal-protection system on the left wing’s leading edge. This breach allowed superheated air to penetrate and erode the aluminum structure of the left wing, which ultimately led to the breakup of the orbiter.
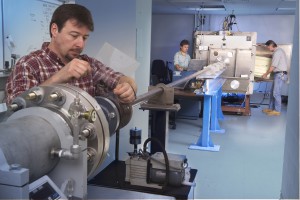
Mechanics Jeff Hammel (left) and Jim Sexton (right) prepare a ballistics impact gun for testing as aerospace engineer Mike Pereira looks at a computer monitor that will display photos of the blast taken by a high-speed camera.
Photo Credit: NASA
As the shuttle was being designed, the program team knew the metal bipod attachment connecting the orbiter to the external tank would require either heating or insulation to prevent large, and undesirable, ice deposits forming on it prior to launch. Building safety into a system—in this case, mitigating a threat from ice—might produce unintentional risks that could go unrecognized even after hundreds of flights or perhaps an entire flight program. Choosing to use foam insulation on the bipod attachment introduced a critical design flaw into the system, one that would not be fully understood until more than twenty years after the shuttle’s first flight.
The board concluded its investigation with a full-scale impact test that recreated the foam strike on Columbia in order to demonstrate that event as the most likely cause of the tragedy. Despite months of newly acquired experience in testing and analysis on the orbiter wing’s leading edge, dozens of engineers and technicians were still unprepared to witness the 16 x 17–inch hole created when 1.67 lbs. of foam hit the leading-edge article during the full-scale test. Their surprise and disbelief can be clearly heard in video documenting the test, emphasizing that a complete and rigorous test program is necessary to fully understand the capability and weakness of any given flight system—and that even seasoned experts can’t completely rely on their intuition once outside the bounds of their experience.
Working as One NASA
Prior to the loss of Columbia, NASA had performed limited debris-impact testing on shuttle structures and had no “physics-based” software-prediction tools to analyze such events. Physics-based software does what the name implies: it incorporates the laws of physics and engineering principles into the equations that make up computational tools. The agency did have significant expertise in impact physics at the Glenn and Langley research centers, but it was rooted in propulsion and airframe aeronautics research efforts, which were not typically partnered with NASA’s spaceflight programs.
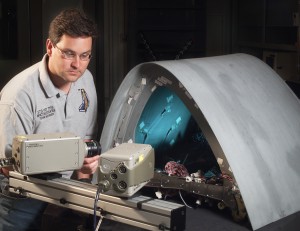
Duane Revilock sets up a high-speed digital camera in Glenn’s Ballistics Impact Laboratory to aid in testing the orbiter leading edge.
Photo Credit: NASA
After the accident, the shuttle program chartered an independent team of experts in impact analysis and testing from Glenn Research Center, Langley Research Center, Johnson Space Center, and Boeing to identify and develop rigorous, physics-based approaches to predict impact damage to orbiter tiles, leading edges, and structures. This team would also provide materials and impact-testing support to the STS-107 accident investigation and Return-to-Flight programs.
Coordinating from the orbiter office at Johnson, our core group performed much like a football team: teammates with clearly defined jobs to do. Glenn was responsible for an enormous amount of impact testing, developing material models and then ensuring they would function correctly once integrated into the analysis software. Langley conducted materials tests and performed validations on the models from Glenn. Once the methods were accepted, Boeing would carry out what we called “production runs,” performing hundreds of analyses on shuttle components to ensure we were safe to fly and able to survive any debris strikes that were expected on a shuttle launch.
The team was highly effective from its inception, in large part due to having been assigned a well-defined set of milestones and goals to accomplish for the program. We were empowered to work independently, and we were allowed to do our jobs unencumbered by administrative burden. We certainly had plenty of e-mail in our inboxes and spent hours on teleconferences—constant communication that was necessary for our work.
Travel played a valuable if not critical role in building and maintaining the team’s effectiveness. Since we lived in different parts of the country, we would convene four to five times a year at one of the centers. Not only did we accomplish a lot of work at these meetings, but we also reaffirmed the trust and confidence we had developed with one another. Trust is a crucial component in high-functioning groups that depend on each other to achieve a common goal, and I believe it is established most effectively face to face.
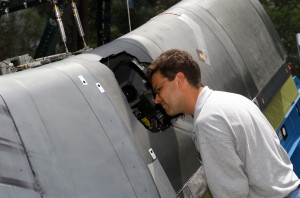
A test engineer inspects the hole created during full-scale testing of the orbiter leading edge.
Photo Credit: NASA Glenn Research Center
In a true “One NASA” sense, our multicenter analysis team would work together for nearly five years developing the sophisticated analysis capability the shuttle program uses today for making flight-rationale decisions. Through both personal and programmatic associations made in the years following Columbia, the expertise and capabilities existing at Glenn and the other research centers are now much more recognized and accessible by the flight centers. Several engineers at Glenn and Langley are still assigned to the shuttle program, further highlighting their recognized value to the program.
