By Svetlana Shkolyar
New specialized tools that improve existing processes or address new issues can make space launch preparations more effective. Developing those innovative technologies is the mission of the Applied Physics Lab (APL) at NASA’s Kennedy Space Center, but users influence the design of the tools and decide which ones will actually be used.
One example is the external tank (ET) vent hood alignment tool, used to align the vent positioned on the ET tip. This “beanie cap” prevents ice that might damage the orbiter during launch from forming on the vent. Engineer Jorge Rivera enthusiastically accepted it for use because he recognized that it would align the vent more safely and quickly than the existing process. Before the tool was available, technicians worked while strapped inside the hood—a hazardous operation that took as long as eighty hours. With the tool, alignment can be quickly and safely performed from outside the hood, not only before external tank propellant loading, but also with a loaded tank when a launch is scrubbed. Despite management’s concern that it needed additional capabilities, Rivera immediately saw its value.
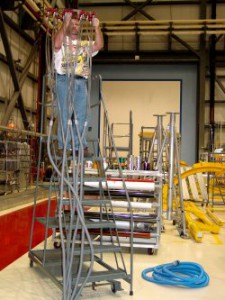
Technician Steve Parks of Arctic Slope Regional Corporation is testing the vacuum of the WET tool. This Plexiglas sheet has holes drilled into it to simulate the waterproofing holes on the shuttle tiles.
Photo courtesy Svetlana Shkolyar
A tool that aids the crucial task of leveling an orbiter in the orbiter processing facilities after missions was also in demand because the access platform system could damage a vehicle that is not perfectly level. The user, a NASA contractor from the United Space Alliance named Mike McClure, recognized the need for an improved leveling tool.
This improved orbiter jack and leveling system is memorable because, when funding was tight, the users and APL took the idea to the Kennedy shuttle processing chief, Michael Wetmore, and fought for it together. “Development of the improved orbiter jack and leveling system is an outstanding example of how groups from different organizations with different responsibilities can work together to achieve a goal even in times of tight funding,” remembers Charles Stevenson of the Shuttle Chief Engineers Office. McClure worked “hand in hand” with the lab to develop it, remembers Dr. Robert Youngquist, who got the APL running in 1989. Without McClure’s support, technically and politically, the system would never have been built.
“The idea for such a system came about many years ago, but no one was willing to champion it until I came into the group,” said McClure. “That is usually what makes or breaks a good project: a champion. You have to be willing to keep pushing.”
It is clear why he was so determined. The orbiter needs to be raised accurately to the height of the servicing platforms by jacks installed forward and aft, an operation that requires precision within one-eighth inch. The previous method of using calibrated measuring sticks consumed time, cost, and labor, and it was hazardous to tile safety. “It took 25 percent longer than with either of our laser systems,” recalls McClure. “From a timesaving standpoint, the laser systems were significant, especially when you add up the number of technicians and quality control inspectors involved with our operations.”
The system uses Leica laser rangefinders positioned at the four corners under the jacks and transmits the height readings to a central computer. It is a vital tool for the orbiter’s safety that would not have come about without the push from McClure’s group.
The water extraction tool (WET), a vacuum system for drying multiple orbiter tiles, is “a case where hardware is needed for contingencies,” said Dr. Youngquist. The tool was designed to remove water from orbiter tiles after the March 2001 Atlantis orbiter mission, which was rained on after landing at Edwards Air Force Base in California. WET is five times faster than the method used for Atlantis, which was dried by heating it with infrared lamps. It efficiently prevents launch delays and tile damage during ascent to the 20,000 tiles covering more than 180 square meters on the orbiter. The tool now dries 150 tiles in two hours, not days as before, by vacuuming water out through the needle holes in each tile that are used to inject a waterproofing compound.
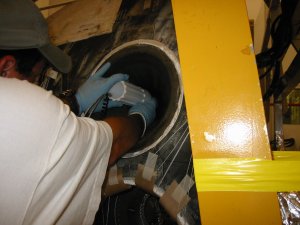
Quality assurance inspector James Allen Atwell is using the fuel hole inspection device to look into a nozzle in the Orbiter Processing Facility bay 2.
Photo courtesy Svetlana Shkolyar
The vacuum system also makes use of the facility’s vacuum cleaning system instead of using extra power for heat lamps. It allows faster temperature recovery, easier tile access, and clearer water flow visibility. “The Thermal Protection System team laughed when we first demonstrated the system; it was so much easier to use,” recalls APL physicist Stan Starr.
The team approved of the tool, but after it was developed, tested, and delivered, they “kindly asked us to keep our hardware,” recalled Youngquist, because shuttles are rarely rained upon. But in August 2005, Discovery landed at Edwards and encountered almost two inches of rain. “When users want something, things can move very quickly,” said Youngquist. A request for the tool was sent to the lab; within two weeks, WET was being used in the field.
Another APL technology that would not have made it into the field without the user’s active involvement was the Reaction Control System, or RCS, nozzle inspection tool. This checks the RCS for defects, which cost millions of dollars to remake and repair. The tools are made of Teflon to limit damage to the orbiter surface. “We worked closely with the inspectors and gave them a machined Teflon glove and a Teflon mirror tool with a mirror and eyepiece. It went through a few versions until they were satisfied that it met all their needs,” said Youngquist.
The RCS nozzle inspection tool replaced a flashlight and a boroscope tool, which were time consuming to use and failed to meet the desired capability. Today, three RCS tools are used at four sites, including the White Sands Test Facility that refurbishes thrusters.
Just as NASA Orbiter Maneuvering System engineer John Peters “took a hands-on interest” in the RCS project, Robin Floyd, lead window inspector, took a similar interest in developing the surface light optimizing tool (SLOT). SLOT saves money and time by efficiently highlighting tiny defects on orbiter windows. It took the lab only a few days to make a small plastic tool that attaches to the window via a suction cup and uses total internal light reflection with a prism to trap light in the glass. The light escapes at defects, showing the smallest damages to the windows, caused by micro-meteors, as bright points. Developing a tool with a large mirror makes the inspection “like looking through a big picture window,” recalled SLOT quality inspector James Atwell.
Floyd conceived the idea for SLOT independently but had no means of fabricating it on his own; he teamed up with APL and jointly produced the tool when a “meeting of the minds occurred,” said Youngquist.
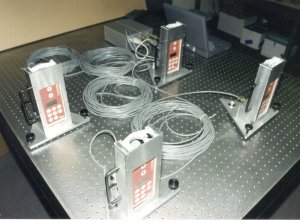
Four Leica laser rangefinders for the Improved Orbiter Jack and Leveling System.
Photo courtesy Svetlana Shkolyar
As a result, fourteen SLOT devices were delivered during the 2005 fiscal year and hundreds of potentially risky defects that the previous approach did not find were located. The SLOT will soon be adapted for use on the International Space Station and the Constellation project, which hopes to send the Ares I and V crew and cargo launch vehicles to the moon and Mars. It is now in its fourth generation.
In all, more than forty pieces of hardware have been developed at APL to assist shuttle program operations in the nineteen years of the lab’s operation. According to Youngquist, “the best case is when the end user wants to work with you and develops a vested interest” in making a tool. He adds, “Technology is a function of how ardent the customer is on getting the product; it is need and personality driven.” No one knows better than the user whether a particular tool will make his work easier and better. Listening to the customer is one important secret of successful technology development.
Some of this content was originally published on Space.com, for the Institute of Engineering Technology, and in NASA Kennedy Space Center’s Spaceport News.
About the Author
![]() |
Svetlana Shkolyar is a science communication graduate student, researcher, and writer. |