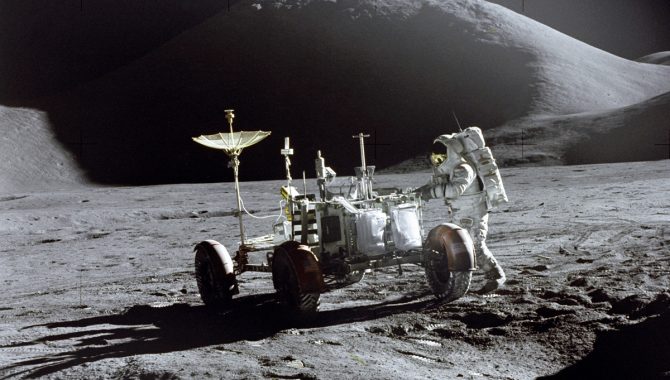
Apollo 15 Lunar Module Pilot James Irwin works at the Lunar Roving Vehicle during the first Apollo 15 lunar surface extravehicular. The folding “manned spacecraft on wheels” was a game changer for the Apollo Program, freeing astronauts to explore larger swaths of the lunar surface. This photograph was taken by Mission Commander David Scott.
Credit: NASA
Team develops ‘manned spacecraft on wheels’ on tight deadline.
On July 31, 1971, 50 years ago this month, Apollo 15 Commander David R. Scott and Lunar Module Pilot James B. Irwin began to operate a series of pulleys and braked reels to remove the contents of a modest compartment at the base of the Lunar Module (LM). What began to emerge and unfold, mostly automatically, was an engineering marvel—a 10 foot long, six foot wide, two-seat vehicle designed to exacting specifications to help Scott and Irwin traverse a wide swath of the harsh lunar landscape.
The Lunar Roving Vehicle (LRV) was a Cadillac folded down to the size of a Volkswagen, in the words of Saverio “Sonny” F. Morea, the LRV project manager. It was developed in just 17 and a half months. By the time Morea was tapped to lead the project, he had already distinguished himself as project manager during development of the Saturn V’s 19-foot-tall, 12-foot-wide F-1 engines, and then as project manager of the team that found the cause of J-2 liquid hydrogen/liquid oxygen engine failures and engineered design changes.
During a 2012 oral history, Morea recalled getting a call from Dr. Wernher von Braun’s office, offering him the project manager position on the LRV. Von Braun, the chief architect of the Saturn V launch vehicle, was then director of NASA’s Marshall Space Flight Center. “My initial response was somewhat negative,” Morea recalled, telling von Braun’s deputy, “I know propulsion. I do not know much about cars except I drive one.”
Von Braun sent word that anyone who could solve $1 billion problems in a bigger program could solve $40,000 problems in a smaller one. “You do not say no to Dr. von Braun,” Morea recalled. “He selected me to do this. He wanted me to do it, so I did it.” Morea, who was awarded the NASA Exceptional Service Medal twice during his career, recalled that the LRV turned out to be one of the more challenging assignments he ever had.
“Although deceptively simple in appearance, the LRV, in reality, was a highly specialized and complex, sophisticated vehicle more aptly described by using the terminology ‘manned spacecraft on wheels,’ ” Morea wrote in a conference paper, The Lunar Roving Vehicle: Historical Perspective, presented at Johnson Space Center during the Second Conference on Lunar Bases and Space Activities of the 21st Century.
When NASA issued a Request for Proposals on July 11, 1969, it was clear from the dozens of specifications that they intended to build a state-of-the-art, lightweight, folding spacecraft. The RFP specified an electric vehicle, weighing just 400 pounds on Earth, powered by redundant batteries, and capable of carrying more than twice its weight (two astronauts in their equipment and 100 pounds of science experiments) at 16 km per hour and able to traverse slopes as steep as 25 degrees.
The RFP specified a vehicle that could cover 30 km in a day with a high degree of reliability and redundancy. No single-point failure could require a mission abort and no second failure could endanger the crew.
“We could not take a chance that we were going to leave two astronauts abandoned somewhere because the vehicle broke down. We had to have duplicate batteries; each had the capability of driving the entire EVA [Extravehicular Activity] mission. We had to have separate electric motors in each of the wheels, so we basically had four-wheel drive. We could lose one wheel and the other three would continue to operate. We could lose a second one and the remaining two would continue to operate. We could actually lose three of the four motors in those wheels, and the last one would continue to operate,” Morea explained.
On October 28, 1969, NASA selected Boeing as the prime contractor for the LRV, teamed with General Motors’ Defense Research Laboratories as a subcontractor tasked with developing the wheels, motors, and suspension. Designing a vehicle for the harsh lunar surface contained many challenges for the team, but to Morea, the greatest of them was the pressing deadline.