This expanded awareness of our expertise has also led to other efforts within NASA. We continue to advance jet engine fan-containment technology in the ballistic lab at Glenn to make our aircraft safer. Our analysts are also contributing to the development of NASA’s new Orion crew capsule for human spaceflight by helping design seats for the astronauts that will help them avoid injury in the event of a hard landing. Our advances in knowledge and technology during our Return-to-Flight efforts will most certainly continue to support the agency’s future aeronautics and spaceflight programs.
Advances in Technology
As often is the case with ambitious programs like Return to Flight, the development and maturation of new technologies are greatly accelerated. In fact, this occurred as a consequence of the ballistic impact-testing efforts.
The advent of digital photography dramatically improved NASA’s ability to accomplish its goals on the accident investigation as well as the Return-to-Flight program. High-speed digital cameras, largely unavailable and cost prohibitive just a few years before, were used extensively in both these efforts and provided near-instantaneous playback of any event they recorded. We used sixteen cameras to document the full-scale leading-edge test at rates of up to 30,000 frames per second—an unprecedented use of digital high-speed cameras.
Since the development of the digital still camera, a technique called “stereo photogrammetry” had come into practice. It accurately measured deformations on objects by using a pair of digital cameras to observe a test article from two points of view. Just as we sense depth using both our eyes, so can a pair of cameras—but with the added benefit of allowing us to apply mathematics to the images to compute precise displacements, stress, and strains for engineers.
It was a natural progression to apply these principles to the high-speed cameras being used to record the impact tests, and the NASA Glenn Ballistic Impact Lab worked closely with a commercial vendor of this technology to adapt the capability to use high-speed camera images. Once developed, this capability was critical for validating our analysis models. The technique was so successful that it was used on some of the full-scale leading-edge tests as well. Six years later, this technology is standard equipment in labs doing high-speed work both within and outside the agency.
The Rest of the Story
Early in 2009, the Orbiter Thermal Protection Group at Kennedy Space Center contacted us to inquire about getting some of our high-speed test video to present to their organization and enhance their understanding of debris-impact phenomena on their systems. Rather than provide only the movies, I offered something a bit better: a two-hour seminar summarizing the accident and describing how ballistic-impact research played a critical role in supporting the investigation and the Return-to-Flight effort.
More than fifty people attended that first seminar, and their response was so positive that I was asked to return to Kennedy to speak to all the technicians and engineers in the thermal-protection group. Over the next several months, I would present eight times to more than three hundred people who work on the shuttle orbiter.
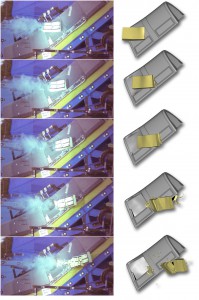
Comparison of the LS-DYNA predictions with high-speed video of the full-scale test.
Photo Credit: NASA
Feedback from the attendees affirmed two things. First, sharing our story was extremely valuable and worthwhile to the workforce. I presented dozens of high-speed impact-testing movies from our work—impacts on tiles, reinforced carboncarbon, windows, the external tank structure—materials that every tech and engineer attending saw or handled daily. They were captivated by the impact movies and the damage that could be caused by lightweight foam or a tiny piece of tile-gap filler. They also felt a sense of satisfaction as they learned how much effort the impact team had put into safeguarding their thermalprotection systems. There was a very strong sense of community and pride knowing what their teammates at the other centers had done to help make the orbiter safer.
Second, I became aware that creating such presentation materials for knowledge sharing, teaching our lessons learned, and preserving the agency’s history is invaluable to NASA as well as to our stakeholders. After the experience of speaking at Kennedy, I concluded it would be worthwhile to adapt our team’s story to video to permanently preserve it for future generations. Dozens of individuals with the debris-impact team worked tirelessly for more than two and a half years to overcome immense technical challenges to get NASA back to safely flying. Their story is worth knowing.
The shuttle is not unique in having dormant design flaws. They are inevitable in complex systems: aircraft, air traffic control, nuclear power plants, and even today’s financial systems are some examples. It is the job of those who tend to these systems to identify and resolve such flaws to ensure safety and mission success. To our credit, we’ve collectively done a commendable job. Our shuttle fleet flies safer than it ever has. Better imagery, better engineering, and more sophisticated analysis tools, as well as effectively learning from our past lessons, are just a few contributing factors. Nevertheless, in the business of spaceflight, we cannot relax until the wheels stop on the last vehicle to return home. Columbia will always be a painful, yet necessary, reminder for us to stay vigilant, always on the lookout for what lies hidden.