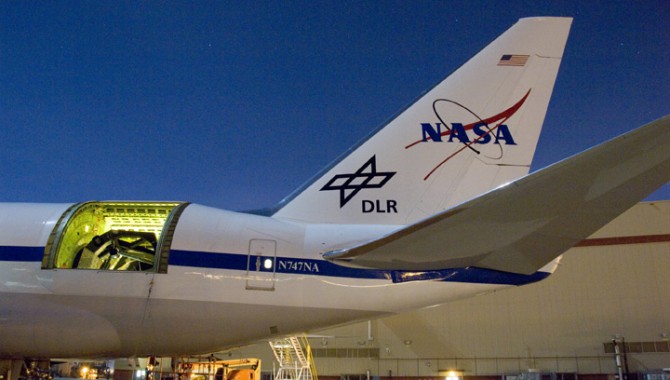
The SOFIA airborne observatory's 2.5-meter infrared telescope peers out from its cavity in the SOFIA rear fuselage during nighttime line operations testing. Photo Credit: NASA
January 31, 2011 Vol. 4, Issue 1
There’s no clear path to become a top systems engineer, but as three engineers experienced, learning on the job is an important part of the process.
The Systems Engineering Leadership Development Program (SELDP) provides opportunities for a small class of high-potential candidates to develop and improve their systems engineering leadership skills and technical capabilities. A core feature of this yearlong program is a hands-on developmental assignment. These experiences, which take place away from a participant’s home center, lead to a broader understanding of NASA and expand his or her systems engineering experience.
ASK the Academy tracked three members of the 2009-2010 SELDP class throughout the year as they adapted to the challenge of working and learning in a new setting.
Learning Every Day
“Fast” is the word that best describes Tom Simon’s SELDP experience working at Marshall Space Flight Center (MSFC) on the Fast, Affordable, Science and Technology SATellite (FASTSAT), a microsatellite designed to carry six small experiments into space. Having served as a subsystems engineer at Johnson Space Center since 2001, Simon went from a program with thousands of employees to a project so small that everyone on the team could stand around the satellite.
Coming from eight years in the space shuttle program, the difference in scale was a learning experience. “If I had a question about how we mate to the launch vehicle with the satellite, I know exactly who to talk to,” he said. “The family size of the project allowed the advantages of a co-located R&D effort even when we applied it to the development of a spacecraft.”
FASTSAT also operated completely differently than the systems that Simon was accustomed to working with. “There were almost no moving parts, and no fluid systems,” said Simon, who spent most of his career working on mechanical and fluid systems. He found himself troubleshooting electrical problems and software bugs. “The day-to-day work was in technical disciplines, which forced me to grow.”
As the new kid on the block, Simon found that his colleagues were glad to help him get up to speed. “Even though I wasn’t coming in on the same page that they were on, I tried to make it very clear that I cared about the success of the program,” he said. “As long as that connection is made, folks don’t mind helping you catch up–especially if they see you as someone who can help them too.”
The schedule also represented a new way of working for Simon. FASTSAT had a 12-month project lifecycle. Processes were streamlined to where decisions were made in weeks, not months. “Most of the projects that I’ve worked on I’ve had intended launch dates a few or several years away,” said Simon.
Working under such a fast-paced schedule shifted his approach to projects. “Every project I join now I’m going to start with the perspective of ‘What do we need to do?’ and not necessarily ‘What have we always done?'” he said. “I’ll never be the same again.”
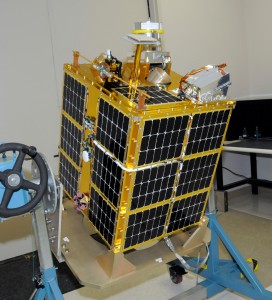
The FASTSAT-HSV01 spacecraft designed to carry multiple experiments to low-Earth orbit.
Photo Credit: NASA
To keep pace with the schedule, testing took place nearly every day. “We had to basically get to the test phase earlier than any of us usually get to [it], and let the data speak for itself,” Simon said. During the thermal vacuum test, the team was reviewing the output signal from the flight transceiver when they noticed a discrepancy that likely would have led to a failure. “One thing I learned from this project is that even if you’re trying to do things affordably and quickly, you don’t skip these meat-and-potatoes tests,” he said. “We could have spent six months analyzing the system, and we never would have found the transceiver issue. Instead, in a few days of testing, we found it.”
As the project wrapped up and awaited launch, Simon authored a lessons learned document for the team. He saw it as a resource for future work at NASA’s manned spaceflight centers. “Once the Shuttle is retired and the Station is complete, there are going to be a lot of people working on systems that need to be approached differently than the way we’ve worked in the past,” he said.
Working on FASTSAT helped Simon fill a gap in his experience between working on the Shuttle and R&D work earlier in his career in a lab setting. “I don’t think they (the SELDP team) could have picked a better assignment, team, or organization for me,” he said. “If the first 10 years are any sign, I’ll be learning every day until I retire.”
Leading from the Middle
Cynthia Hernandez knew the SELDP year demanded that she remained focused on meeting the goals she’d set for herself in the program. As a software engineer from Johnson Space Center, she enjoyed the challenge of working on an aeronautics flight project when she became the Deputy Chief Engineer of the F-18 research program at Dryden Flight Research Center. “Coming from a human space flight program, it’s very rare that you actually get to see the hardware you’re working on,” she said. The F-18 project met her SELDP job assignment goals, but it did not address her leadership goal, which called for her to lead a team.
