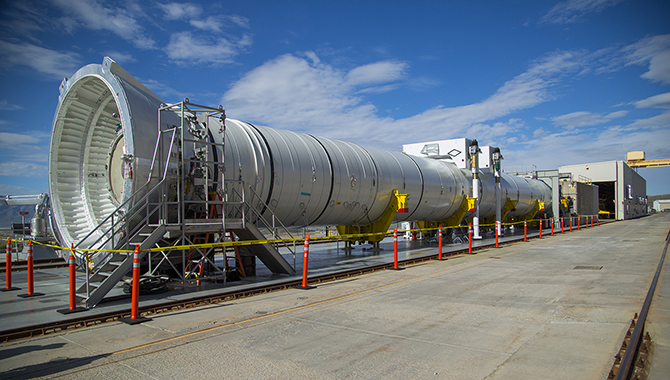
A full-scale test version of the SLS solid rocket booster is on site at Orbital ATK’s Utah test facility in preparation for the upcoming Qualification Motor-2 test.
Photo Credit: Orbital ATK
NASA’s Space Launch System (SLS), the world’s most powerful launch vehicle, is on track for the final ground-fire test of its solid rocket booster (SRB).
The SLS, NASA’s exploration class heavy lift launch vehicle, is being developed to enable manned deep space exploration for the first time in over four decades. The SLS is designed to achieve that goal while maximizing cost and schedule efficiencies by incorporating heritage hardware used in successful past spaceflight programs.
Its RS-25 engines first made their mark in the Space Shuttle Program. They have since been modified to meet the specifications of the SLS and will be used in a different configuration: four engines, not three, will propel the new rocket into space. The engines have also been reconfigured for greater thrust, with 512,000 pounds vacuum thrust for the SLS compared with 491,000 for the shuttle.
Twin SRBs, designed to deliver more than three-quarters of the total thrust at launch, will power the SLS when it meets the Orion spacecraft for their first joint test flight, Exploration Mission 1 (EM-1). Like the engines, the boosters are derived from shuttle hardware, but they feature a supplemental segment for added power. This fifth segment includes extra solid propellant to provide additional lift before separation from the core stage.
The first ground test of a full-scale test version of the SLS booster took place in March 2015. The hot motor test, Qualification Motor-1 (QM-1), validated the SRB’s performance at the high end of its propellant temperature range. The entire booster, which contained 1.5 million pounds of propellant, was heated up to an average temperature of 90 degrees Fahrenheit. It was then fired up with an igniter that shot a flame 150 feet down the length of the rocket in order to light all of the propellant surfaces at the same time. This produced 3.5 pounds of thrust for the first 25 seconds of the test. The propellant then burned for roughly another minute and a half while the booster reached an internal temperature of more than 5,600 degrees.
A second SRB ground test, QM-2, will take place this summer at Orbital ATK’s facility in Promontory, Utah. For the test, which will assess the motor’s performance at the low end of its temperature range, SRB components will be cooled to 40 degrees before firing. The SRB is expected to generate as much as 3.6 million pounds of thrust during the test. As was the case for QM-1, more than 500 sensors will measure the booster’s performance.
The cold-fire test is a critical step in qualifying the SRB design for use in the SLS. It will be the final static test of the SLS booster. The next time the SRBs are fired will be for EM-1, which is scheduled to take place in late 2018.
The boosters are manufactured by Orbital ATK. The SLS Program is run by Marshall Space Flight Center and managed by the Explorations Systems Development Division within the Human Exploration and Operations Mission Directorate.