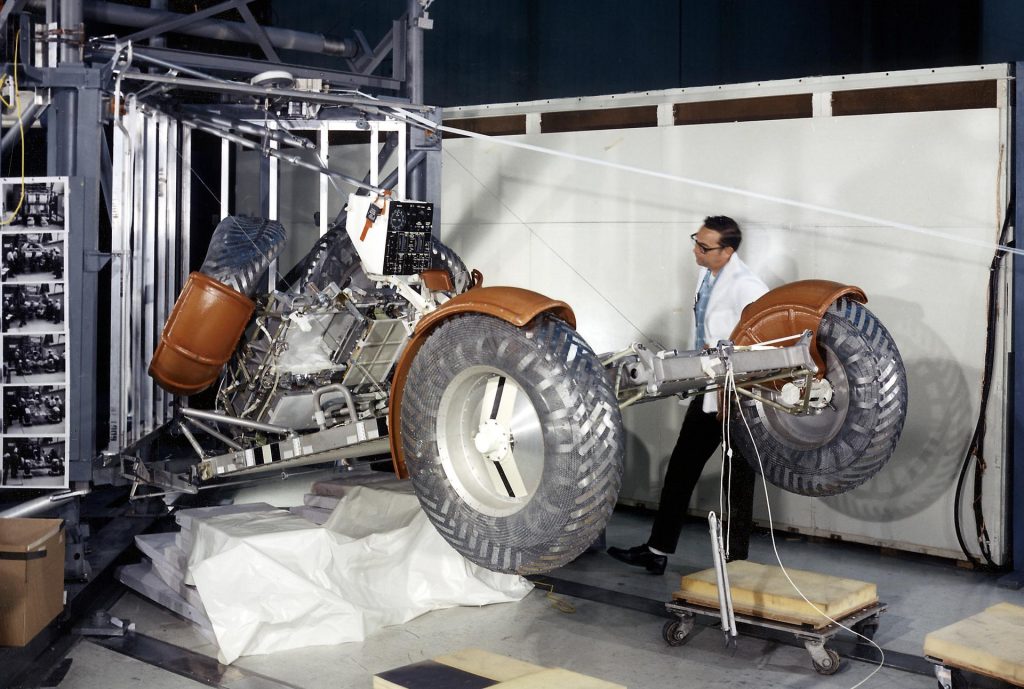
This photograph was taken during a deployment simulation of the Lunar Roving Vehicle (LRV).
Credit: NASA
“The biggest problem of all, strangely enough, was the fact that we had to design and develop this vehicle and man-rate it all in a seventeen and half [month] period from the time we signed the contract with Boeing and General Motors. We had to do this car in seventeen and a half months, and we did not know the environment we were operating in very well. That was the challenge,” Morea recalled.
The project was filled with technical issues that Morea said, “lent themselves to being solved.” One of technical issues was the development of the wheels and tires. The vehicle would operate in a vacuum on the harsh lunar soil, moving over rocks, through small craters, and around large boulders and steep hills.
“Certainly, there were temperatures on the Moon that were extraordinary. They would vary from plus 250 degrees to minus 250 degrees Fahrenheit, depending on whether you were travelling in the shade or travelling in the sunlit portion, depending on whether you were in early morning or whether you were at noon time, where the sun location was,” Morea recalled.
“Even if low weight considerations would not have eliminated the use of traditional rubber tires, the temperature and vacuum constraints did,” Morea wrote.
Instrumental in the wheel’s design was a team at G.M. led by Dr. M.G. Bekker, who in 1956 had literally written the book on the relationship between a motor vehicle and the physical environment, titled Theory of Land Locomotion: The Mechanics of Vehicle Mobility. The team performed extensive research with prototypes operating in simulated light gravity over fine-grained, lunar soil simulants.
The final design, which would perform flawlessly on the lunar surface, featured a spun aluminum hub. A solid titanium ring, known as a bump stop, was mounted to this hub and contained within a hand-woven mesh tire of zinc-coated steel wire. The wheel package was about 32 inches in diameter and 9 inches wide. Chevrons of titanium were riveted to 50 percent of the tire’s surface to improve traction.
Another key technical issue was development of a navigation system that would work on the Moon, which has no magnetic field. The system the engineers developed used a directional gyro initialized using a sun line, odometers at each wheel, and a small computer. The computer would take the starting point of the EVA (at the LM) and compute the vehicle position using data from the odometers as to how far the LRV had traveled and from the gyro as to the direction.
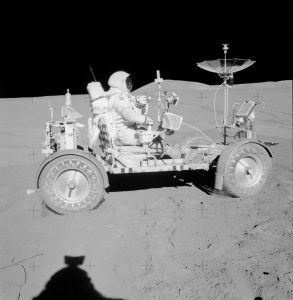
Astronaut David R. Scott is seated in the Lunar Roving Vehicle (LRV) during the first Apollo 15 lunar surface extravehicular activity (EVA) at the Hadley-Apennine landing site.
Credit: NASA
It didn’t take long for the hard work of the engineers and project managers building redundancy into the LRV to pay off during Apollo 15. On the first LRV EVA, Scott and Irwin ran down a checklist of switches and discovered that the front wheels wouldn’t steer. Because the LRV had a redundant system to steer the rear wheels, NASA decided to proceed with the EVA, which went according to plan.
“The steering is quite responsive even with only the rear steering. It does – does quite well,” Scott said from the surface of the Moon. “There doesn’t seem to be too much slip. I can maneuver pretty well with the thing. …It responds quite well. There’s – there’s no accumulation of dirt in the wire wheels.”
“Just like in the owner’s manual, Dave,” CAPCOM responded.
When the astronauts left the Lunar Module for the second LRV EVA, after some sleep time, CAPCOM talked Scott through a series of switch positions and asked the Apollo 15 Commander to test the front steering again.
It worked!
“You know what I bet you did last night, Joe? You let some of those Marshall guys come up here and fix it, didn’t you?” Scott joked. The front steering worked for LRV EVAs two and three.
The LRV was a game changer for the Apollo program. No longer were astronauts confined to distances they could walk in bulky spacesuits. Scott and Irwin traversed 17.5 miles of the lunar surface, much more than the previous three lunar missions combined. The astronauts of Apollo 15, 16, and 17 returned to Earth with 632 pounds of lunar samples, which are still being studied today.
“The astronauts who had the privilege of driving this machine on the lunar surface … all had very positive comments about its handling, performance, reliability, and the sort of machine the LRV was. In fact, the superlatives flowed quite easily in all the mission debriefings,” Morea wrote.