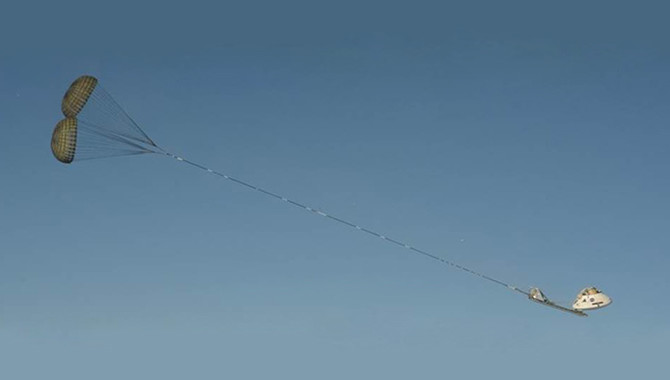
Two extraction parachutes were deployed behind a mockup of the Orion capsule during a recent test of the parachute system.
Photo Credit: NASA
In August, the Orion parachute system was put through a risky scenario: landing without two key parachutes. The results were even better than predicted.
The test, in which the Parachute Test Vehicle (PTV) was dropped without one of the drogue parachutes as well as one of the main parachutes, was part of a series of development tests known as engineering evaluation development tests or simply “EDU.” Designed to examine parachute performance in a variety of nominal and anomalous scenarios, findings from these tests will inform the final design of the system that will support Orion’s Exploration Mission 1 (EM-1) in 2018. APPEL News had a chance to learn more about the parachute tests from Stuart McClung, Orion Crew Service Module Functional Area Manager, Mechanical, Pyrotechnic, Landing Systems.
APPEL News: Thanks for talking with us again. We last spoke after Orion’s maiden voyage, Exploration Flight Test 1 (EFT-1). Is there anything you can share with us about what you learned from that flight?
Stuart McClung: It was a great mission. We basically got every test objective we wanted. It was really better than you could hope for to have that kind of success. Since then, all of us on the various teams have been picking apart the data from EFT-1, and where it makes sense we’re feeding it back into the work we’re doing. We wrapped up the critical design review for our [Exploration Mission] EM design—our long-term design—recently. So we’ve taken all of the knowledge from EFT-1 and said, “Where does it make sense to fine tune?” That’s a lot of what we’ve been doing since December of last year.
APPEL News: You said there were 1200 sensors on Orion’s first flight, so a lot of data came out of EFT-1. Were there any challenges in breaking it all down and getting it to everyone involved with Orion?
McClung: I don’t think you could ever get any of us on the team to say we had too much data. There was a lot of it coming off the vehicle, but once we got it processed, all the various teams knew which bits of data were their own. It got back to folks in January or February and now it’s getting used all over the place. And it will probably continue to get used. Each time we run a test, we’ll use it as another data point to reflect back on. It gives us a flight case versus a lab case.
APPEL News: You mentioned last time we talked that “every pound we take out is a pound we can put towards science.” With that in mind, did you alter the design of any parts after EFT-1?
McClung: Yes. We’ve actively carved some weight out of the EM design. That’s been one of the things we’ve been working on. On the cone section of the Orion spacecraft, we’ve modified the number of panels. It still has the same basic shape, but we’ve got fewer welds, making it a more efficient structure. So we carved some weight out of that.
The parachutes themselves are going to be about the same weight. We were already sizing them for the entry conditions that we’re going to see long term. We did that because if you change the chute a lot, then you have to test it more, and it’s expensive to test parachutes. So we tried not to make any global changes to the parachutes. Actually, we did do one thing that took some weight out of the chute. The parachute had steel risers for EFT-1. Early in the program, we thought that we needed to have steel in the lower part of the risers, around where the chute contacted the vehicle. Based on EFT-1 and other factors, we’ve moved from steel to Kevlar. So while the overall parachute looks same, the risers coming up to it that attach up to the vehicle have changed.
APPEL News: Have you been using Kevlar in the tests you’ve done since EFT-1?
McClung: Yes. We’ve been using it for the EDU tests for the risers themselves and also for reefing rings. Those are the rings buried inside the parachutes that are used to guide some of the ropes. They were steel rings and now we’ve made them cloth—Kevlar. Saves a little bit of mass and it also eliminates the risk of a pinch point when you pack the parachutes down. So from big things to little things, we’ve changed what we needed to in the tests. We’ve got another test coming up in January, our last EDU. And then we’ll tie a bow around our development testing and move into the formal qualitative testing of the parachutes.
APPEL News: How has the EDU testing been going?
McClung: It’s going really well. In August, we had the test where we intentionally failed one drogue parachute and one main parachute. That’s two significant failures. The chances of that ever happening are really quite low, but it could happen. At the end of the day, the vehicle has to be able to survive that and give the crew a good safe landing. So we tested it and the results were quite good. The vehicle was actually a little more stable under the drogue parachute than had been predicted, so that was encouraging. And the handover to the two remaining main parachutes worked quite well.