Hernandez sought the guidance of her SELDP support team, and ultimately reached a decision to seek a new assignment. Stephen Jensen, the SELDP Advocate at Dryden and Chief Engineer of the Stratospheric Observatory For Infrared Astronomy (SOFIA), an aircraft-based observatory, and he identified a need within his own project that would enable Hernandez to meet her goal.
In March 2010, she joined SOFIA as it approached its final stages of integration and testing before its first test flight. Hernandez’s job was to lead the Observatory Validation and Verification (V&V) Working Group, a 10-person team with responsibility for developing the V&V test procedures and executing the tests properly. “It was my responsibility to organize and develop the team, help them work together, and help each other out to accomplish our tasks,” she said.
“I have a lot to learn in such a short period of time” said Hernandez at the beginning of her work on SOFIA. In addition to having never formed or led a team before, she had to bring together a diverse group, including senior engineers and scientists from Ames Research Center, the Germany Aerospace Center (DLR), Deutsches SOFIA Institute (DSI), University Space Research Association, and Dryden, to agree on test procedures. She also had to coordinate the writing of procedures, another new experience, which meant finding someone with the necessary expertise even though she had a very limited network at Dryden. In short, she faced the challenge of learning to lead from the middle–the team was her responsibility, yet she had very little formal authority.
“They were each so busy trying to meet their own milestones,” she said. “Initially it proved difficult to find people to write test procedures.” She happened to read a test procedure from another group that she found particularly well written, and she asked her boss, the Chief Engineer of SOFIA, if he knew its author, Cathy Davis. When he indicated that he did know her, Hernandez said she wanted her on the team. “She really played a key role in pulling the procedures together.” Hernandez, Davis, and a small core team made sure that the right procedures were in place and that the team didn’t waste time on unnecessary ones.
Hernandez ultimately led the team through a four-day observatory checkout process before scientists came aboard to do their own tests of the instruments. She then began work on the test plan for the 003-level (the highest level) of integration testing for the overall observatory. Shortly after her assignment ended, SOFIA achieved “first light” — the observatory was successfully activated in flight.
Looking back on her assignment, Hernandez learned a great deal from the process of working across organizational and cultural boundaries. “Working with different cultures and different organizations gave me the opportunity to broaden my way of thinking and approach to solving problems,” she said. As NASA’s missions increasingly involve international partners in critical path activities, that lesson is likely to pay dividends many times over.
The Value of Constructive Paranoia
Going from aeronautics research at Langley Research Center to a large spaceflight project at the Jet Propulsion Laboratory (JPL), Michael Lightfoot felt like he had travelled to another planet. At JPL, the lexicon everyone used sounded familiar, only it carried a different meaning. Team members seemed to intuitively know what to do, like bees in a hive. “You don’t know how they know what they’re doing or what they’re supposed to be doing, but it happens,” he said.
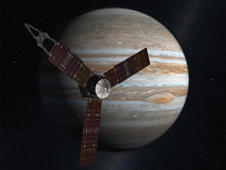
Artist concept of Juno spacecraft in front of Jupiter. With its suite of science instruments, Juno will map Jupiter’s intense magnetic field, investigate the existence of a solid planetary core, measure the amount of water and ammonia in the deep atmosphere and observe the planet’s auroras. Image Credit: NASA/Jet Propulsion Laboratory
His SELDP assignment brought him to the Jupiter Uranus Neptune Outreach (Juno) mission, a billion dollar international project. From the beginning, he took care to watch the people around the center to uncover the source of the invisible “playbook” that seemed to be ingrained in the team. “I’ve come to the conclusion that the processes, the rules, and the requirements serenade a point from which discussion can begin,” he said, “but the real glue that holds it all together is the people.”
Lightfoot, who spent a large portion of his assignment working on verification and validation (V&V), saw the value of “constructive paranoia,” which kept the team on its toes. “No one wants a failure to happen while they’re on deck, or at any time, so people are constantly looking for avenues to make improvements that actually aid the confidence that the spacecraft’s going to do what they expect it to do.” Certain people within the team picked up on concerns or issues, evaluated them, and generated detailed solutions or scenarios to determine how they would affect mission success–that is, focusing on the value of the science that would be collected.
For instance, the team realized that it could decrease ground control costs by putting the spacecraft into hibernation mode at times when it would not be collecting data. At the same time, they recognized that while this offered a savings in cost, it also posed the risk that the spacecraft might not awaken from its sleep mode. Solutions included developing a “phone home” capability if Juno ran into trouble, and also prompted debate concerning how such changes would affect the design of the spacecraft. Thinking about cost in this way, “forces people to think differently to come up with good alternative engineering solutions,” he said. Lightfoot, who prior to this assignment was accustomed to developing an instrument that was then shipped off for installation elsewhere, appreciated the opportunity to participate in the system-level evaluation of a mission.
Lightfoot’s overall understanding of systems engineering changed during his rotational assignment. “I thought I knew what it was when I went away,” he said. “I got a more complex picture of what it could be at JPL.” His key insight related to the high level of integration on most NASA projects today. “Some of the things we’re taking on now are so highly coupled that if you try to decompose them and ship work off to traditional engineering disciplines, you run the possibility of locking in a design too early, and shooting yourself in the foot without knowing it.”
His SELDP experience added another challenge to his day-to-day work as an evolving systems engineer. “It’s hard to put the genie back in the bottle,” he said about learning to work at the systems level. “I’ve seen a lot and there’s an awful lot I want to share.” He aims to share his experiences with his Langley and other agency coworkers to “make sure we put some things in place that enable us to sustain ourselves.”
The SOFIA airborne observatory’s 2.5-meter infrared telescope peers out from its cavity in the SOFIA rear fuselage during nighttime line operations testing.
Featured Photo Credit: NASA