By the ASK Editorial Staff
In March 2003, a team from five NASA centers, two Air Force groups, the Army, and Sandia National Laboratories began work on a hypersonic re-entry vehicle intended to serve as a flying technology test bed for thermal protection systems, flight controls, sensors, communications, and other vehicle systems that need to withstand the rigors of high-speed re-entry. They developed plans for a 750-lb. vehicle that would be launched on a suborbital rocket from Wallops Island and achieve speeds ranging from Mach seven in early tests to Mach twelve and beyond. It was designed to then be slowed by parachutes and retrieved in mid-air by helicopter. The project was known as the Hypersonic Technology Experiment, or HyTEx. Working quickly, the team had a Preliminary Requirements Review in July, just four months after their start date, and a successful Preliminary Design Review (PDR) eight months later, in March 2004. Almost immediately after that PDR, however, the project was cancelled as a result of changing NASA priorities and budget pressures.
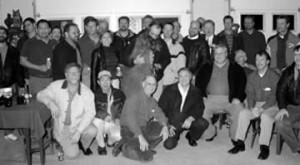
The HyTEx team stands with a llama in southeast Huntsville, Alabama, at a farm owned by Tony O’Neil, a member of the Marshall project management group.
Despite that disappointment, project participants remain extremely positive about the experience, citing outstanding cooperation among the multiple centers and organizations involved and the speed and quality of the work accomplished. Rich Nelson, Kennedy Space Center Advanced System Division Chief, a NASA employee for thirty-four years and part of the Kennedy Space Center group involved in HyTEx, says, “The PDR was one of the best I’ve been through. It went the way things should go.” Susan Spencer, deputy on the Marshall project management team, thinks of HyTEx as the project she is proudest of.
Project manager Jimmy Lee believes that the relationships of trust and mutual understanding established during the work will persist and have lasting value for NASA and the participants. “The success of the project is relationships,” he says. “The sense of trust sets you up for future engagements. You’re not making a cold call; you’ve got an existing relationship, and people will go out of their way to help you.” Nelson agrees, noting that the connections he established with colleagues at Wallops continue and provide a foundation for future cooperation. He says, “HyTEx showed that NASA centers can work in close collaboration without competing for resources.”
Ron Walsh, the Wallops project manager for HyTEx, attributes that successful collaboration in part to Lee’s clarity about the work to be done. “He had a very clear definition of system boundaries,” he says. “No one felt other people would encroach; they had a space to work in.” Because people were confident that these boundaries would be respected, they did not feel they had to protect their territories by limiting the information they shared or devote attention and energy to fending off attempts to grab part of their work. Thanks to what Walsh describes as “a sense of safety,” they were open to offering and asking for help.
At least as important as this clarity about boundaries and responsibilities was the atmosphere of openness, trust, and respect that Lee fostered. Part of that came from leading by example. “He’s a straightforward and trustworthy guy,” says Nelson, and Ron Walsh remarks that Lee’s positive and cooperative spirit was “contagious.” For Lee, an essential contributor to developing trust among team members was for him to trust them. He did not micromanage the project. Instead, he says, “I tried to give the vision and direction and let folks go off and do what they did best.” Characteristically, he underplays his role, saying, “If you’ve got people engaged in doing something they like to do, it’s easy.”
Lee also took concrete steps to build relationships with the team. He organized frequent face-to-face meetings with project leaders and other team members—as many as thirty or forty people at a time at meetings held at different NASA centers and at Sandia National Laboratory. Varying the location helped create a sense of equality and partnership that would have been lacking if meetings had been held only at Marshall, where Lee and his project management group were located. (Unusually, Marshall had no technical role in the project, only management responsibility.) These work sessions were followed by social times that helped team members get to know one another better and deepen their sense of connection. Often, the whole group went out for dinner together. Once, during the HyTEx Preliminary Requirements Review, the team met at the Cozy Cove Farm for a cookout. Tony O’Neil, a member of the Marshall project management group who owns the farm in Southeast Huntsville, graciously hosted the traditional southern cookout. In addition to the outstanding food and the opportunity to socialize with friends, Tony’s farm gave team members the experience of a “petting zoo” within the city limits complete with miniature donkeys, horses, llamas, and alpacas. After dinner that night, the hosts paraded several of their favorite llamas into the barn to mingle with the team and be admired.
Shortly after the project was cancelled, Jimmy presented a framed certificate with a group photo with one of the llamas to each person in recognition of their individual contributions to the team. The photo remains a prized souvenir of the project and exemplifies the team’s chemistry and unity. This was a fast- track project with a demanding work schedule, but Lee and his colleagues understood that taking time for social connection could help produce good results faster, not delay them.
Along with these meetings, frequent teleconferences kept team members in contact. Walsh remembers the calls as notably inclusive, saying, “Jimmy invited everyone in.” One result, says Nelson, was “enjoyable and knowledgeable” discussions and productive outcomes. He cites the example of work on the Experiment Management Unit that would be designed to transmit data from the flight experiments on board, one of the Kennedy Space Center responsibilities. Sandia had developed a similar system but one built for a specific, different payload. Rather than getting caught up in rivalry between Sandia and Kennedy, Nelson experienced a cooperative sharing of expertise.
None of this diminishes the real disappointment team members felt when HyTEx was cancelled. While they recognize that such changes in direction are a fact of life at NASA, they continue to believe in the value of the work. Their belief in the importance of the project—their shared sense of mission—was one of the things that supported their outstanding collaboration in the first place. (Some related work continues at Sandia.) Still, they see HyTEx as a model of how collaborations among multiple centers and organizations should happen. The approaches used, the spirit of the project, and the relationships that have survived it are all part of the lasting legacy of that intense year of work.
HyTEx Team
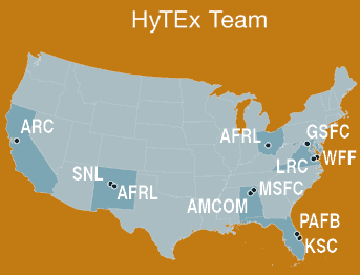
- ARC: Ames Research Center
- Thermal Protection
- System Experiments
- Vehicle Health
- Management Technology
- SNL: Sandia National Laboratories
- Re-Entry Vehicle
- AFRL: Air Force Research Lab
(New Mexico HQ) - Re-Entry Structures Experiment
- AMCOM: Army Aviation and Missile Command
- Aerothermal Analysis
- Ground Testing
- MSFC: Marshall Space Flight Center
- Mission Management
- AFRL: Air Force Research Lab (Ohio HQ)
- Thermal Protection
- System Technology
- GSFC / WFF: Goddard Space Flight Center / Wallops Flight Facility
- Booster
- Range And Launch Operations
- Recovery
- LRC: Langley Research Center
- Aeroscience
- Thermal Protection System
- Wind Tunnel Testing
- KSC: Kennedy Space Center
- Experiment Management System
- Experiment Processing
- Vehicle Health Management Technology
- PAFB: Patrick Air Force Base
- Recovery Operations