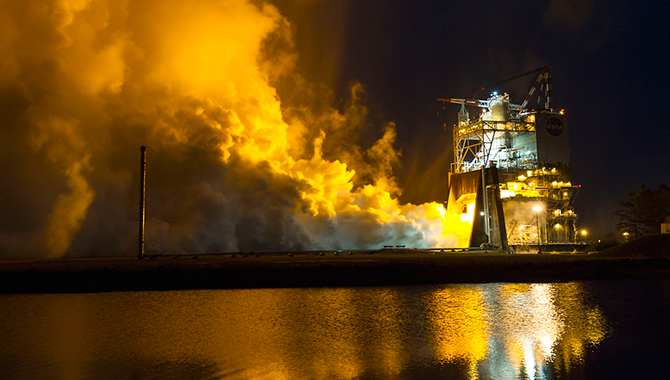
The SLS’s RS-25 engine undergoes a 500-second test fire at Stennis Space Center.
Photo Credit: NASA
The Space Launch System (SLS), NASA’s powerful new heavy lift launch vehicle, incorporates elements from some of the agency’s most successful past programs.
For 30 years, the RS-25 served as the space shuttle’s main engine (SSME). From the shuttle’s first mission in 1981 to its final re-entry in 2011, a three-engine cluster of RS-25s propelled the orbiter safely through low Earth orbit (LEO). During that time, the engine design underwent multiple upgrades and evolutions, enhancing its performance and reliability.
When it came time to retire the shuttle, NASA expected to retire its SSME as well. But things changed as the agency began exploring technology to support its emerging manned deep space exploration program. NASA faced the challenge of developing a heavy lift launch vehicle capable of safely sending humans farther into space than ever before, yet doing so under the constraints of a limited budget. The need for efficiency in terms of both cost and schedule led the program to focus on two areas: heritage hardware and cutting-edge manufacturing practices.
To maximize efficiency, the SLS utilizes a range of components that originally made their mark in other agency programs. In the case of the RS-25s, the engines have been modified to meet the specifications of the SLS. Four engines—not three, as for the shuttle—will support the new rocket. They have been reconfigured for greater thrust: 512,000 pounds vacuum thrust for the SLS compared with 491,000 for the shuttle. According to SLS Program Manager Todd May, the RS-25 “is the state of the art in terms of stage combustion. As an example, one of those engines has as much power as eight Hoover Dams.”
In addition to the RS-25s, the initial version of the SLS will feature two solid rocket boosters derived from shuttle hardware. Each booster has five segments, in contrast to the four-segment design for the shuttle. The fifth segment adds power: it includes extra solid propellant to provide additional lift before separation from the core stage. The launch vehicle also utilizes an interim cryogenic propulsion stage that leverages Delta IV-Heavy rocket design. This initial version of the SLS will be taller than the Statue of Liberty and capable of lifting 70 metric tons into orbit. It first flight will take place in late 2018, when it will carry NASA’s Orion spacecraft beyond LEO for Exploration Mission-1 (EM-1).
The SLS is designed to evolve over time as the needs of NASA’s human spaceflight program change. While the initial version will be slightly smaller than the Saturn V, the rocket that powered the Apollo Program, the engines will provide 10% more thrust off the launch pad. Its final (evolved) version, which will be capable of lifting 130 metrics tons, will be larger than the Saturn V. “This will be the work horse for heavy cargo and humans out beyond the moon to Mars and asteroids,” said May.
For the evolved version, a J-2X engine will power the SLS’s upper stage. The design of the J-2X is based on the J-2 engine and the Saturn V. The current version of the J-2X is capable of nearly 300,000 pounds of vacuum thrust, enabling the Orion spacecraft to go far beyond LEO.
Incorporating repurposed hardware is one way that the SLS program is containing costs. Using advanced manufacturing techniques is another. “As we pursue America’s next heavy lift rocket, our engineers are proactively looking for methods like [Selective Laser Melting (SLM)] that will make the rocket more affordable,” said May. SLM, a 3-D printing process, is being used to create parts for the RS-25 and the J-2X. The method contains costs by markedly reducing manufacturing time.
The repurposed RS-25 underwent a successful engine test fire on January 9, 2015, at Stennis Space Center. During the test, the engine fired up for 500 seconds. On March 11, the SLS’s five-segment solid rocket booster will go through its first qualification test: a two-minute, full-duration static test that will qualify the booster design for operation at the high end of its propellant temperature range. In early 2016, a second qualification test will take place to examine the booster’s low-temperature performance. After these critical tests, the booster hardware will be qualified for the first SLS flight, which is scheduled for late 2018. That flight will mark the maiden voyage of the SLS in conjunction with Orion as they take an important step toward advancing NASA’s deep space exploration capabilities.
Watch a video of the RS-25 engine test fire in January.
See how the SLS boosters are made.
Read an APPEL News article about Orion’s successful first flight, Exploration Flight Test-1 (EFT-1).