APPEL News: What will the upcoming EDU test in January examine?
McClung: For this test, we want to hit the parachutes with a high load case. So instead of using the PTV—the one that looks like the Orion capsule—we’re going to use the Parachute Compartment Drop Test Vehicle (PCDTV). That one looks like a giant lawn dart: it’s like a nice big missile and it falls much faster than the PTV. We’ll let it fall till we have the right speed and then hit the chutes really hard. So for the last test, in August, we were looking primarily at stability and how to handle failures. This January test will stress the system by putting a maximum load into the parachutes to verify that they can handle that load. It’s stressing the system differently than the last test, and visually it looks distinct because we’re using a different test vehicle.
APPEL News: So did each EDU test evaluate something different? Or were some repeats to see if the results were consistent?
McClung: Yes and yes. Each test had multiple objectives, some of which overlapped. We didn’t want to get a direct repeat, so we varied conditions a little bit, trying to get as many different scenarios as we could. This gives us a broader data set. For instance, for the last test we finished up under two mains. That was the fourth or fifth time we’d landed under two main parachutes. So we repeated that objective of testing under two main parachutes, but the handover points, the initial conditions, and some of the timing events were different. In other words, we varied some of the secondary features of the test objective to spread out the database. At the end of the day, parachutes are really certified by analysis and by being able to model how they perform. You make that model more robust by having a good, broad set of data points.
APPEL News: How does this set of development tests differ from the qualification tests you’ll be starting in 2016?
McClung: To an outside observer, the tests will look much the same. But when you get into the qualification tests, there’s a little more rigor and formality. Basically, development testing is intended to inform design. Qualification is the pass/fail of the final design.
While we’re going through the development series, we allow ourselves to intentionally evolve the design. Like the reefing rings that I talked about: going from metallic to fabric. Or modifying some of the stitching. There were all kinds of fine adjustments we made along the way. That’s why we run these development tests: to have the flexibility to tweak and fine tune.
When we get into qualification, we really clamp down on those kinds of changes. Our goal is to take the final configuration and run it—the unchanged config—through this battery of tests. We want to verify that the final config performs as expected through the whole suite. So we’ve already locked down the design.
APPEL News: Who designs the parachute tests you’re doing?
McClung: For the development phase, the tests were loosely laid out and we let them evolve as we ran them. When we go into qualitative testing, we’ll be a little more defined up front. That starts with a subgroup of our team, ten or twelve hard-core experts who are our subject matter experts. They include our NASA design team, the Safety and Mission Assurance rep, and the parachute vendor. They’ll sit down and decide what the test program needs to look like. In the case of parachutes, there’s not a good handbook that says, “Here’s what your test program should look like.” So that subgroup will set out their proposed test program and they’ll bring it into one of our control boards where the rest of us in the technical community will review it and provide input. We’ll all agree on the tests we need to do and what each will look like.
APPEL News: Has anything unexpected come up during testing so far?
McClung: We got a surprise in our test program a while back. Even before EFT-1, we saw what we call a pendulum effect in the parachutes. Under two chutes, when the vehicle would get a wind gust, it didn’t give us the landing orientation we needed. That was a surprise. And that’s one of the reasons we test: we see if there’s any behavior we did not predict. Subsequently our parachute team, guidance and control team, and aerodynamics team went back and looked at the problem. Through analytical work and modeling they were able to recreate that condition, which allowed us to understand what we needed to do to modify the system to protect against the pendulum effect. We figured out that we could do some early reaction control firings to damp the effect and mitigate it. Another way might be to let the vehicle fall a little faster because it becomes more stable when it falls faster. But then you’re trading more stability for a harder landing.
The only real surprise we got on EFT-1 wasn’t a parachute problem—it was that we didn’t get all of our inflation bags to work. We were supposed to get five to inflate and we only got two and a partial. Since last December, we have spent a lot of time looking at why the bags didn’t work the way we expected. We’ve modified the bags themselves, the bladders, and the container that they’re all stored in, which sits inside the gusset. Now we’re getting ready to go into testing on that new design to prove to ourselves that the changes we made will make that system more reliable and more robust.
APPEL News: So it sounds like everything’s moving ahead smoothly. Were there any other surprises from the development testing or EFT-1?
McClung: Actually, the public response to EFT-1 was the biggest surprise. The level of response was really phenomenal. The day after the launch, my boss and his wife were at Universal Studios, and he had his Orion shirt on. People would come up to him and say, “You were the guys who just did that NASA launch yesterday!” Everyone was saying how great it was. At the same time, a different group of people from the Orion team was flying home. There were 10 or 15 of them on the same plane. They actually got a round of applause on the aircraft. It was fascinating that we got that level of interest for a two-orbit unmanned test flight. It was a really good feeling to have been involved in something like that.
So it was great, it was warm and fuzzy for a few days after EFT-1, and then we said, “Okay—let’s go build the next one.”
Read a previous APPEL News interview with McClung following Orion’s successful maiden voyage.
Watch a video of the successful August 26, 2015 test of Orion’s parachute system.