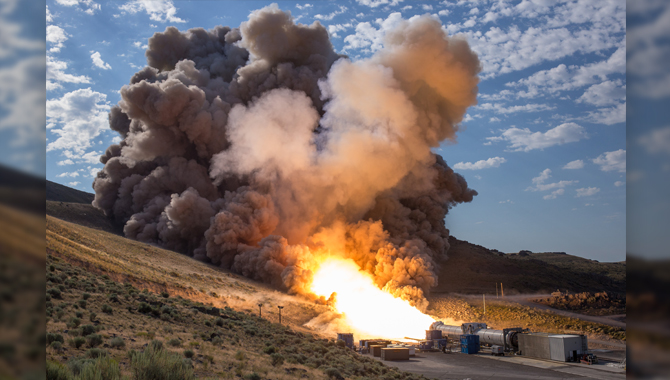
The SLS solid rocket motor burned successfully for two minutes during its final full-scale ground test, which examined performance at the low end of its propellant temperature range.
Photo Credit: NASA/Bill Ingalls
On June 29, 2016, NASA’s Space Launch System (SLS) successfully completed the final qualification motor test (QM-2) of its solid rocket booster (SRB).
The SLS is being developed to propel humans beyond low Earth orbit (LEO) for the first time in over four decades. Because that journey demands more power and lifting capability than existing rockets provide, the SLS will be the world’s most powerful launch vehicle. One example of its power is the SRBs: derived from space shuttle hardware, the boosters were redesigned to feature a fifth segment for extra thrust.
“To give you a reference point,” said Charlie Precourt, vice president and general manager of Orbital ATK’s Propulsion Systems Division in Promontory, Utah, “the shuttle, when it lifted off, was about 7 million pounds of thrust total between the two boosters and three main engines. The new Space Launch System will be about 9 million pounds of thrust for the two boosters and the four main engines on the core of that vehicle. So these two boosters had to be stretched from what we had on shuttle. Twenty-five percent more length and propellant results in a booster that went from 3.3 million pounds of thrust to 3.6 million pounds of thrust. And along the way, in meeting those challenges, we dealt with improvements to design, manufacturability, and so forth […] to make sure that this booster provides the best performance possible. Because when you consider space station is 160 miles to 200 miles up, the moon is 250,000 miles away, and Mars is 35 million miles away—we’re talking about being capable of providing tremendous delivery of systems hardware for the crew to be able to handle that journey.”
QM-2 was a critical step in moving the agency and nation along the journey to Mars. It followed the first booster qualification test, QM-1, which took place in March 2015 and validated the SRB’s performance at the high end of its propellant temperature range. During that test, the entire booster was heated up to an average temperature of 90 degrees Fahrenheit before burning for two minutes.
QM-2 tested the performance at the opposite end of the SRB’s temperature range. Before the test, the motor was cooled for weeks to bring the average propellant temperature down to 40 degrees. Examining both extremes of the temperature range is crucial, as propellant functions differently at different temperatures: when warm, it burns faster, creating more pressure; when cold, there’s less pressure but it burns longer. As a result, both qualification motor tests were necessary to ensure the SLS could perform as needed under a variety of potential launch conditions.
“It’s really important to bracket our flight performance requirements. This vehicle has to be able to fly from a propellant temperature of 40 degrees to 90 degrees. And we really want to maximize our launch availability windows. Being able to go to Mars doesn’t come around very often, and we want to be able to take advantage of those planetary alignment opportunities with a vehicle that’s robust,” said Alicia Carrillo, an engineer at Orbital ATK. “Temperature does affect, a little bit, how the propellant burns. It affects motor performance. And we need to be able to dial that in for vehicle trajectories.”
The qualification test got off to a slow start with a delay due to problems with the sequencer. “It’s a computer program that controls what happens next during the test,” said Bruce Tiller, SLS Booster Manager at Marshall Space Flight Center (MSFC). “You have to have that automatic system working to proceed with the test.” He noted, however, that the sequencer is part of the ground system and was not being tested during QM-2. To address the problem, the team at Orbital ATK’s testing facility simply switched out the hard drive for one that had a different version of the software, and the test proceeded as planned. The motor fired up successfully, completing the final full-scale ground test for the booster.
To ensure the test supplied the needed data, QM-2 included 82 test objectives over 530 instrumentation units. “They’re going to get a lot of data. There’s over 500 channels of data on this rocket. They’ll be pouring over that data to make sure that it performed exactly the way we intended it to perform at these cold conditions. That data will be really important to go ahead and say things are certified,” said Bill Gerstenmaier, associate administrator for Human Exploration and Operations (HEO) at NASA Headquarters.
Early test results appear positive. Alex Priskos, NASA SLS Boosters Office manager at MSFC, said, “We had a chance to look at some very, very preliminary data in terms of ballistics and the TVC [thrust vector control], and everything looks great so far. We’re going to be digging into data a lot more as we go forward.”
“This is a great test to confirm our design, [to show] that we’re on a good path to fly this design of this booster on Exploration Mission 1 [EM-1],” said Mike Sarafin, Mission Manager for the SLS’s first flight, which will take place in 2018.
Boosters for EM-1 are already in production, with three motor segments cast so far. Across the country, work is being done to move all of the elements of the SLS and Orion toward that first flight test. EM-1 will send the spacecraft into the proving ground, an area near the moon that is a quarter-million miles from Earth. There, Orion will encounter radiation levels beyond those experienced in LEO as it goes far beyond the GPS navigation constellation and communication satellites in geo-synchronous orbit. The mission will inform EM-2, which will be the second flight test of the SLS and Orion and the first crewed mission beyond LEO since the Apollo Program. EM-2 is planned for the early 2020s.
“All the pieces are moving forward. We’ve got activity heading on each one of these, we’ve got hardware and manufacture, we’ve got teams moving forward. These are not paper designs. We are really ready to move from EM-1 to EM-2, and then we’ll move into a flight rate roughly about once per year after that,” said Gerstenmaier.
The SLS boosters are manufactured by Orbital ATK. The SLS Program is run by MSFC and managed by the Explorations Systems Development Division within the HEO Mission Directorate.